The Steiner TOR-X: Laser Aiming with the Mantis Dry-Fire Training System
Mantis calls its latest hardware release “The Ultimate Mantis-Steiner Fusion.” Even though as far as I know this is the only Mantis-Steiner Fusion, I suppose they can be given some allowance for hyperbole, as its collaboration with Steiner (a respected German optics/laser company now a part of the Beretta Group) resulted in the TOR-X.
The TOR-X is the first handgun-mountable aiming laser system to be integrated with MantisX technology (the same as is in a Mantis X10 Elite unit).
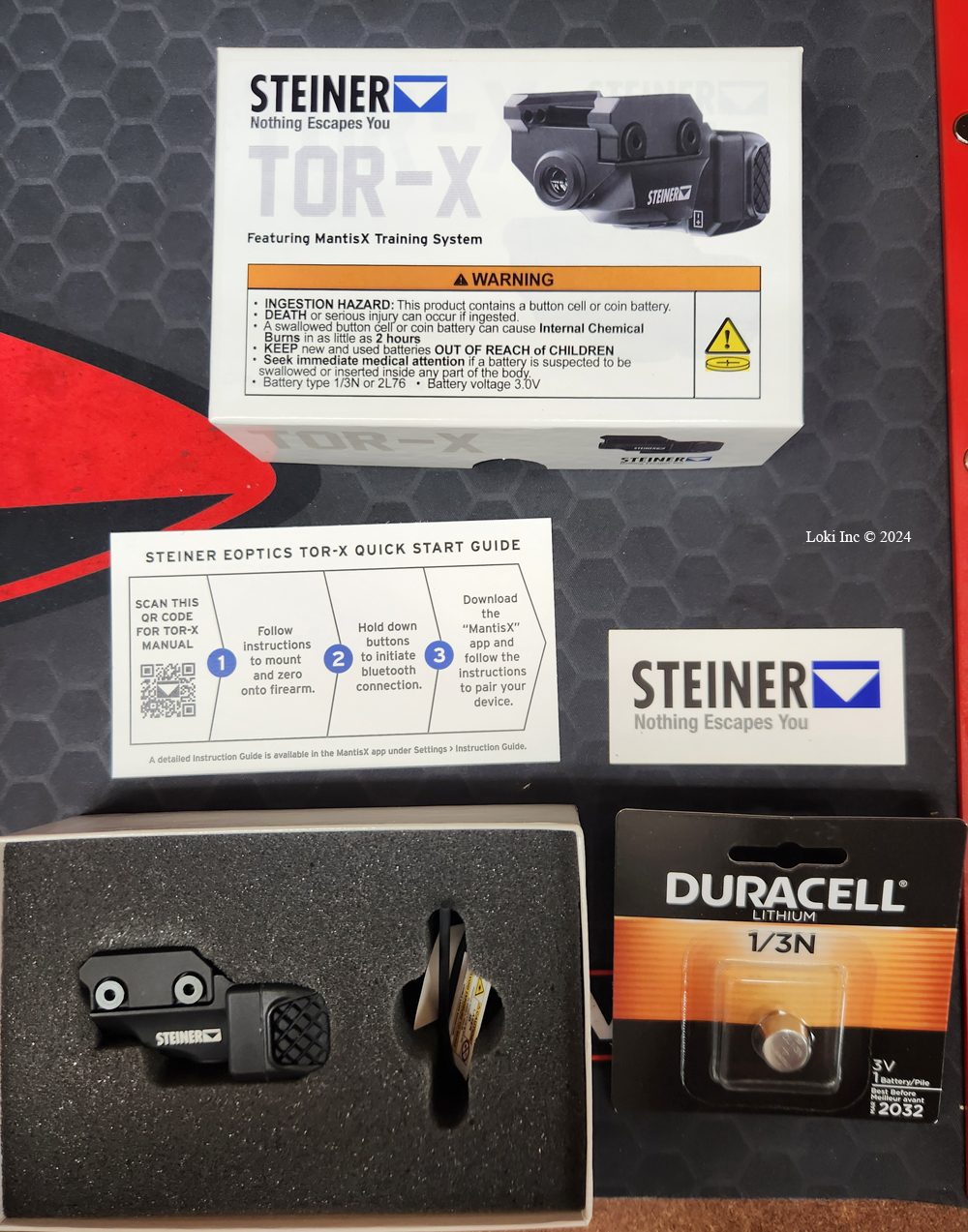
TOR-X box and contents
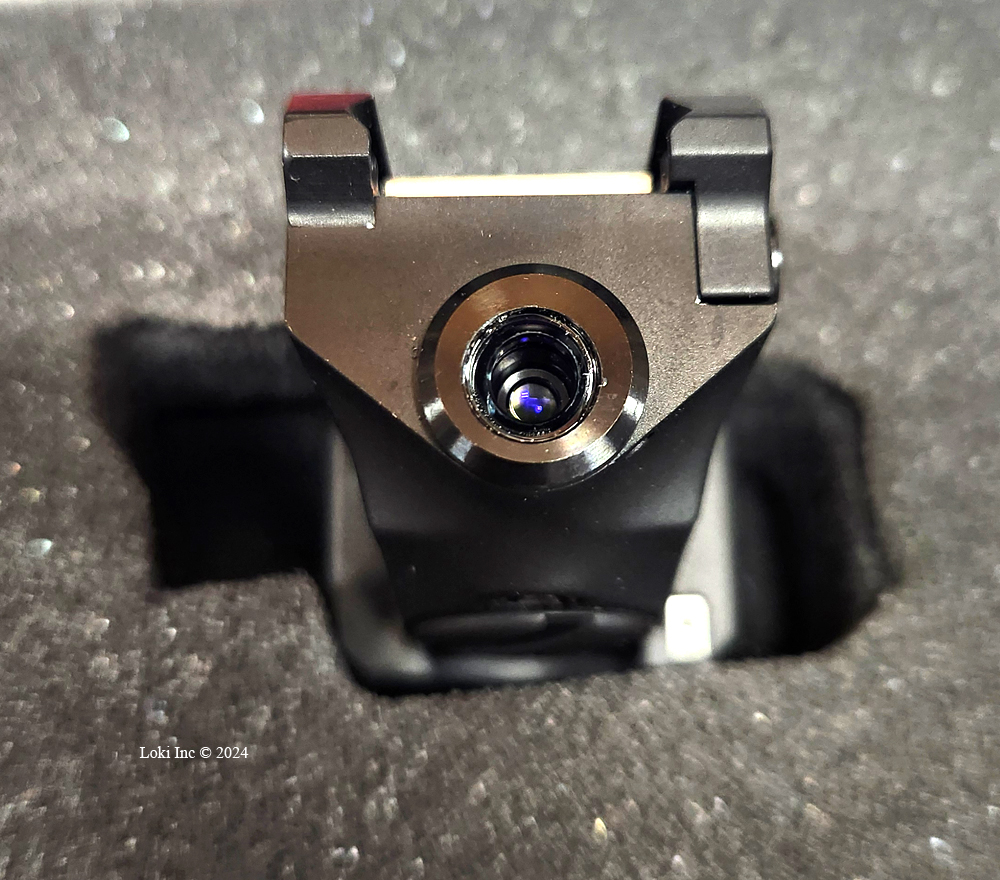
Front end of TOR-X showing laser aperture
Mounting a TOR laser pointing device and a Mantis X10 Elite on the same handgun rail mount is not feasible on most handguns; there simply isn’t enough room on the rail. The TOR-X allows a shooter to have both systems in a package that will fit on most forward undermount rail-equipped handguns.
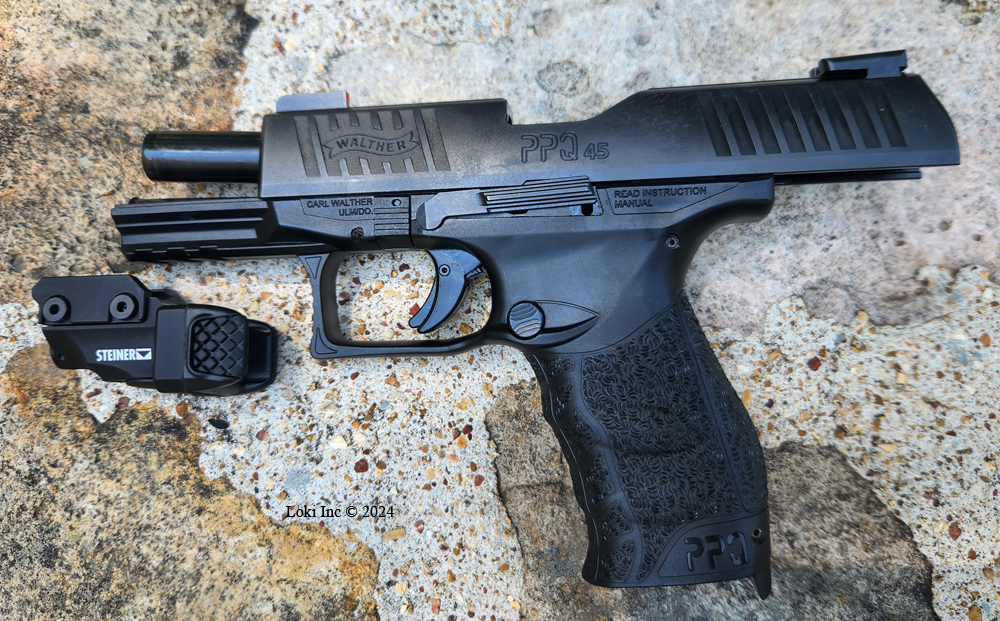
Walther PPQ 45 and unmounted TOR-X
I’ve written about MantisX systems in a previous blog post, and for additional information see my post about the BlackbeardX training system, which integrated the Blackbeard AR-15 training system with MantisX technology. As such, I won’t repeat myself – please refer to the previous blog posts for information about MantisX dry fire training and how to operate the associated systems.
In my earlier blog posting, I explained why the MantisX system is an excellent aid to learning proper handgun grip and trigger management. Adding the technology to a dedicated laser aiming system in the TOR-X package, which is small enough to be deployed effectively from the forward undermount rail location of a handgun, has not changed my opinion of the Mantis concept. Also, fortunately, the system will fit into a holster that accommodates the particular pistol plus a light mounted on the aforementioned forward rail, thereby allowing full use of the different training programs available with the Mantis smartphone application.
Mantis continually upgrades the smartphone application that takes data from MantisX and then provides to the user pointing direction up to trigger break, shot analysis, and a trace of pistol movement from the start of sight hold on target through shot break and recoil (if used in a live fire exercise). All this capability is inherent in the TOR-X system due to its MantisX technology.
Having the capability of laser aiming while using MantisX for shot monitoring and handgun mastery training expands the latter dimension of the Mantis concept. Not only can you use the MantisX for dry fire training without the laser, or the laser for aiming at a target during live fire, but you can use both MantisX and the laser when doing either type of training to help diagnose difficulties you may be having with your grip of the gun, trigger management prior to shot break, and recoil management afterwards.
Steiner TOR-X Fit on Guns
Having a large array of handguns at my disposal, I checked the fit of the TOR-X on a number of them in order to give the reader an idea how well the system would integrate with a particular gun. Some of the designs I checked are no longer in production, but are in use so I didn’t exclude them from my examination. A photograph of each fit check is below.
Walther PPQ 45, .45 ACP caliber. Good fit, but laser pointing cannot be elevated enough to coincide with the point-of-aim (POI) at 7 yards. The laser spot at 7 yards is about 2 inches low.
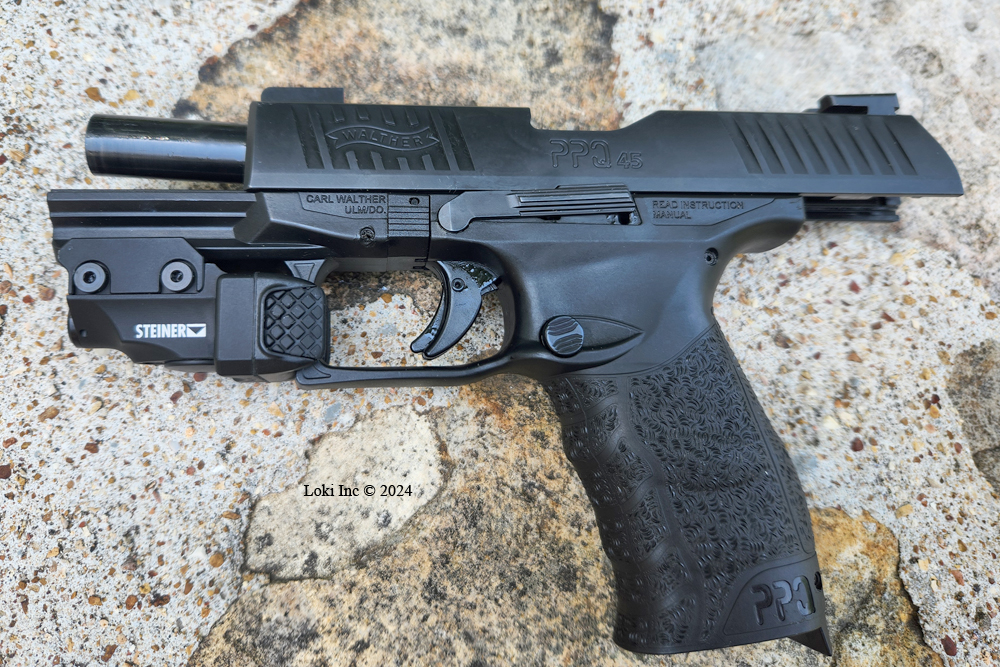
Walther PPQ 45
SIG Sauer P220, .45 ACP caliber. Good fit and pointing capacity.
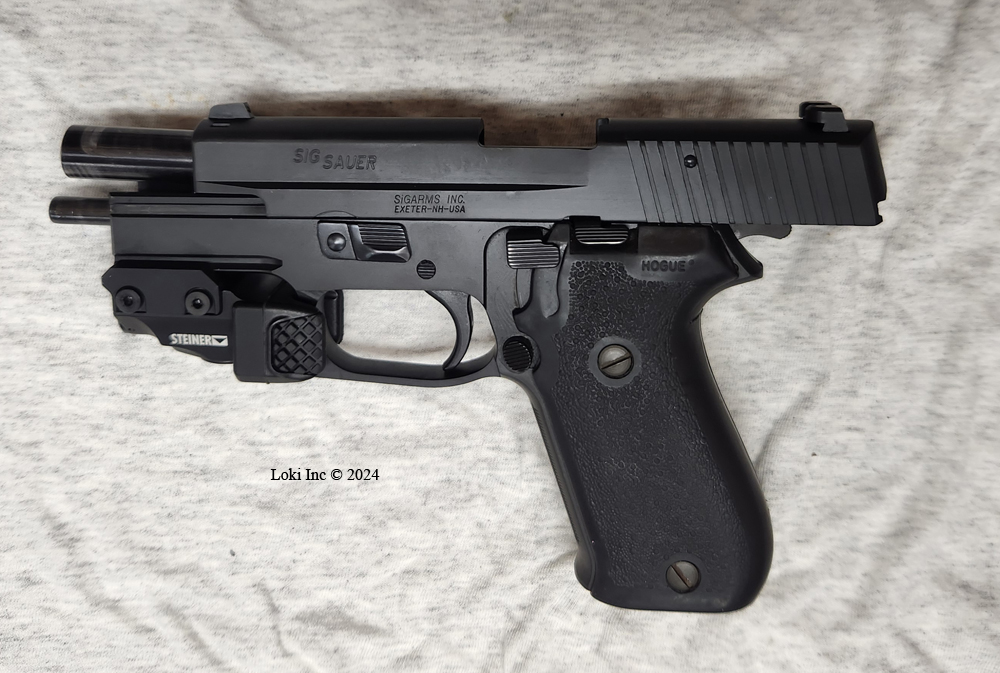
SIG Sauer P220
Glock 22, .40 S&W caliber. Pointing capacity good, TOR-X mount cross-pin had to be force-fitted into the rail groove.
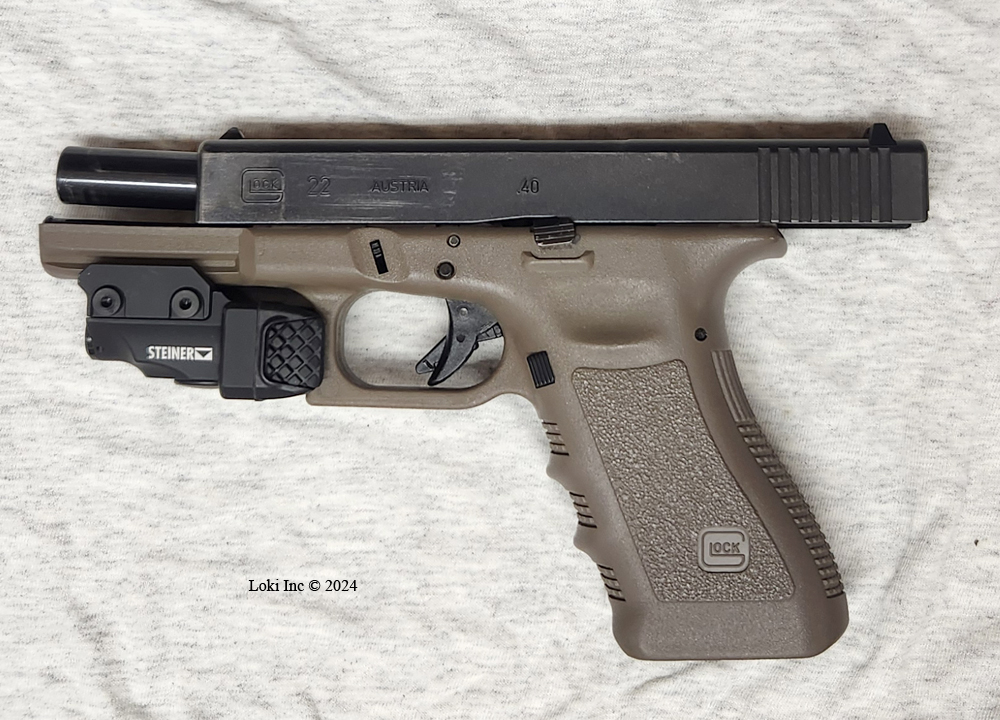
Glock 22
S&W M&P 40 Performance Center, .40 S&W caliber. Good fit and pointing capacity.
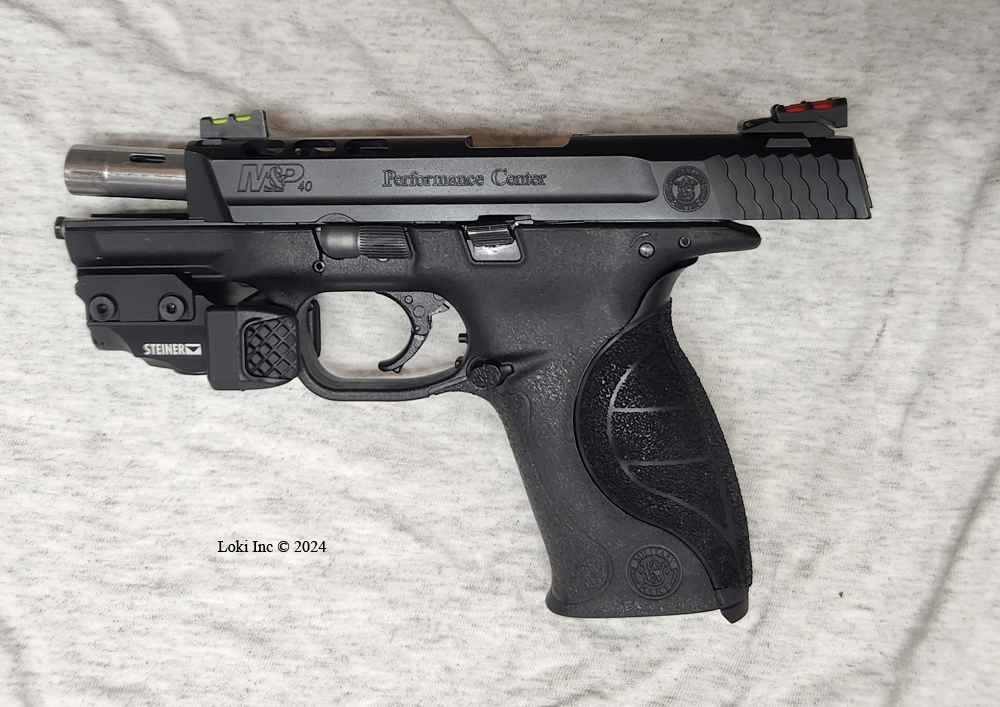
S&W M&P 40
Walther PDP, 9 mm Parabellum caliber. Good fit, but laser pointing cannot be elevated enough to coincide with the POI at 7 yards. The laser spot at 7 yards is about 1 inch low.
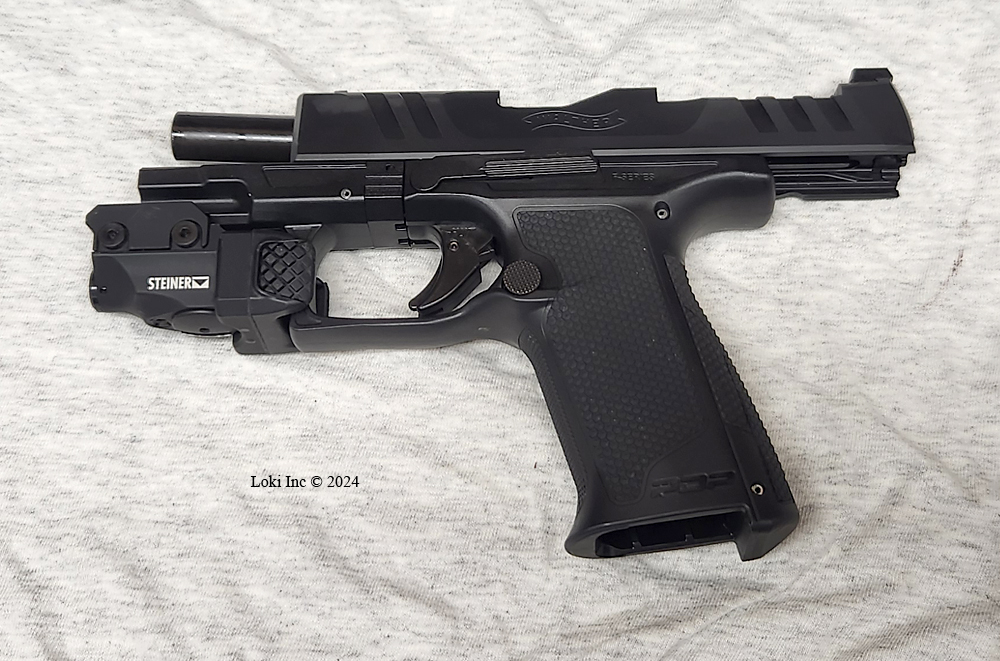
Walther PDP
Remington RP9, 9 mm Parabellum +P caliber. Good fit and pointing capacity.
Remington RP9
Ruger 57, 5.7 x 28 mm caliber. Good fit and pointing capacity.
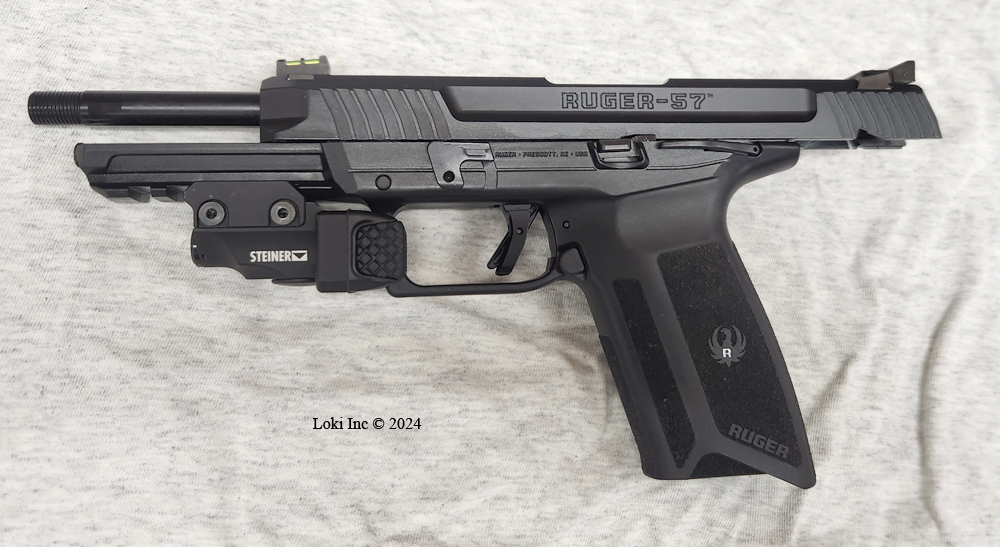
Ruger 57
SIG Sauer Mosquito, .22 Long Rifle caliber. Good fit and pointing capacity.
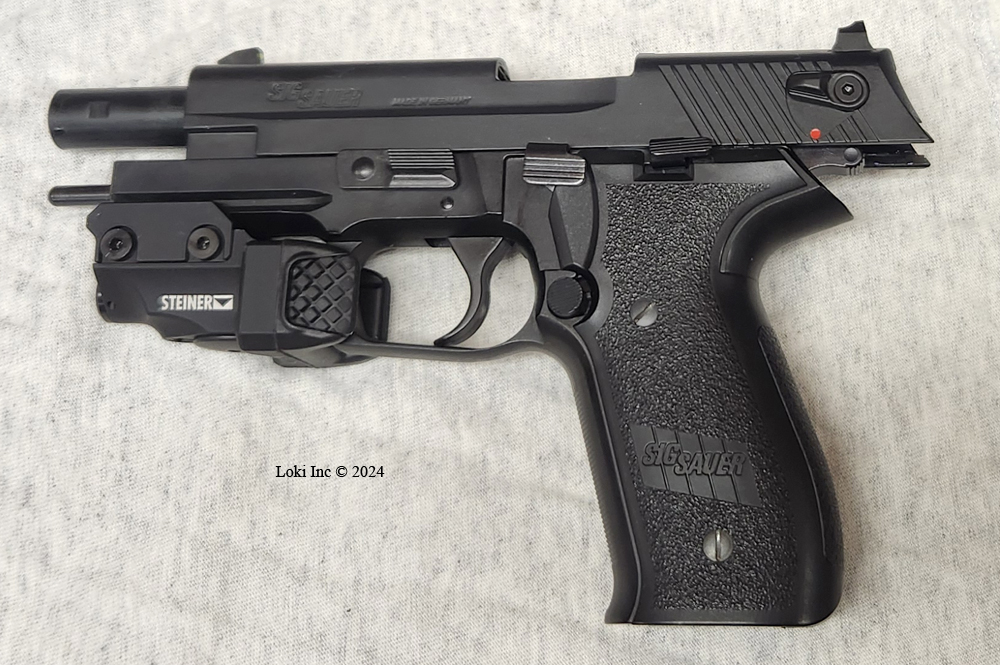
SIG Sauer Mosquito
Ruger SR22, .22 Long Rifle caliber. Good fit and pointing capacity.
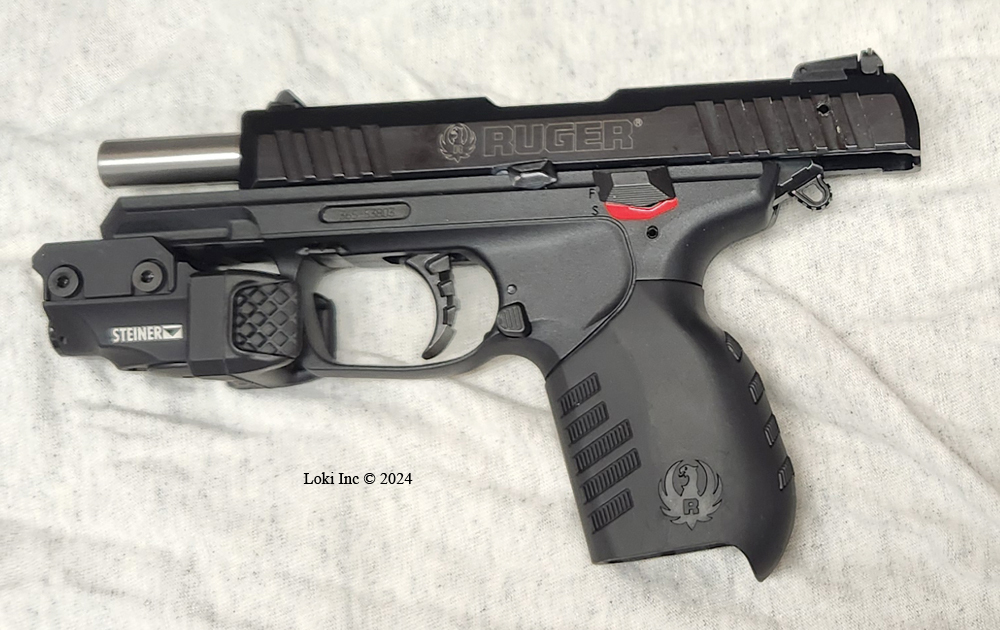
Ruger SR22
Taurus TX22, .22 Long Rifle caliber. Good fit and pointing capacity.
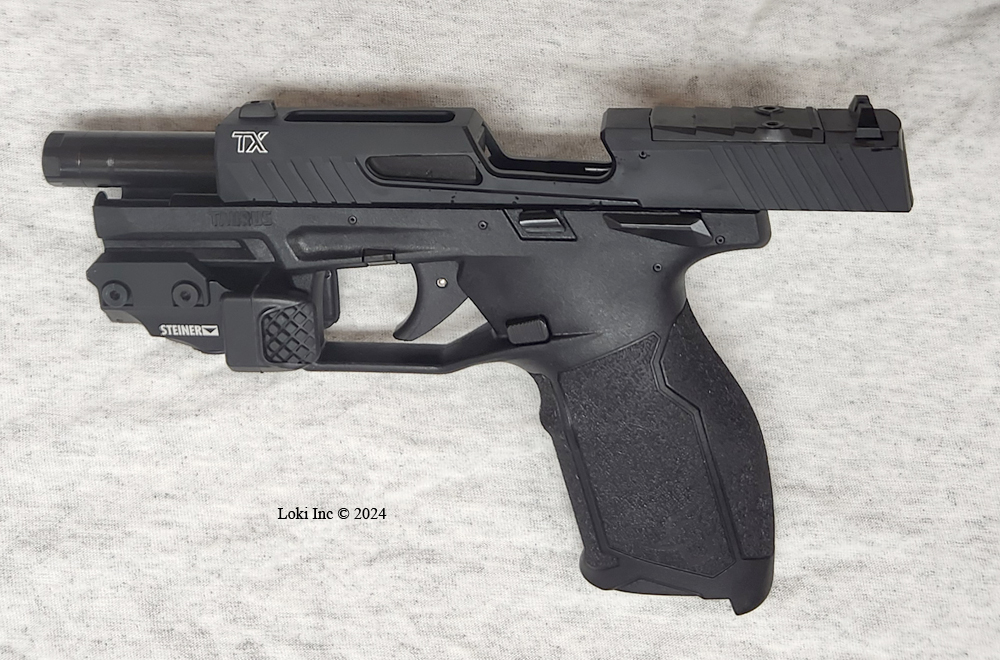
Taurus TX22
Note: For the Ruger SR9, 9 mm Parabellum caliber, the TOR-X mount cross-pin was too big to fit into the rail groove without filing the groove or the cross-pin. I didn’t do either for the purpose of this brief exam, but would file the groove to open it up if I wanted to dedicate the TOR-X to this gun.
When installing the TOR-X, it is critical to pay close attention to, and to follow, the rail mounting instructions in the User Guide. If you are not careful to align the cross-pin with the correct and corresponding holes in the mount and in its clamping bar, you will not be able to tighten the mount to the rail sufficiently enough to keep the mount from moving and possibly departing the gun if live firing. At the very least, the system cannot provide good accelerometer data if its sensors are slopping around on the gun in ways that don’t correspond to your grip and trigger management.
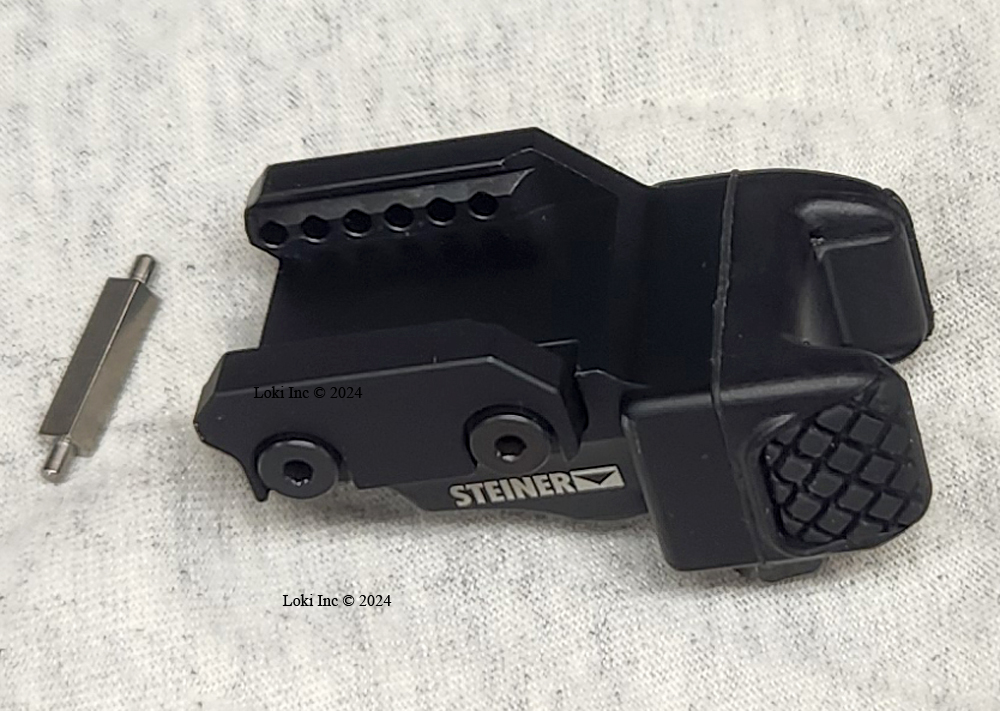
TOR-X showing cross pin and its mounting holes
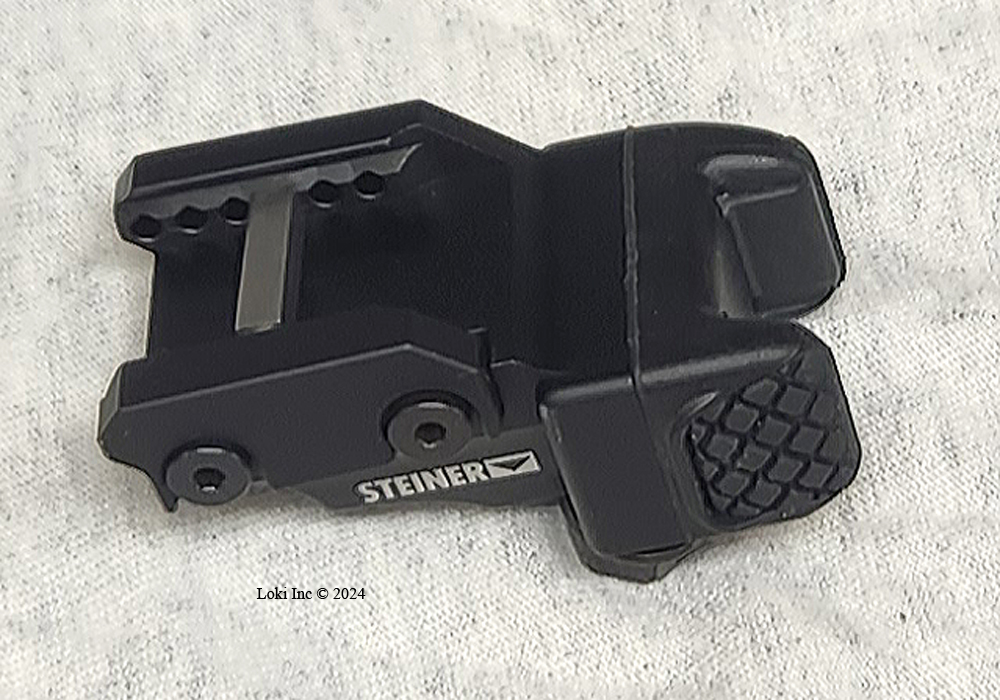
TOR-X showing cross pin in place
For more information about the TOR-X, visit the Steiner website. The TOR-X is distributed by Mantis, so you should visit their website for availability and purchasing information.
MSRP: $359.99
Rebarreling a Savage Axis II .25-’06 XP Hardwood Rifle
I decided to rebarrel my Savage Axis II .25-’06 XP Hardwood Rifle because I didn’t like the group size it produced using a good scope and very good ammunition.
If you haven’t already read my blog posting about reworking a 6.5 Creedmoor Savage Axis rifle, you may want to do so before reading this post because I’m not going to repeat the information about the rebarreling or scope mounting processes. I’ll just address the differences between the work I did on the Axis, which was much more extensive, and what I did on the Axis II.
The Axis and Axis II rifles are nearly identical, except the Axis II comes from the factory with their AccuTrigger and a Bushnell scope, whereas the Axis comes with a standard trigger and a Weaver scope (see the Savage Arms descriptions here). As in the case with the Axis rifle, I won the Axis II at an NWTF benefit banquet. Unfortunately, the similarities between the rifles extended to the conditions of their rifle bores!
I already had an excellent .25-’06 Ruger M77 Mk 1 rifle that I purchased at an auction many years ago. The seller said he sold it because it wouldn’t shoot accurately anymore, so I was able to buy it for a very low price. I took a look down the bore of the gun (this was in my pre-borescope days) before I bought it, and could hardly see the rifling for all the copper bullet material stuck in the grooves, so I figured the gun would be “a shooter” if I could get the bore cleaned of all that metal. After several days and iterations of using an electrochemical bore cleaning system that stripped progressive layers of copper, burned powder, and lead out of the bore I had a clean gun that returned to its previous glory. It is a “tack-driver.” So, I knew the caliber could produce very good and accurate results.
My excitement about winning a new .25-’06 turned to disappointment over a week or so when my new Axis II spewed bullets downrange into really crappy groups, even when combined with a quality SIG scope. It was as inaccurate as my old M77 before I de-metaled its bore! With the Axis II being a new gun, I didn’t think bore metal deposits would be a problem. This time, though, I had a borescope rather than my naked eyeballs to use for a bore examination. After checking all the other things that could be affecting the gun’s accuracy (bad scope, loose scope mountings, barrel in contact with the forend, loose/improperly torqued stock-to-receiver bolts and ammo variations), I borescoped the barrel and discovered similar problems to those I found with my Axis rifle. The craters and cavities in the one-third of the bore closest to the muzzle were worse than in the Axis
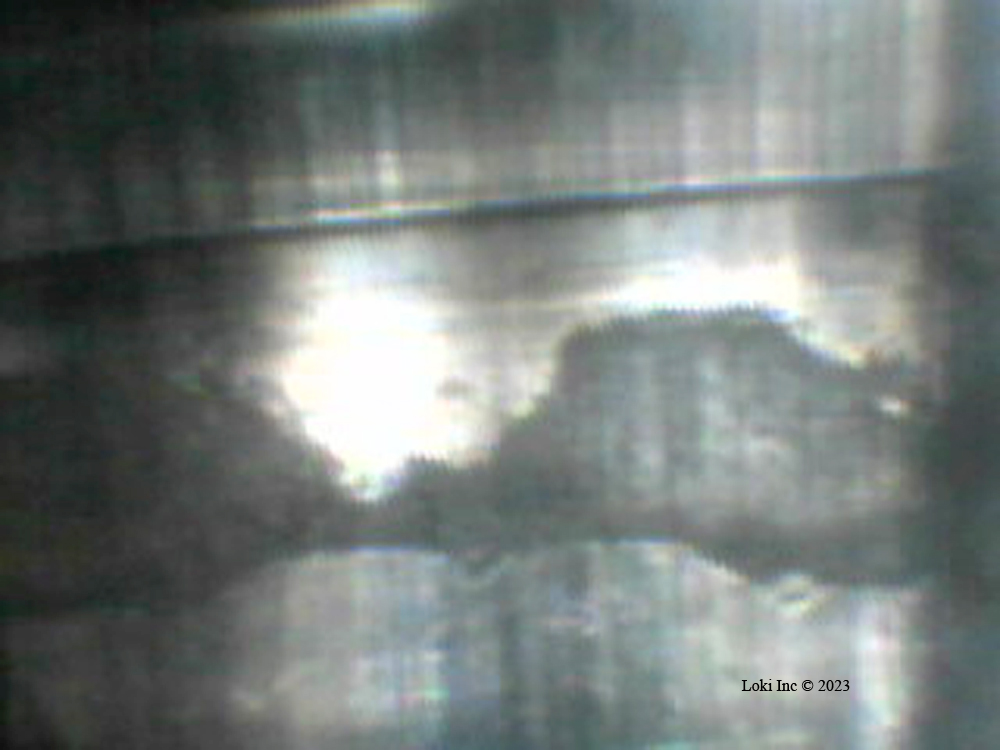
Cavity in bore
This mystifies me, as Savage rifles have a reputation for accuracy, and the two others I own (an older Classic Model 110 in .270 Winchester, and a 110 Precision in .338 Lapua Magnum) were very accurate right out of the box. I don’t know why the two rifles I won at benefit banquets were problem children.
Rebarreling a Savage Axis II .25-’06 XP Hardwood Rifle
The Axis II’s cost to me so far was just the raffle ticket, so I decided to invest some time and money into improvements. The XP stock is pillar bedded, and made of a nice hardwood with two darker cross pins fore and aft of the magazine well, and I like the AccuTrigger. I hoped that all I needed to replace was the rifle’s barrel, so I searched online and found an E R Shaw (now called Shaw Custom Barrels) .25-’06 barrel kit with a factory contour Savage barrel for sale. Shaw barrels are well known for accuracy, and the kit included a GO gauge and a NO-GO gauge as well as a Savage barrel nut wrench.
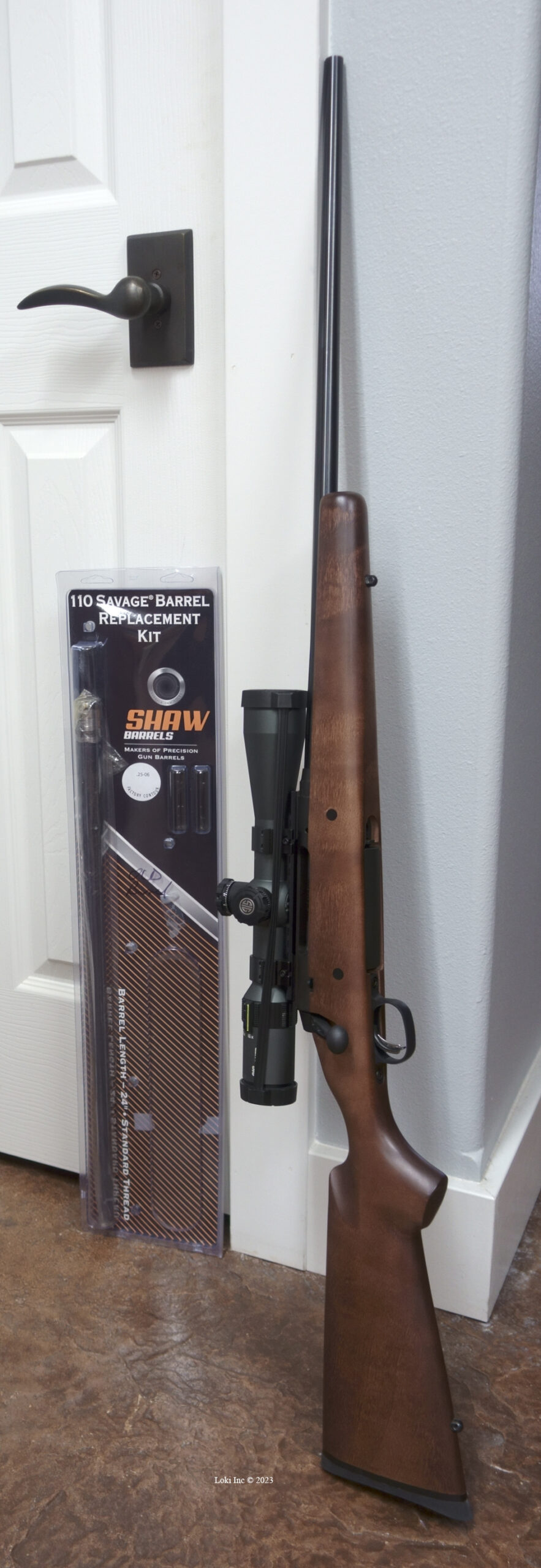
Original Savage Axis II rifle with Shaw barrel kit
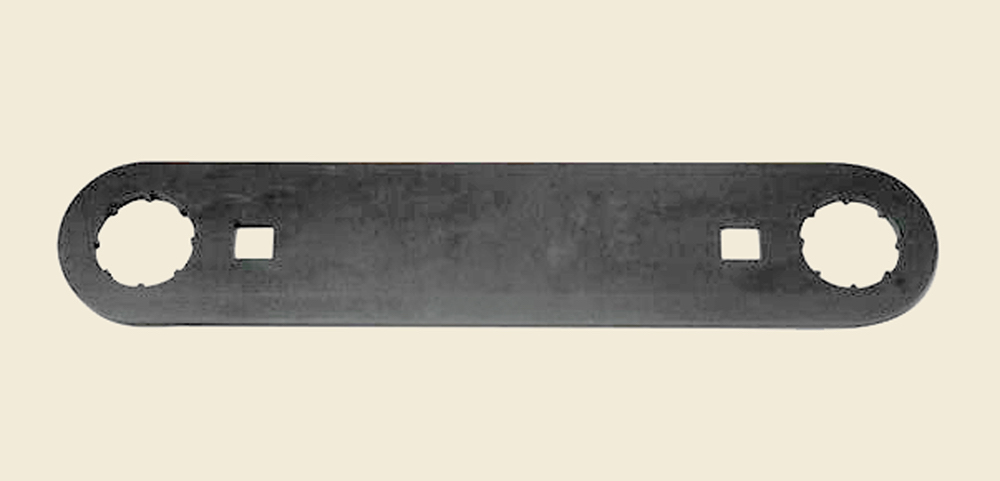
Savage barrel nut wrench-2
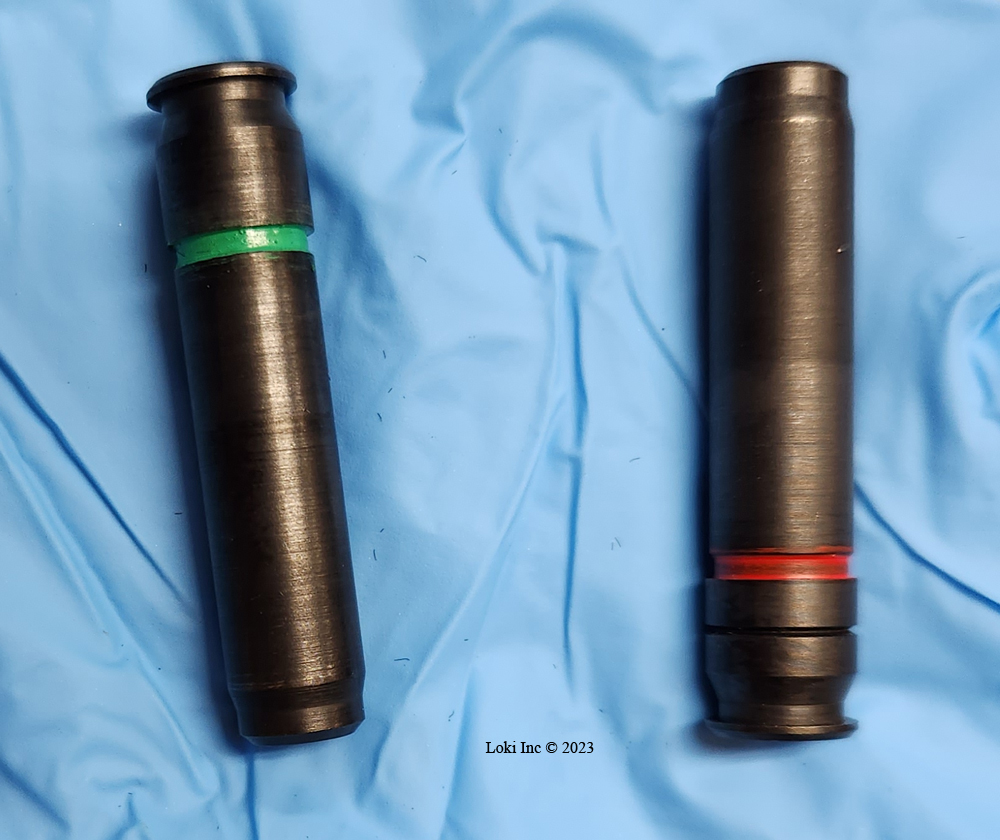
Headspace gauges – GO on the left, NO GO on the right
One of the many good things about the kit was its detailed set of instructions on installing the barrel. Even though I have installed Savage and Mauser barrels before, and knew the process, I still followed Shaw’s instructions to ensure I didn’t mess-up something. It behooves anyone barreling a firearm to be sure of the process, to avoid creating a dangerous situation with the wrong headspace.
Rebarreling the Axis II went smoothly. After removing the scope and its mounts from the receiver of the rifle, I removed the barreled action from the gunstock. I clamped my barrel vise in my big mechanic’s bench vice, and then after fiddling around a bit to decide which bushing to use in the barrel vise, I put some rosin on the rifle’s barrel. You don’t always have to use rosin to keep the barrel from slipping in the vise, but the inserts in my vise weren’t a perfect fit on the barrel so I needed to use rosin. At that point, to remove the barrel it was a matter of using the barrel nut wrench to remove the nut, and then sliding the barrel out of the action. Installing a new barrel included several important details, as addressed in the Shaw installation instructions, so I followed them closely. The barrel nut should only go on in one way, and the gun’s recoil lug has one way to install it. To achieve the required 75 to 100 ft-lbs of torque on the barrel nut with the GO gauge installed in the gun, I inserted the square driver part of my big torque wrench into the square cutout in the barrel nut wrench, and used the torque wrench/barrel nut wrench combination to tighten down the nut.
Even though the new barrel was noted to be the factory contour, when I seated the barreled action into the gunstock I noticed some interference between the barrel and portions of the stock’s barrel channel. As I mentioned in my 6.5 Creedmoor rebarreling blog, I prefer to have a business-card-thick gap between the barrel and the stock for the entire length. So, I got out my barrel channel scrapers and enlarged the forestock channel wherever needed to achieve that gap. I put a little sanding sealer onto the newly exposed wood in the channel to help seal it against moisture.
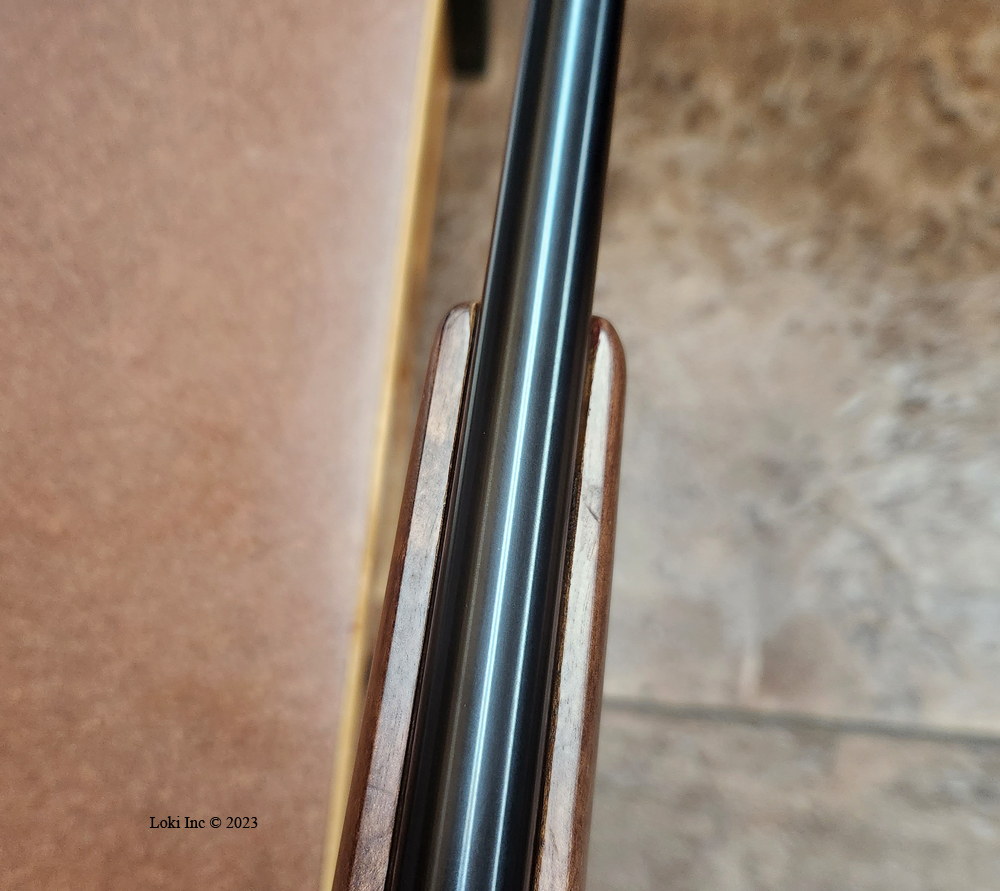
Barrel in forend showing gap
After re-assembling the rifle and re-mounting my scope on it, I thoroughly cleaned the gun’s bore.
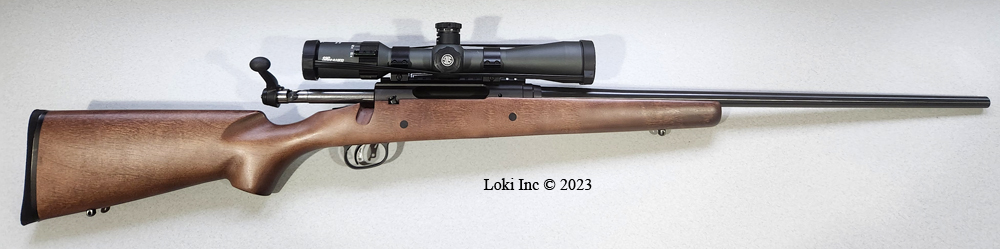
Completed rifle Savage
I was anxious to take the Axis II to the range to see if my work had made any improvement on the rifle’s accuracy, so I grabbed a couple of boxes of different brands of ammo, plus some of my handloads.
On the range, the rifle shot very well – its accuracy was a vast improvement over what I was able to achieve with the gun and its original barrel. Rebarreling it was worth the effort!
New front sight for S&W Model 327 or TRR8
I’ve had a S&W Model 327 TRR8 for several years, now, and it is one of my favorite guns to carry when I’m out and working on my Missouri Ozarks property. I never know when I might come across a four- (or two-) legged varmint that needs to be shot. Unfortunately, I had to replace the gun’s front sight.
Light in weight for a Smith N-Frame because of its scandium alloy frame, the TRR8’s stainless steel cylinder holds eight rounds of .357 Magnum ammo (or .38 Special if you wish for a bit less recoil) that can be full-moon clipped together for quick reloading of the chambers. Since I handload my ammunition, I typically chamber 158 grain JHP rounds loaded to a velocity that I know from experience will expand effectively in raccoon, groundhog, and armadillo-sized animals. As backups, I put two ammo carriers on my belt that can each hold a full-moon clip of .357; one clip has 180-grain solids hot-loaded for black bears, and the other has 140-grain FTX polymer tipped bullets loaded for deer-sized animals.
You can also single-feed the chambers, as the extractor star can pick up the cartridge rims for easy extraction. It’s called a TRR8 because it’s a “tactical rail revolver”, the cylinder holds 8 rounds, and the gun is finished in black.
If you wish to do so, you can install a short piece of Picatinny rail atop the gun for optical sights and another section underneath to attach a light, as the barrel shroud is drilled and tapped at the factory. I chose not to do either, as I want a rugged gun that I can carry in a hip holster when I’m dragging myself through briars and thorny bushes, and when I’m driving a cab-less tractor through the same sort of stuff. More stuff hanging on a gun means more stuff to hang-up in the holster, or in brush when I’m drawing-down on something.
My gun was from Smith’s Performance Center, and they fine-tuned the action so everything about it is smooth – it has a consistent, slick double-action trigger pull, and the hammer release during the single-action pull is like the proverbial “break of a glass rod.” I’ve lost count of how many armadillos, prairie dogs (during a trip to northern New Mexico) and other varmints I’ve killed with the revolver. While carrying it as a backup to my primary arm, I even killed an eight-point whitetail buck with it when (due to a failure on my part) my .30-’06 rifle was out of action.
So, what’s not to like about the TRR8? The interchangeable front sight, in my opinion, is a bad concept. I like iron sights on pistols, and the gun comes with a gold bead Patridge-type front sight blade that worked very well for me. I say “worked” because I lost two of them over the past few years due to the interchangeable design. As it turns-out, holster carry is anathema to this sort of front sight. My holster happens to have an open end at the part where the pistol’s muzzle resides, so twice at times unbeknownst to me when I re-holstered my gun out in the woods, the front sight blade caught on something inside the holster and removed itself. Of course, the blade proceeded to fall through the bottom opening of the holster to be lost in the leaf litter on the forest floor.
Unfortunately, I only had two sight blades from the start. The second time this happened was in the midst of the great Covid-everyone-stay-at-home-and-close-your-business lunacy. I called Smith & Wesson to order a replacement sight blade only to be told that they didn’t have any and didn’t know when they would have any more.
New Front sight for S&W Model 327 or TRR8
What to do? Well, with necessity being the Mother of Invention, I decided to build my own sight blade out of a piece of sheet brass scrap I had left over from another project. Of course, I could have used a hacksaw and needle files to make the blade, but I decided making the blade would be a good time to use my mini-mill and practice my detailed machining skills.
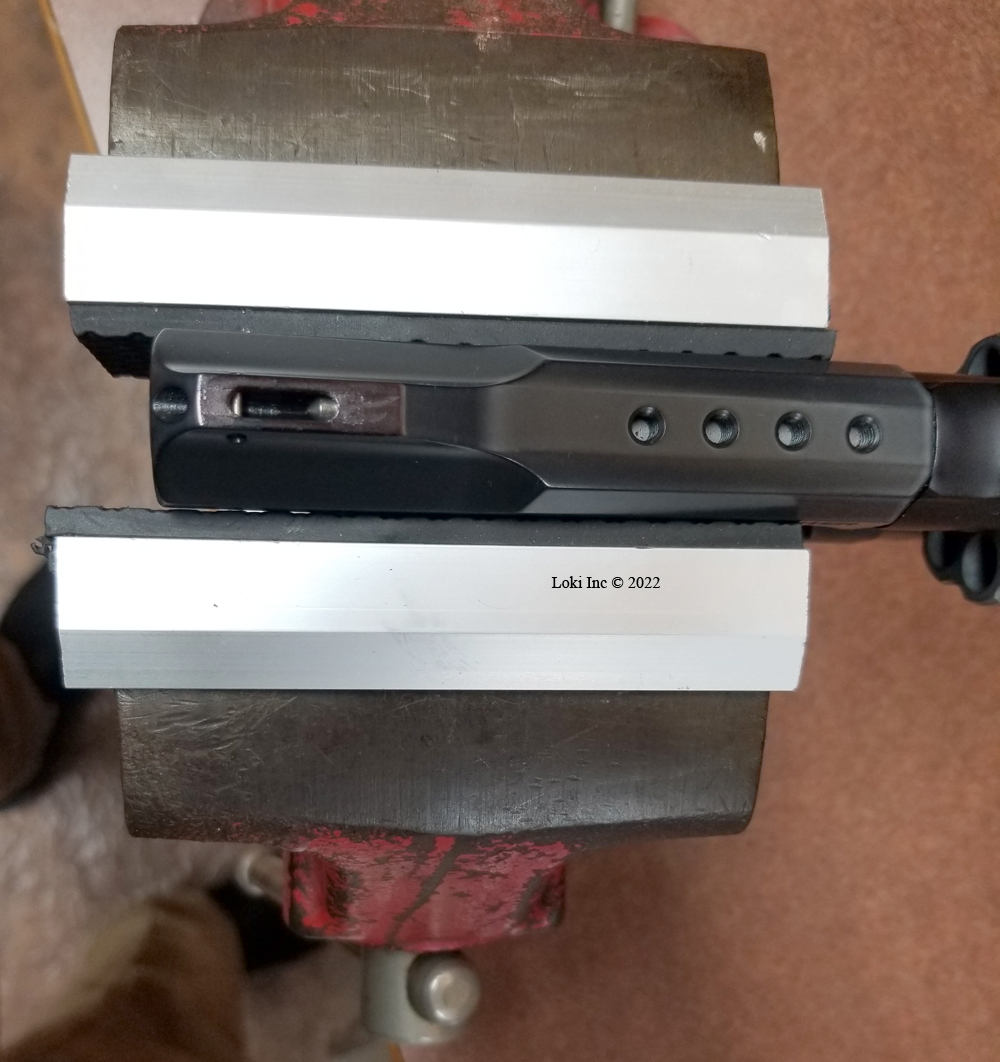
Empty front sight mount in barrel shroud
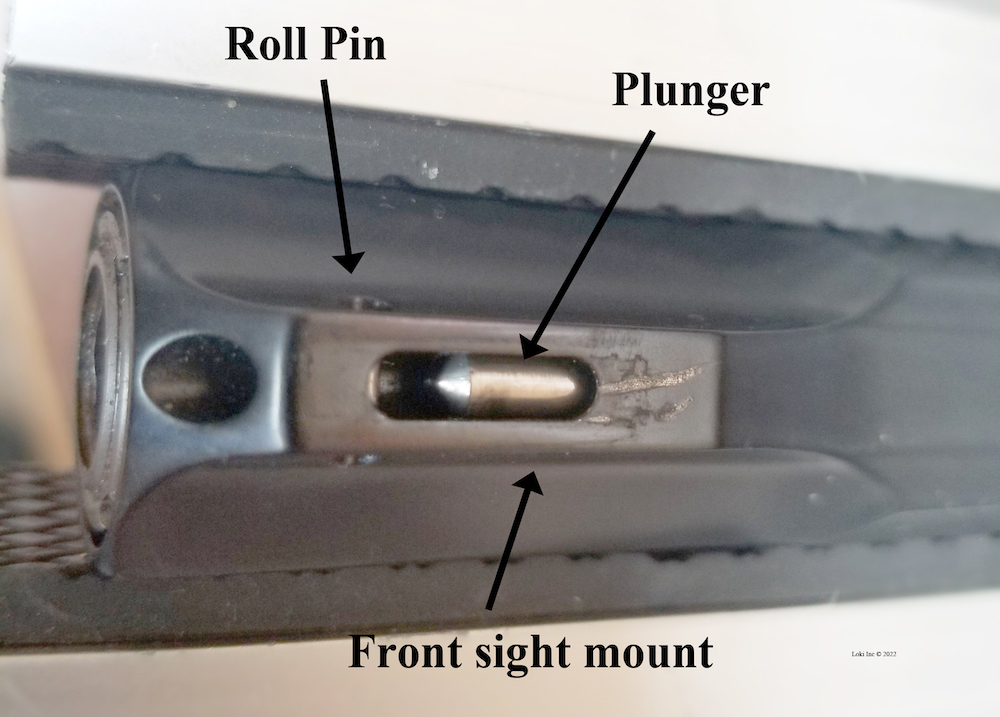
Front sight mount
The front sight mount in the revolver’s barrel shroud has a small roll pin in the front and a spring-loaded plunger in the rear, and the blade has corresponding notches to engage the pin and the plunger.
Measuring the dimensions for the base portion of the sight (the part that would fit into the front sight mount in the barrel shroud) was easy using a caliper; I paid close attention to the dimensions so I could get the front and rear lower angles right. If these front and rear angles aren’t correct where the sight hooks under the front roll pin and where it hooks under the plunger, the sight won’t stay engaged in the sight mount.
I used my metal cutting band saw to cut a rough representation of the sight shape from the brass strip, and then I used a small end mill in the mini-mill to finish shaping the sight blade.
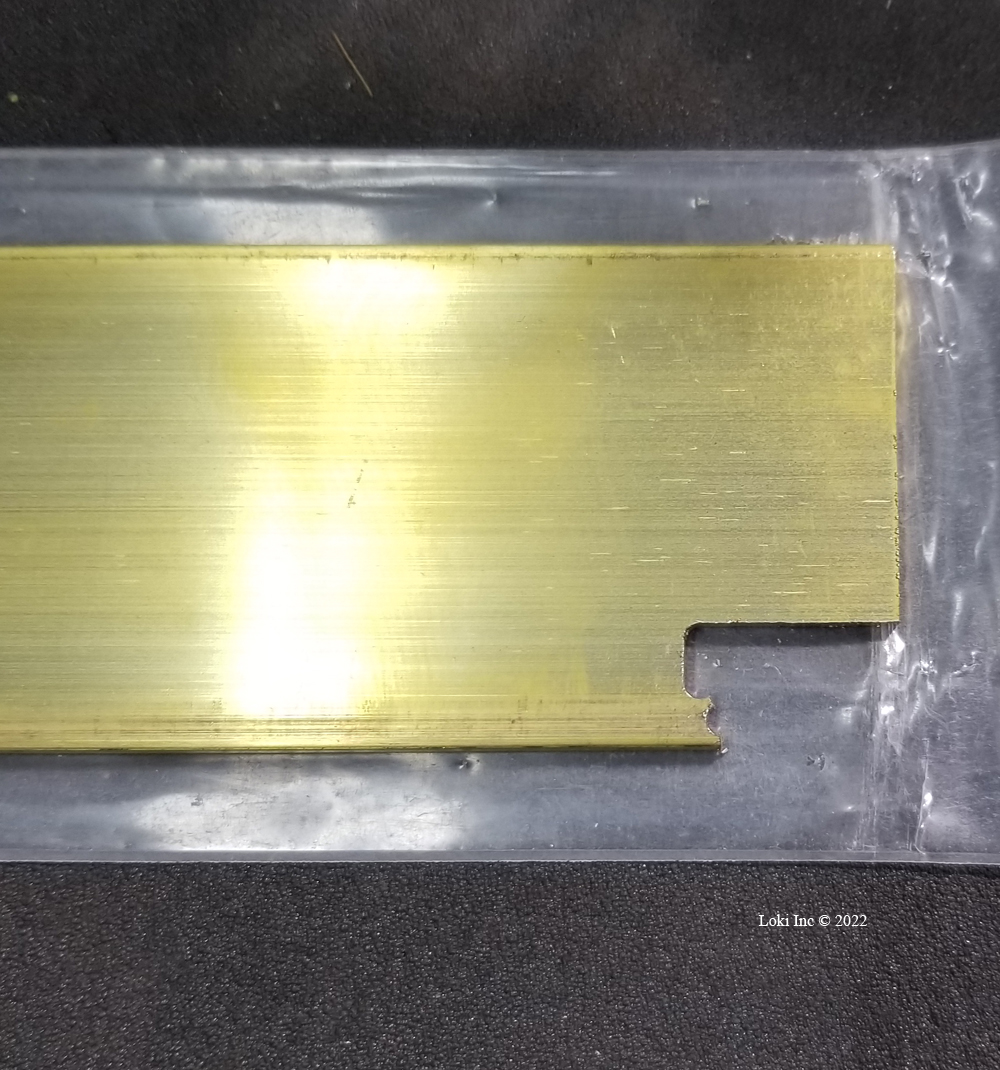
Scrap brass after sight blade cut out
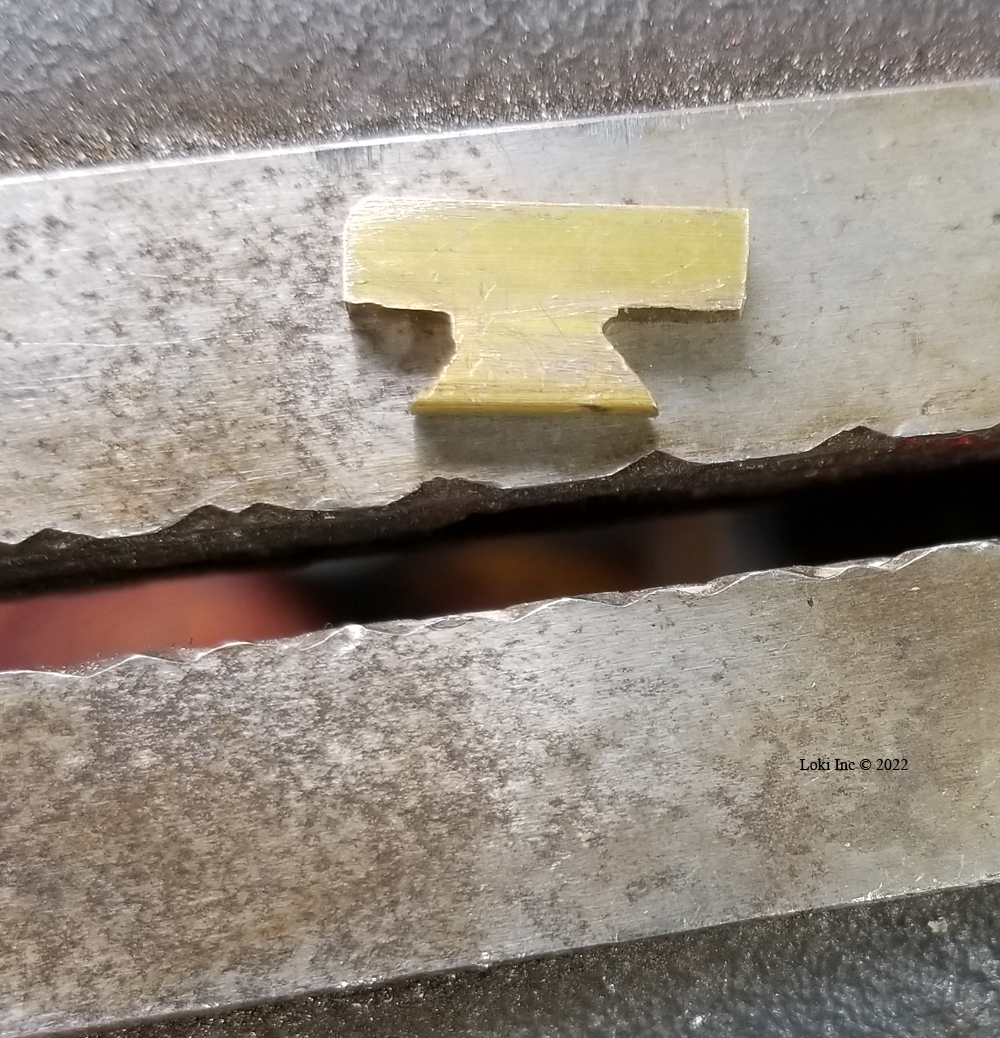
New front sight blade rough cut
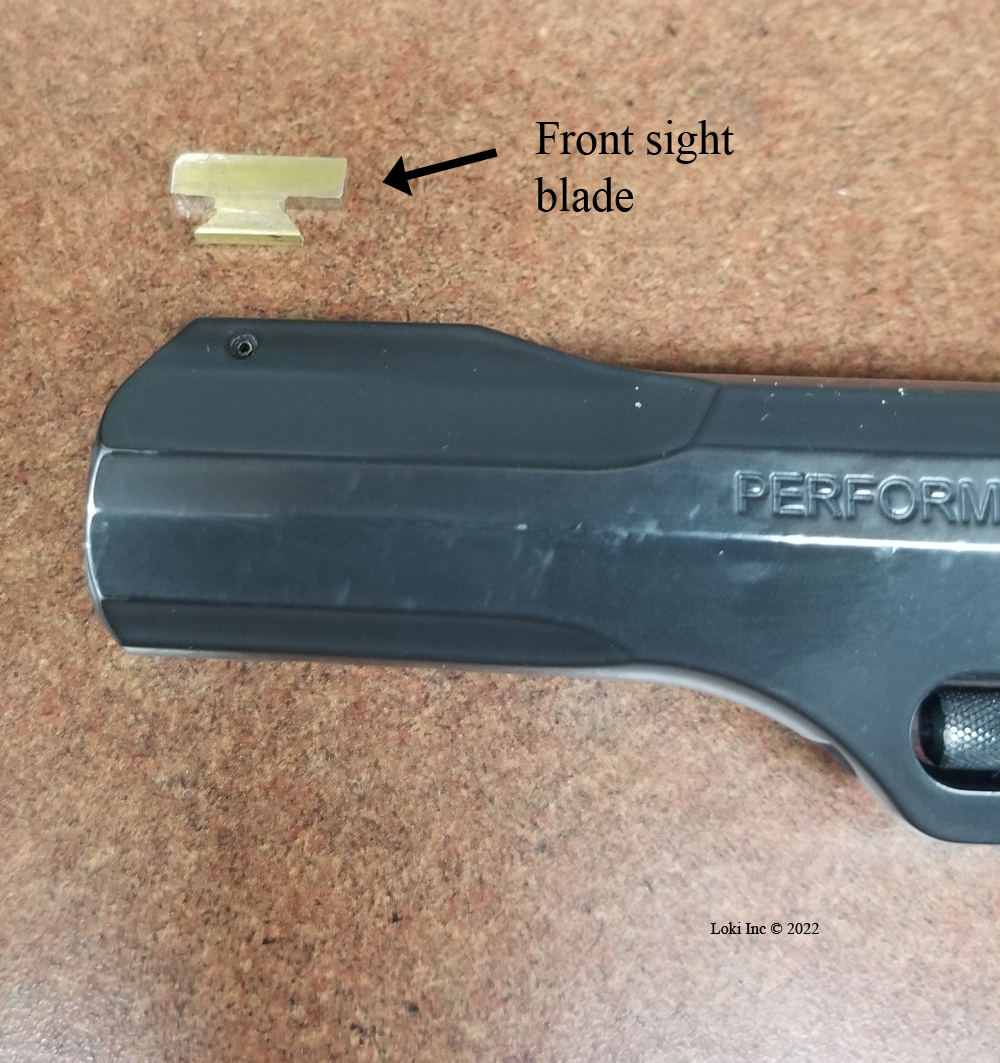
Front sight blade shape
I wanted the new sight blade to have an interference fit within the revolver’s front sight mount in the barrel shroud, but the blade was a bit thinner than I liked and rocked back-and-forth when I inserted it into the mount. So, I used a center punch to peen both sides of the blade that would be buried in the mount, until the blade had a press-fit and wouldn’t wobble back and forth.
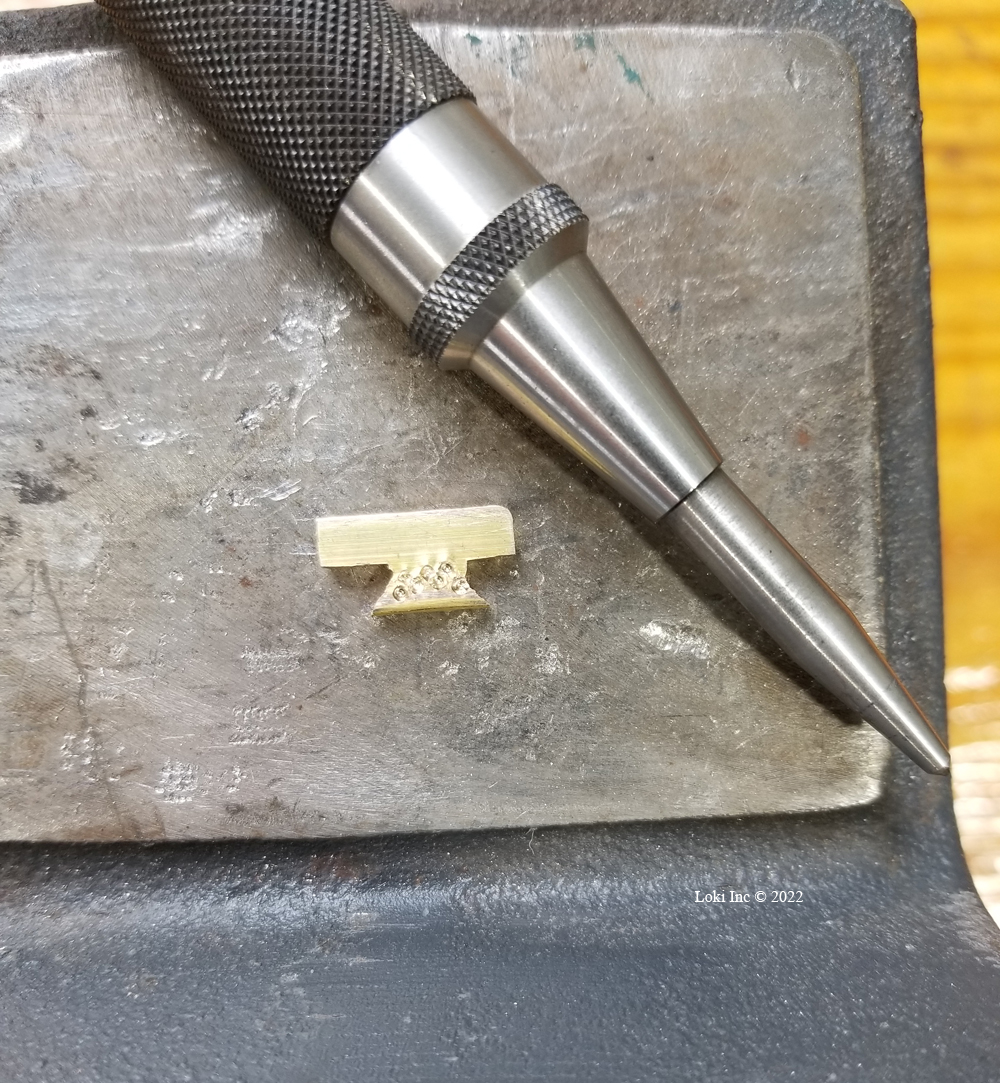
New front sight blade after peening
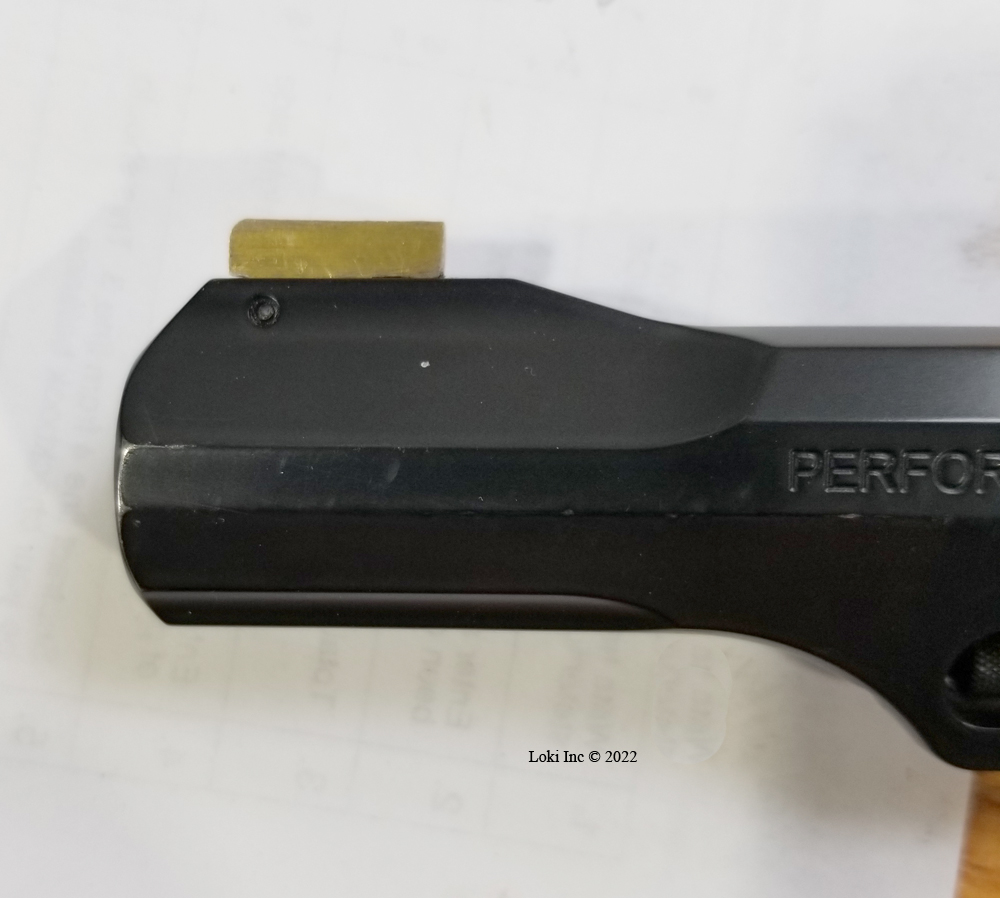
Front sight blade fitted to barrel shroud
At that point, I decided to put a small roll pin in the rear portion of the sight, inserted through the sight mount. After choosing a roll pin that would be about the same size as the factory pin in the front portion of the sight mount, with my new front sight in the mount, I used a center drill in my mini-mill and started the pin hole.
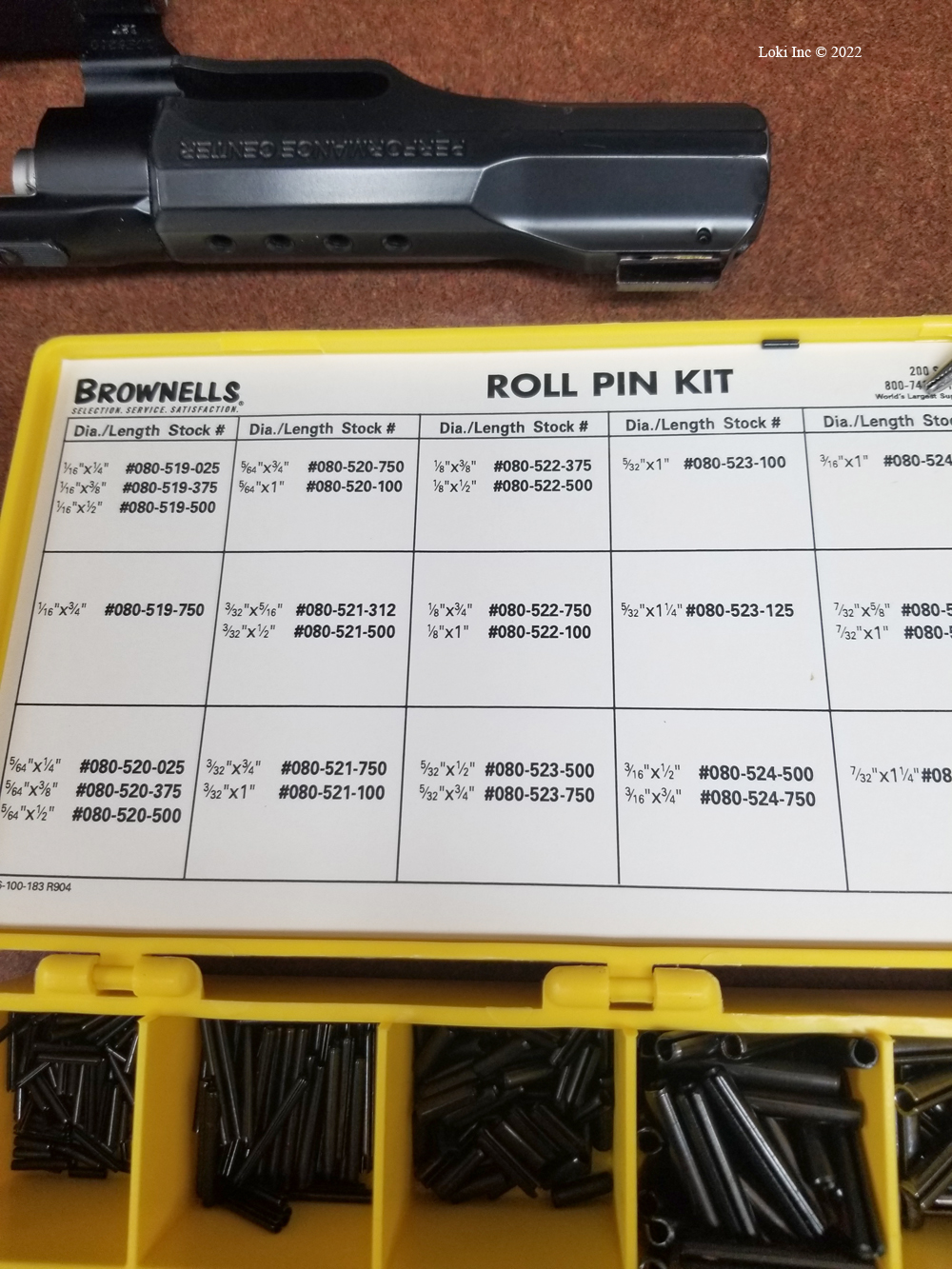
Roll pin kit
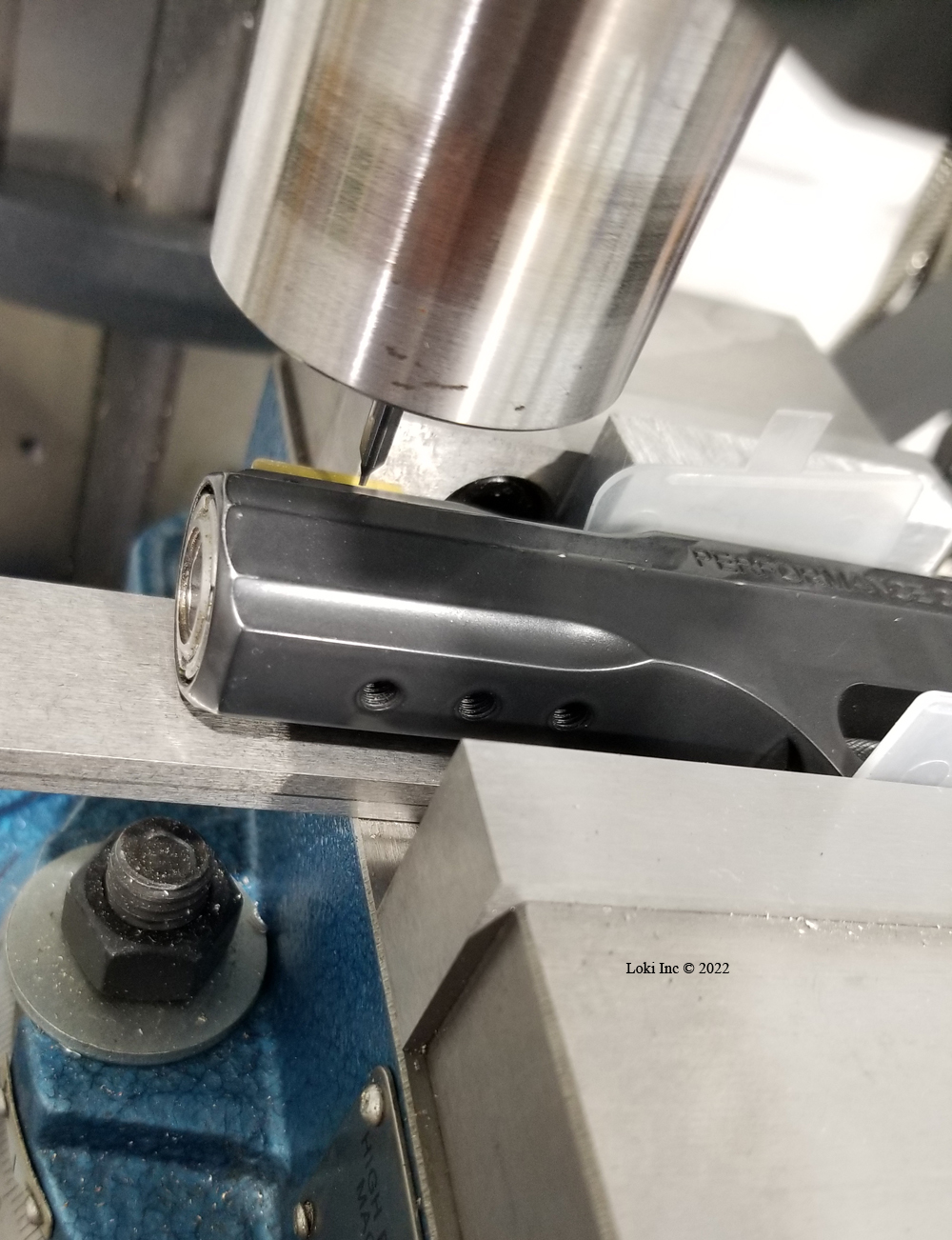
Preparing to center drill hole in front sight mount for retaining pin
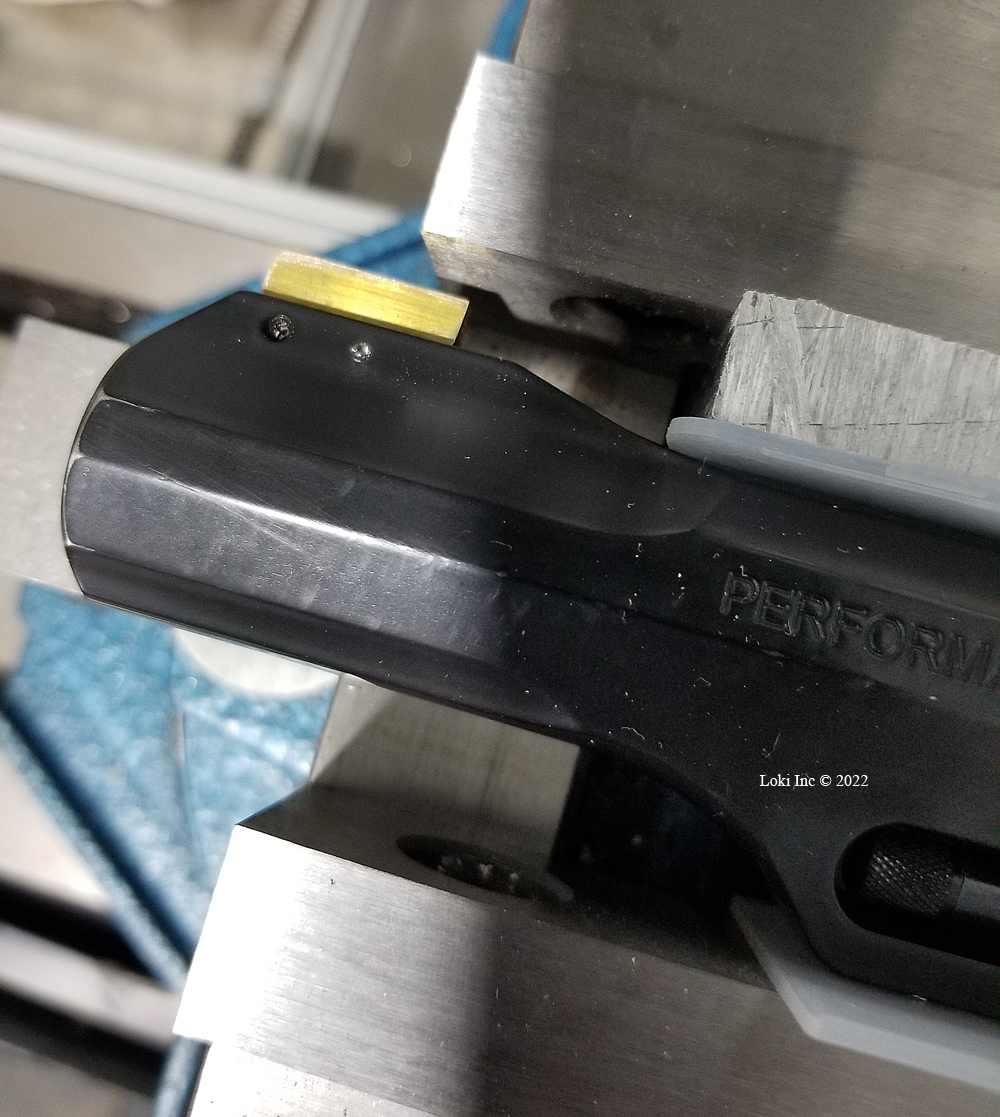
Front sight mount center drilled for retaining pin
Then, using the correct sized twist drill for the roll pin, I drilled the hole all the way through the sight mount and sight, and deburred the hole edges. I used the calipers to measure the correct length for the roll pin, from one side of the mount to the other at the hole openings, and then used a small cutoff wheel in a Dremel rotary cutting tool to cut the pin to that length.
After that, it was simple to insert the roll pin into the hole and tap it into place with a small roll pin punch.
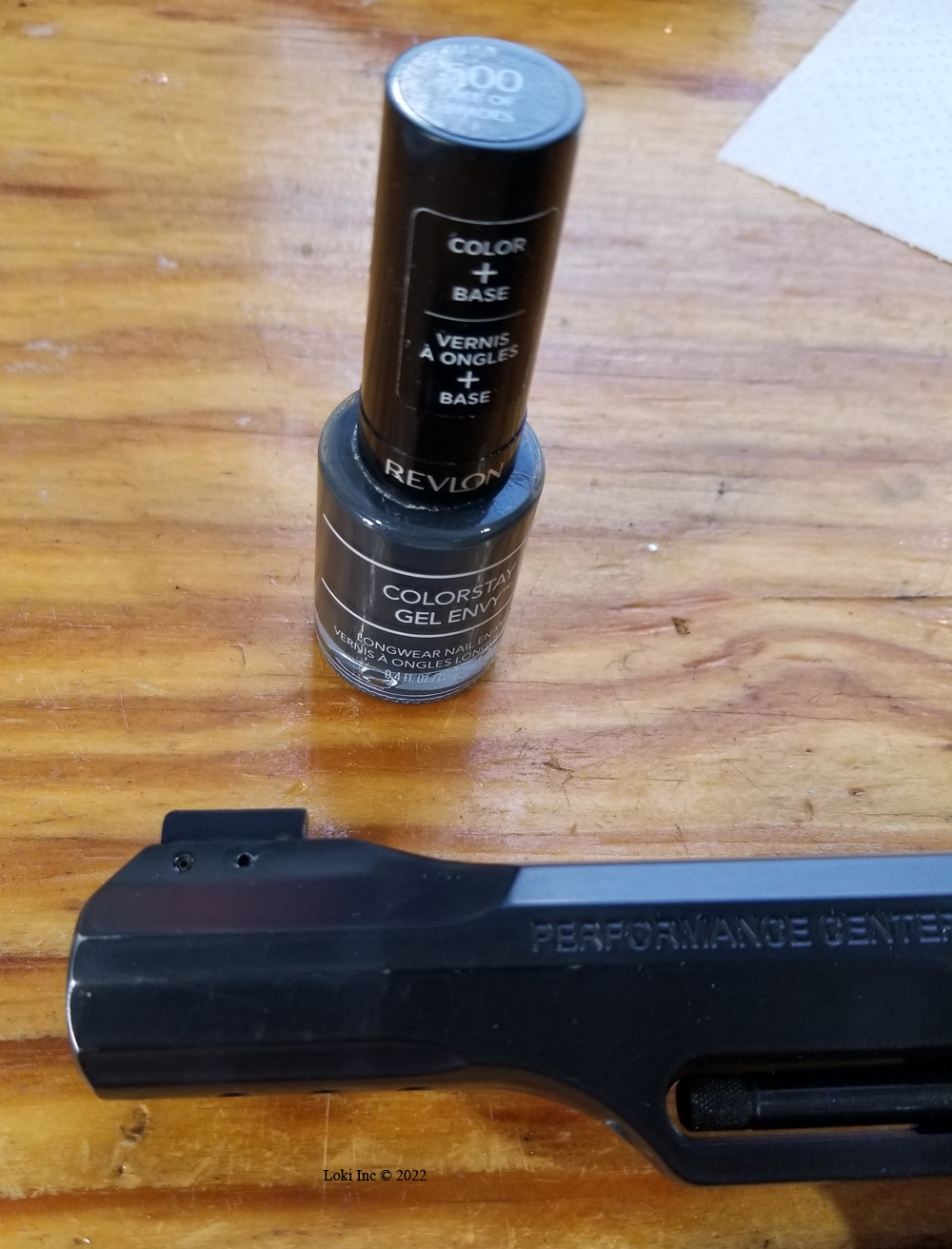
New front sight blade after black nail polish application
A little bit of my wife’s surplus black nail polish worked to cover the edges of the roll pin hole where the bare aluminum of the mount showed, as well as to paint the new front sight. I keep the nail polish bottle handy in case I need to touch-up the sight when it wears from drawing and holstering the gun.
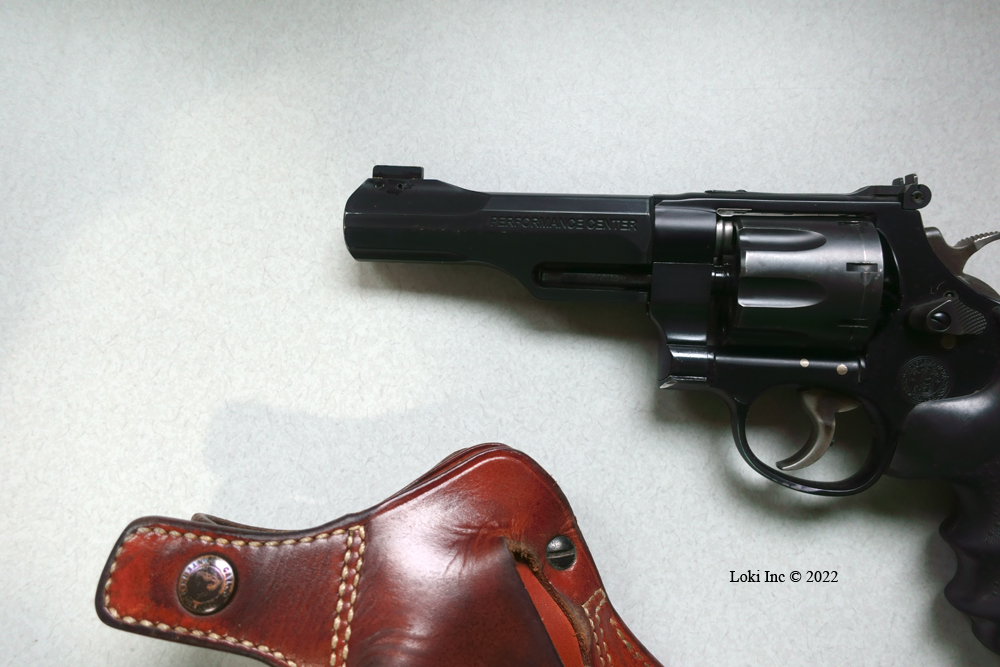
Finished product new TRR8 front sight
Since I completed the project, I’ve used the gun quite a bit and am very happy with it and the sight has never loosened or come off the gun, to the chagrin of many armadillos.
How to Mount an Aimpoint Red Dot on a Henry .450 Bushmaster Rifle
As a sponsor member of our local National Wild Turkey Federation chapter, Loki Incorporated gets a chance at winning a firearm at yearly fundraising banquets. At last year’s (2022) event, Loki won a Henry single-shot rifle in .450 Bushmaster caliber. This was a new caliber to me; I had heard of it as a cartridge for AR15-type Modern Sporting Rifles (MSRs), designed to fit within the magazine well size of those guns. I knew the creation of the cartridge had something to do with certain states’ restrictions against using bottlenecked cartridges for hunting large game. I hadn’t investigated it further, because I’m fortunate to live in a state with no such bullshit restrictions.
So, my investigation of the .450 Bushmaster caliber started serendipitously with winning a rifle chambered in it. It turns-out the .450 is nearly the ballistic equivalent of the legendary .45-70 in modern loadings, with all other factors (barrel length and bullet weight, mainly) being equal. The .450 was initially loaded by Hornady, adapting previous attempts to create a large diameter “Thumper” (the late Col. Jeff Cooper’s term) cartridge pushing a heavy bullet capable of whacking enemies or big game at relatively close range from a compact firearm. The concept is sorta like a .45-70, but the round works in an MSR. Hornady’s adaptation was successful, and now several different arms manufacturers sell not only MSRs, but conventional guns too, in .450 Bushmaster.
The .450 has a rebated-rim “straight-walled” case; it’s actually slightly tapered, enough to make feeding into the gun’s chamber easier than for a truly straight-walled case. The case has no distinct neck, though, making it acceptable to the drones who came up with the bottlenecked cartridge restrictions and demonstrating their ignorance of the terminal performance of small arms.
Why would I mess with a close-range, single-shot rifle in a “Thumper” caliber when I live and typically hunt in a state that has no bottleneck cartridge restrictions? Well, my deer hunting can be over open fields where high velocity .30 caliber arms excel or in hilly and thick cover where a short, handy gun capable of thumping a deer (or opponent) at face-to-face ranges would be useful. I thought it would be interesting to see if the Henry rifle would fit that role.
Henry .450 Bushmaster Rifle
The Henry .450 Bushmaster is only 37.5 inches long, but has a 22-inch barrel. The barrel isn’t threaded, so you cannot attach a muzzle device without gunsmithing. The gun is a lightweight, tipping the scales at about 6-¾ pounds, so it thumps at both ends when fired. Tiger-striped matte finished walnut furniture embellished with swivel studs complements the dark blued barrel and matte black receiver. The gun came with a brass bead front sight and a folding leaf rear adjustable sight, and was drilled and tapped for a Weaver 82 scope mount.
If my old eyes could accommodate the iron sights, I would have left the gun alone because I wanted to use it at short ranges for quick shots. But, that feat is getting more difficult for me each year, so I decided to mount a red dot sight on the rifle. I wanted a sight that was robust and wouldn’t easily hang-up on brush, and would allow me to quickly aim at my target with both eyes open. My choice was the Aimpoint Micro H-2 with a 2 MOA dot. This sight mounts to a “Picatinny” rail, and my measurements of my eye high above the rifle bore indicated the combination of sight and rail would center the red dot in my line-of-sight when I shouldered the rifle. Perfect! Now to mount the sight.
How to Mount an Aimpoint Red Dot Sight
I did a search online for a Weaver 82 compatible rail, as Henry didn’t offer any to fit the H015 rifle series my rifle belonged to, and immediately found several sites that sell them. The only problem was that no one sold a shortie version – the rear sight on my rifle is so close to the scope mount holes above the chamber that I would have to remove the sight to install a standard length base.
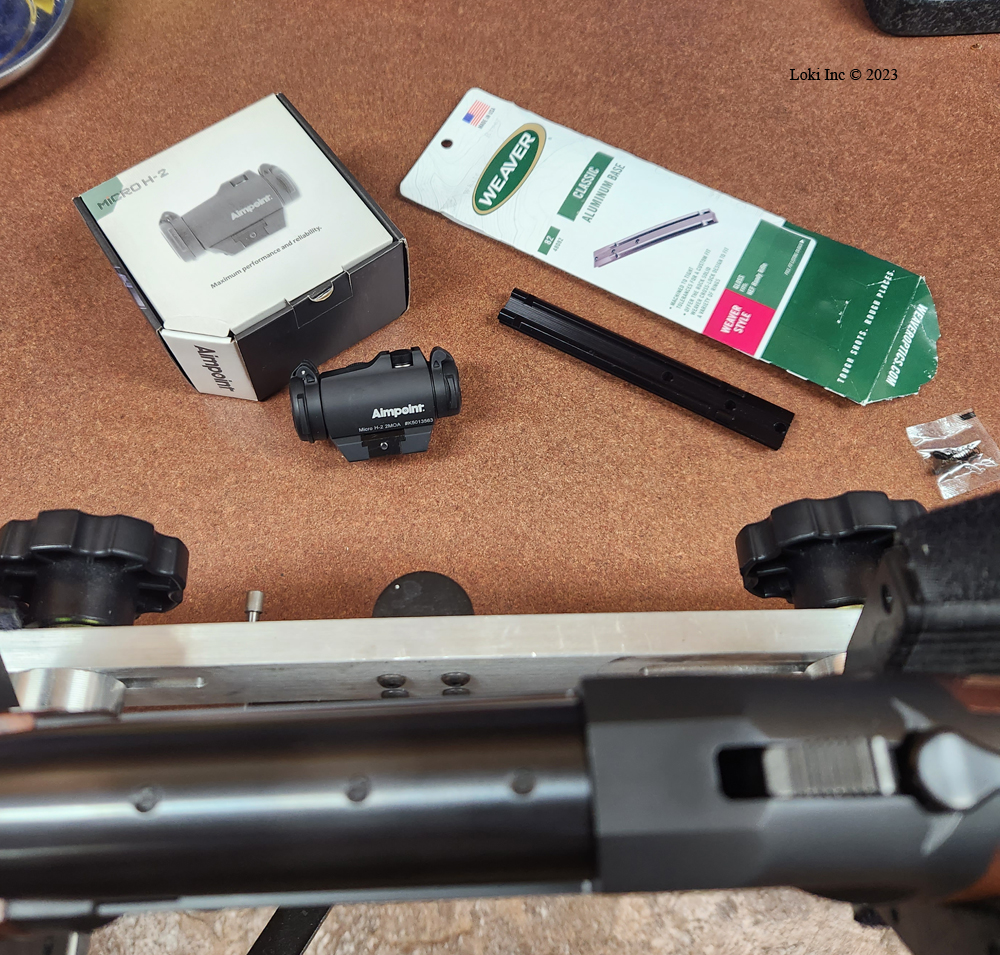
View of Rifle, Micro H-2 and Base
Also, as you can see from the photo even if I removed the rear sight or machined the rail to fit over the sight, the short chamber contour of the rifle would have require cantilevering the rail over most of its length. Bad Juju.
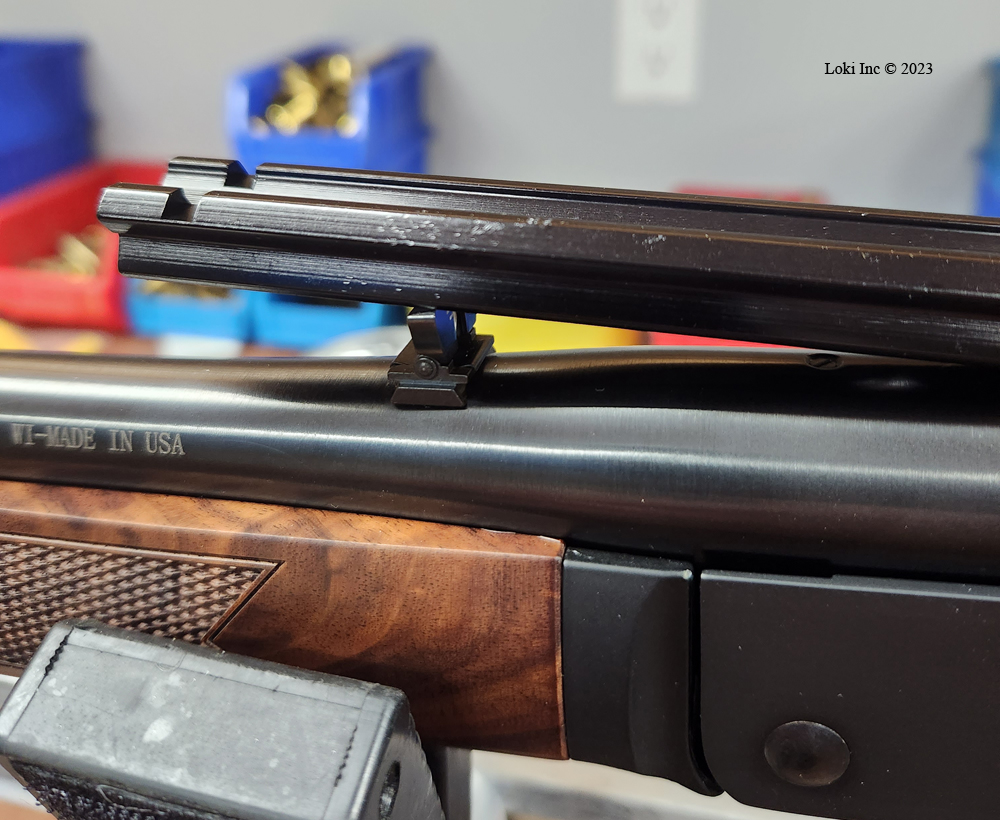
Rear Sight and Base
So, I mounted my optic on the rail and then checked how long the rail would have to be to include all three mounting screw holes and be well short of interfering with the gun’s rear sight.
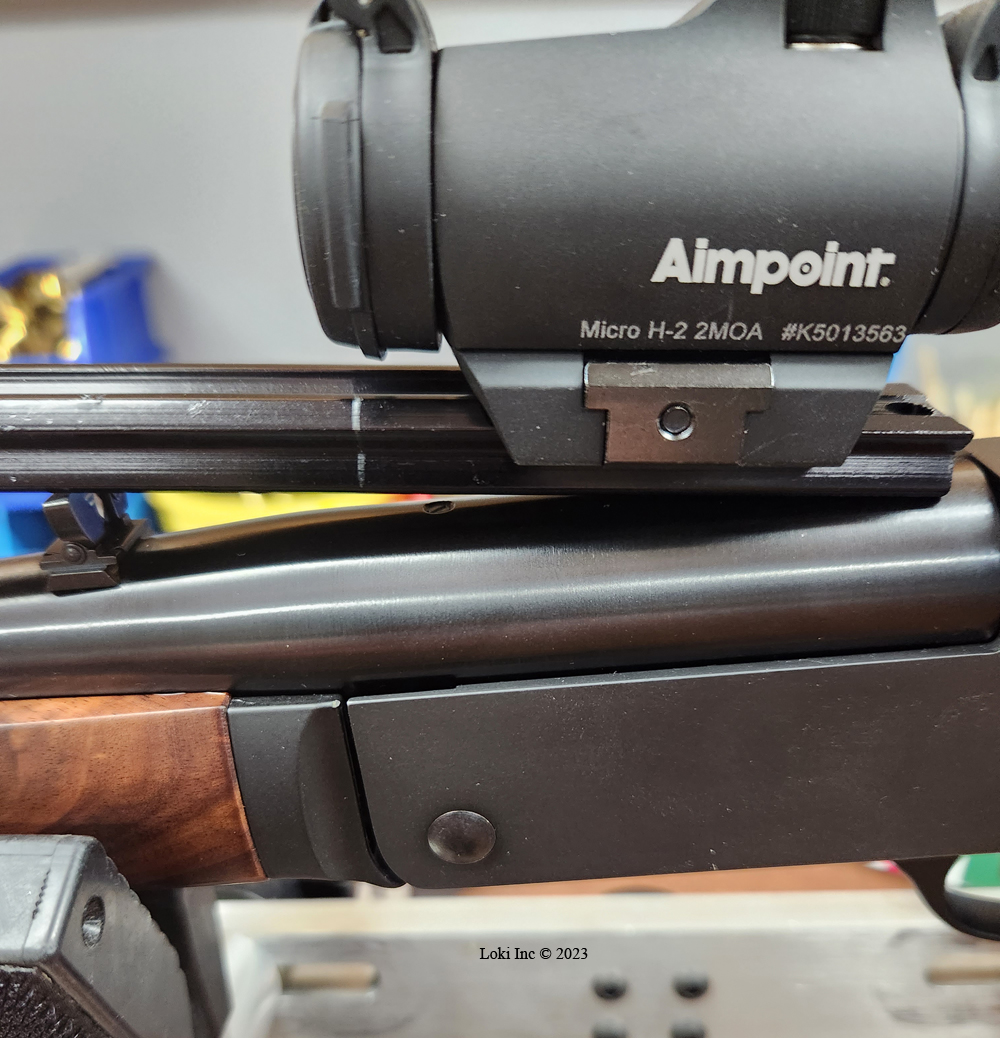
Checking Rail Length
Once I determined and marked on the rail the length I wanted, I clamped it in my horizontal bandsaw and cut it off.
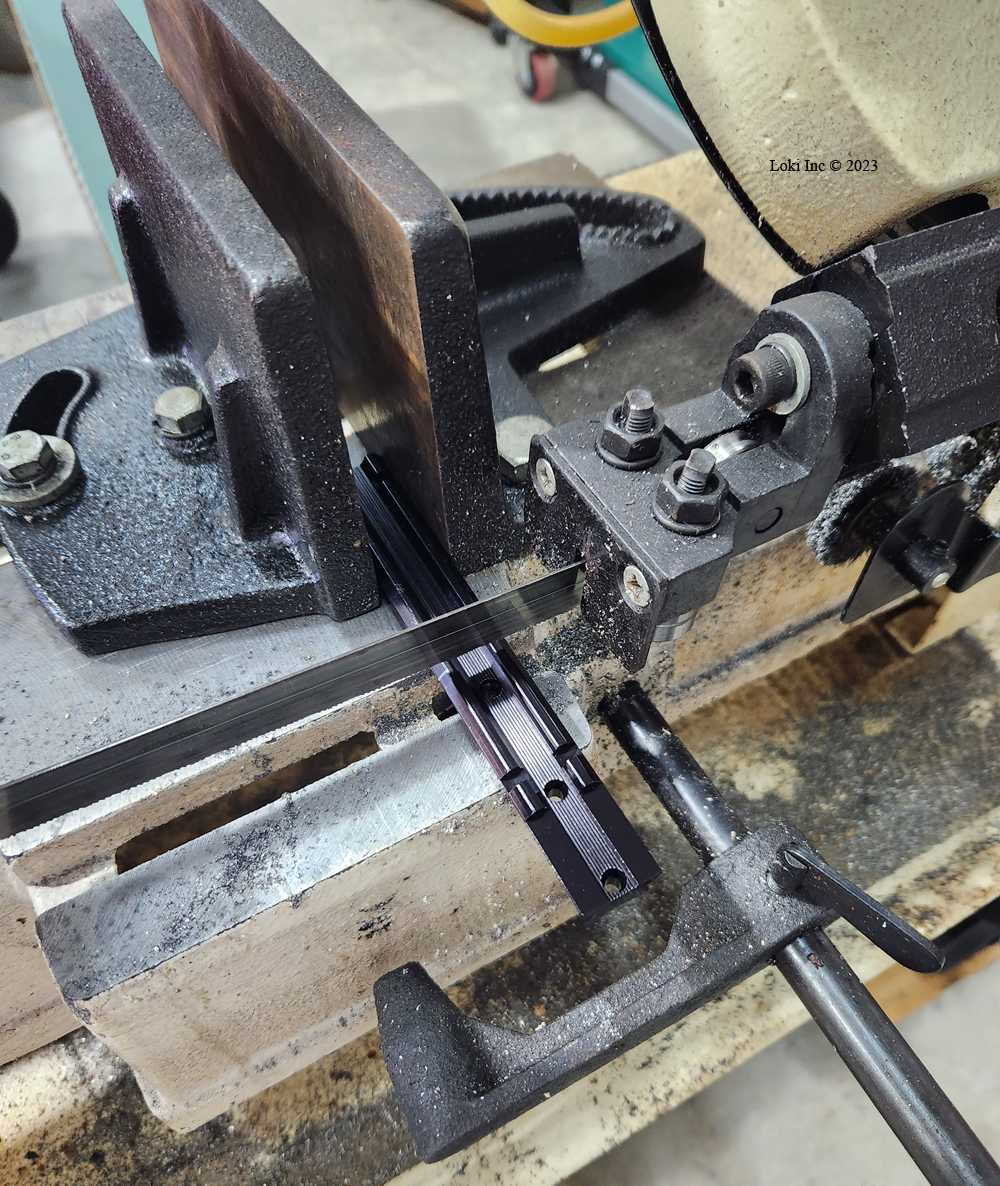
Cutting the Rail
Then, using some scrap cardboard in my machinist’s vise, I clamped the piece I intended to install on the rifle in the vise and smoothed the cut edges with files.
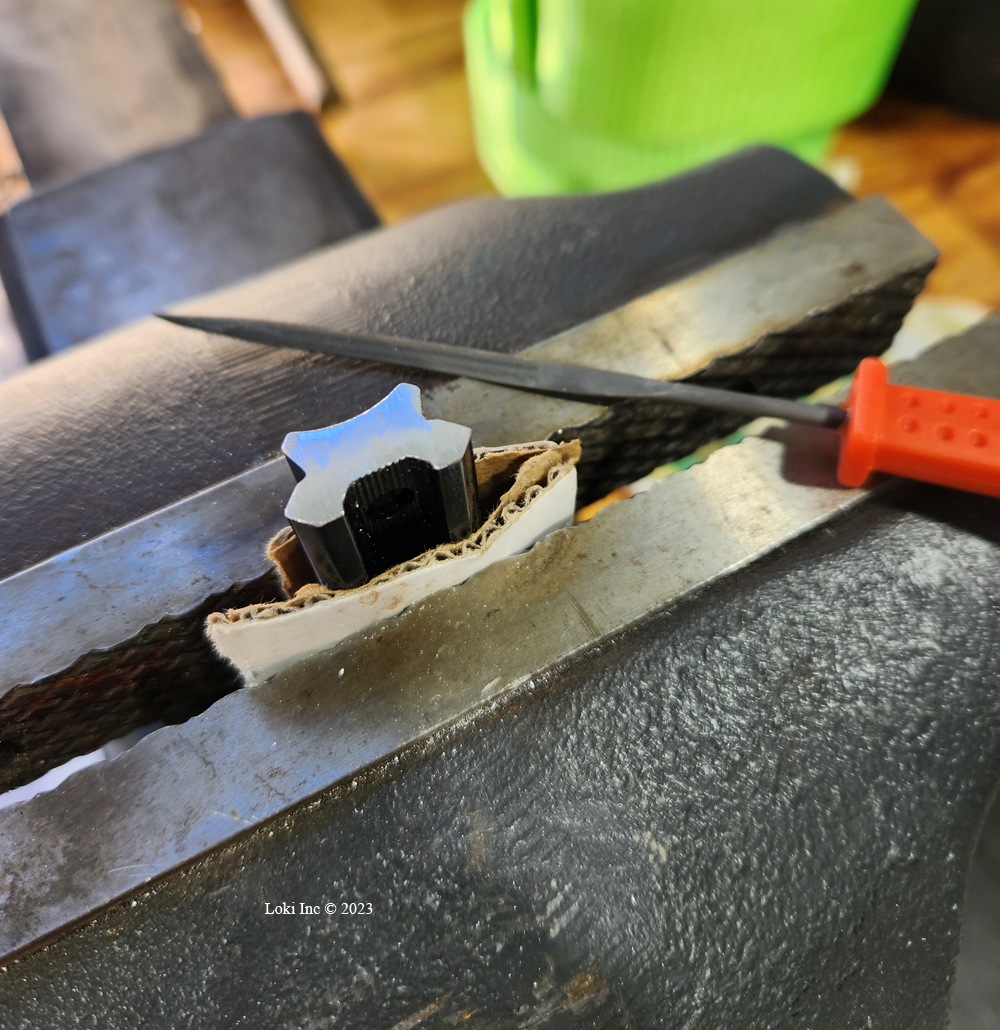
Filing the Rail
After cleaning the filed end of the rail, I used some aluminum blackening finish to “paint” the cut end of the rail.
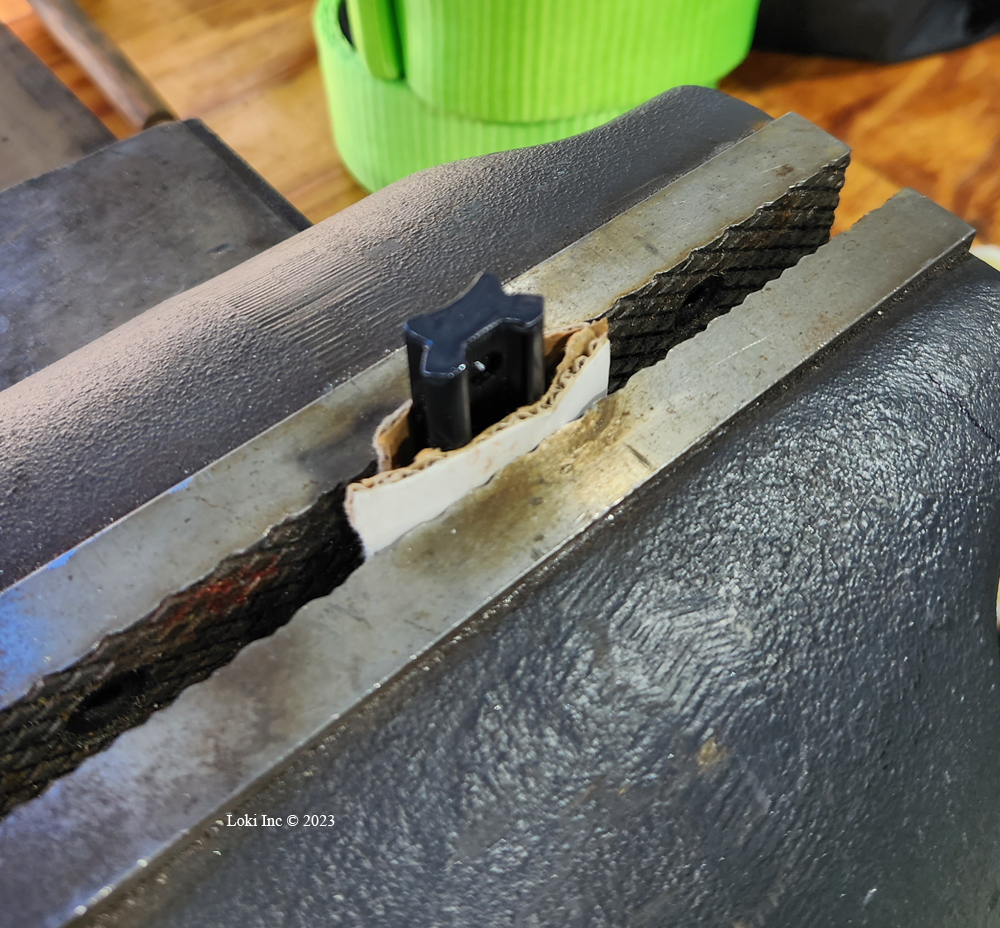
Blackening the Rail
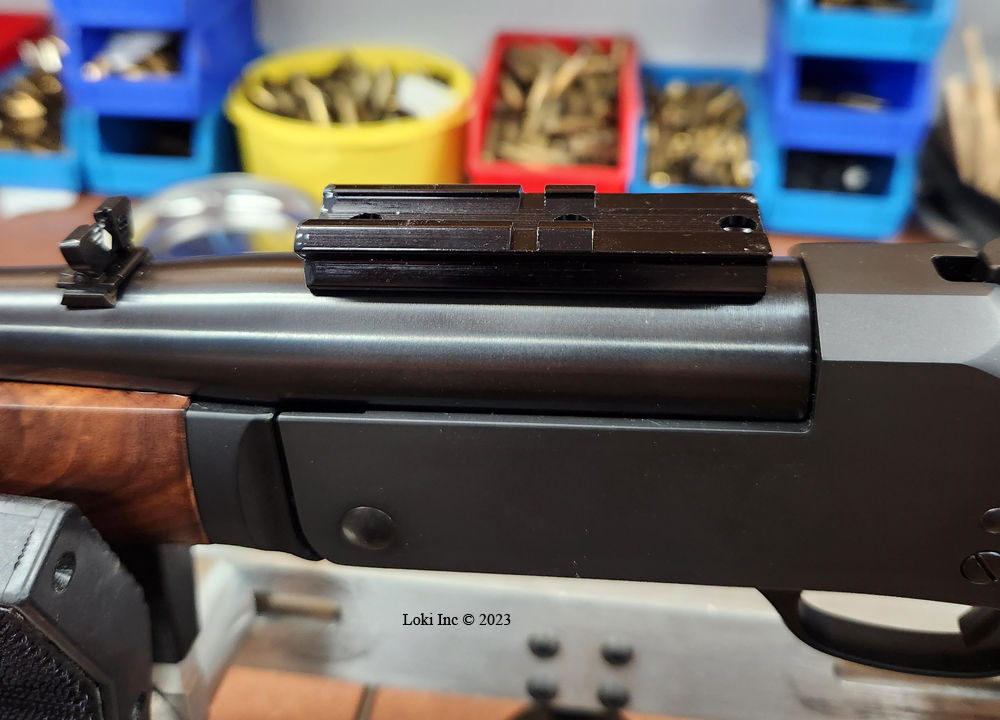
Fit Check
After a fit check to ensure the mount interfaced properly with the rifle and the mounting holes in the rail aligned with the ones in the gun, I degreased the scope mount holes on the rifle with carburetor cleaner.
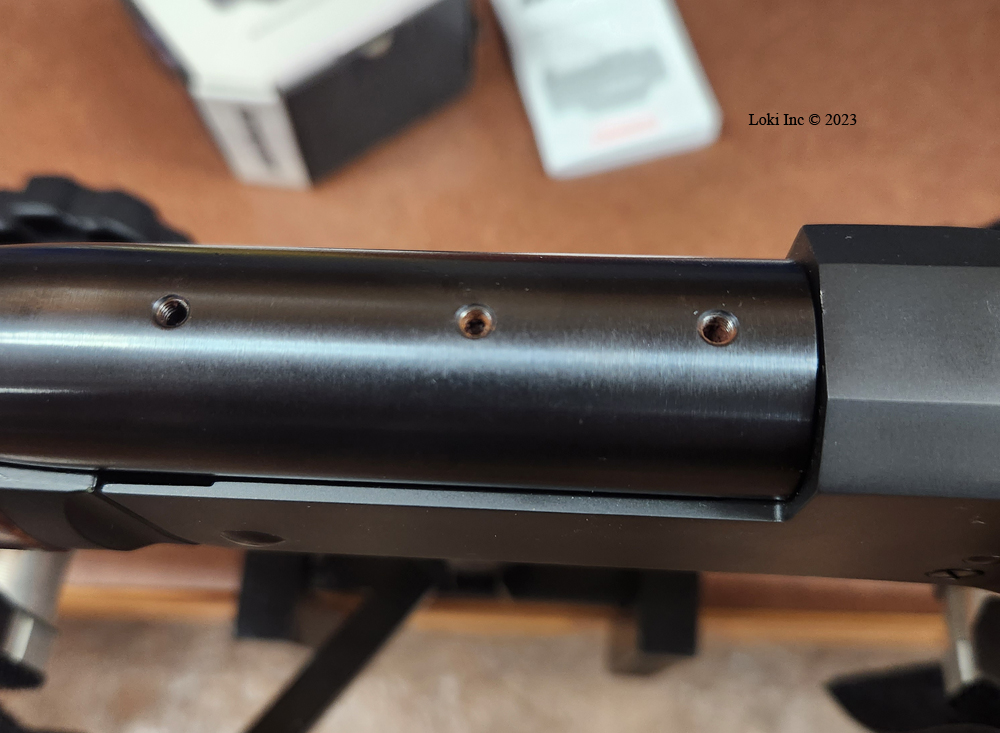
Scope Mount Holes
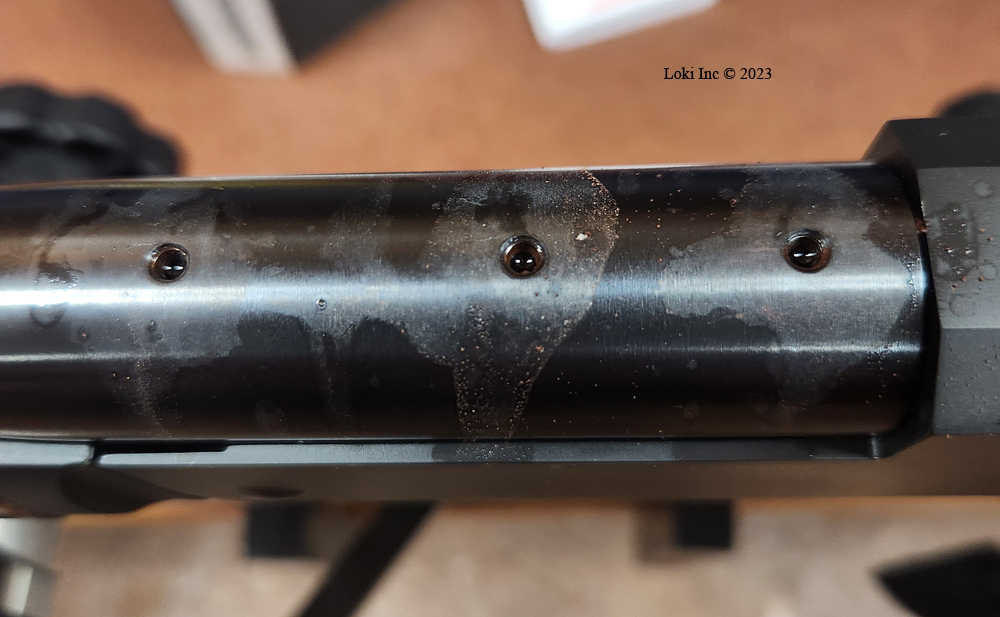
Mounting Holes Degreased
If you use a solvent that produces hazardous vapors to degrease the holes, be sure to work in a well-ventilated and flame/spark-free environment. Also, if your solvent is in a spray can be sure to wear safety glasses to defend your eyes from spray kick-back, and use an apron to protect your clothing when you are spraying the stuff. After letting it work for a few seconds, use a cotton swab to soak up any degreaser that may have settled into the mounting holes.
Since the mounting screws that came with the rail had slotted heads, instead of hex or torx heads made for higher torque attachment, I used blue thread sealant in the mounting holes to secure the mounting screws.
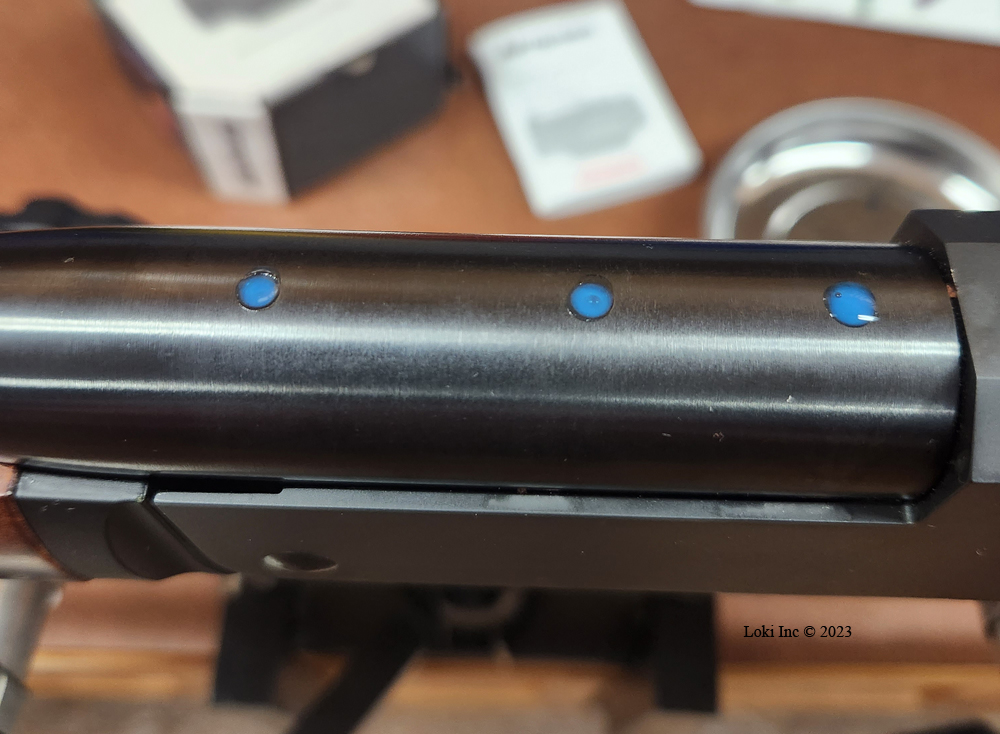
Thread Sealant in Mounting Holes
Then, before the sealant could set-up, using a small torque wrench set to the rail manufacturer’s recommended level I installed the mounting screws through the rail into the mounting holes in the rifle.
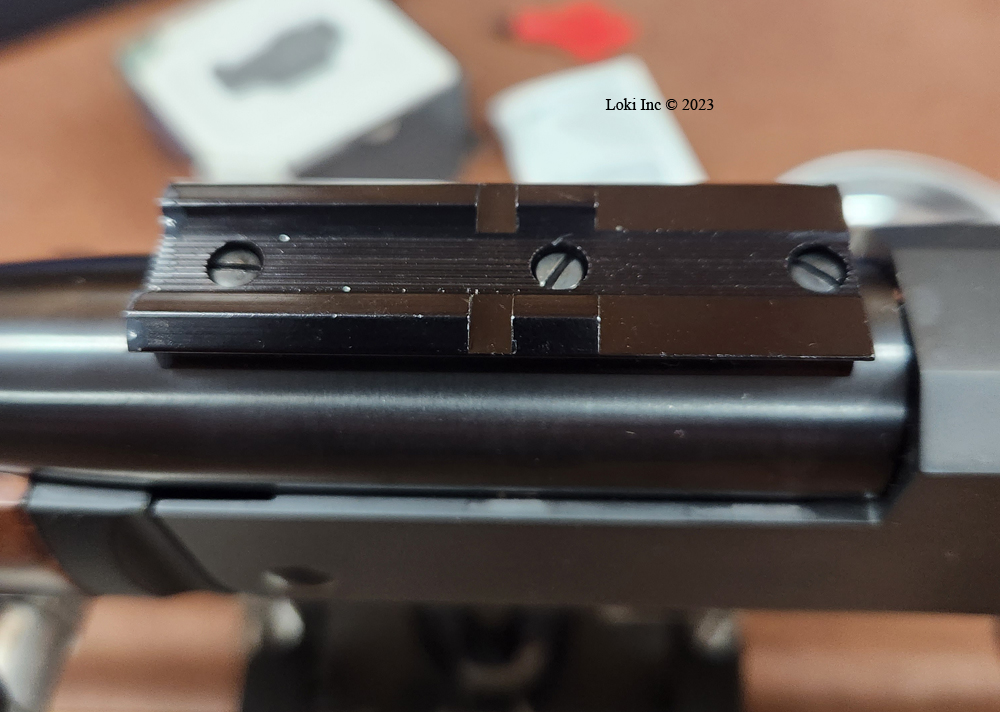
Rail Attached
All that was left to do in the sight mounting process was to attach the Micro H-2 to the rail, using my small torque wrench to turn the sight mounting screw to the manufacturer’s recommended level.
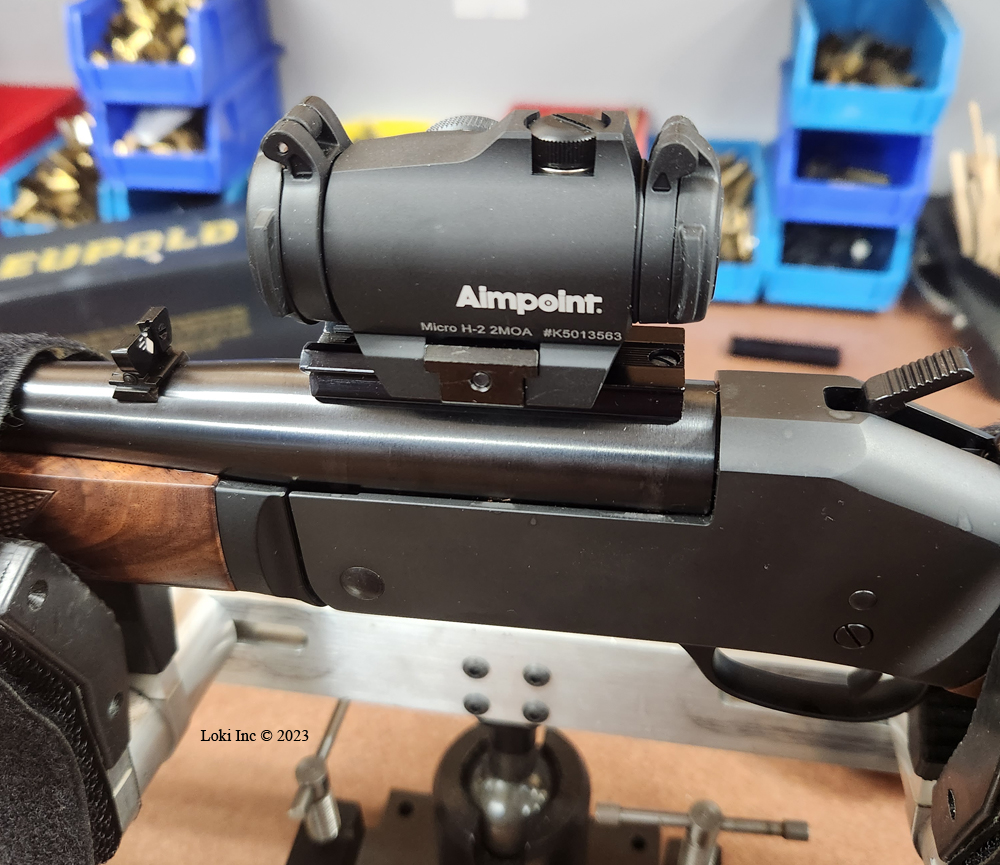
H-2 Mounted on the Rifle
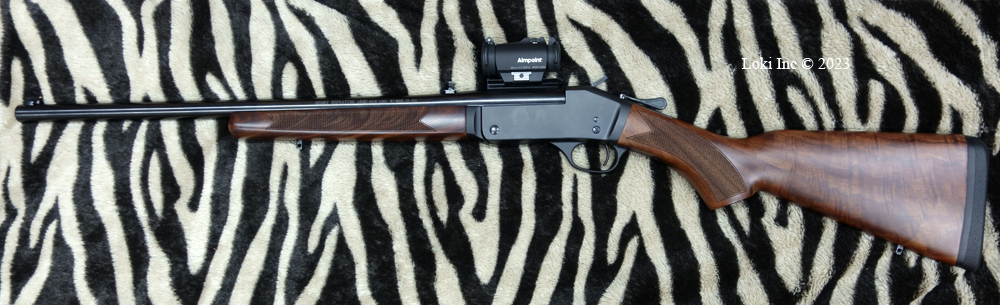
Henry .450 Bushmaster Rifle with Aimpoint Micro H-2
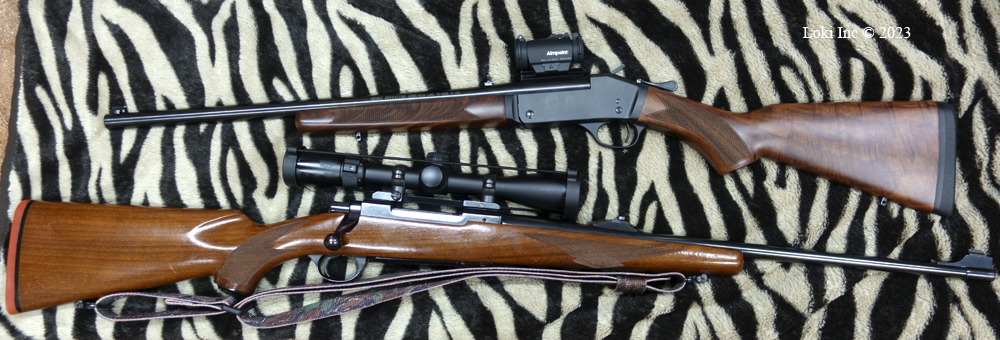
Henry and Ruger Rifles
For comparison purposes, I took a photo of the Henry rifle alongside my favorite deer rifle, a Ruger M77 Mk1, and a photo of their respective fodders.
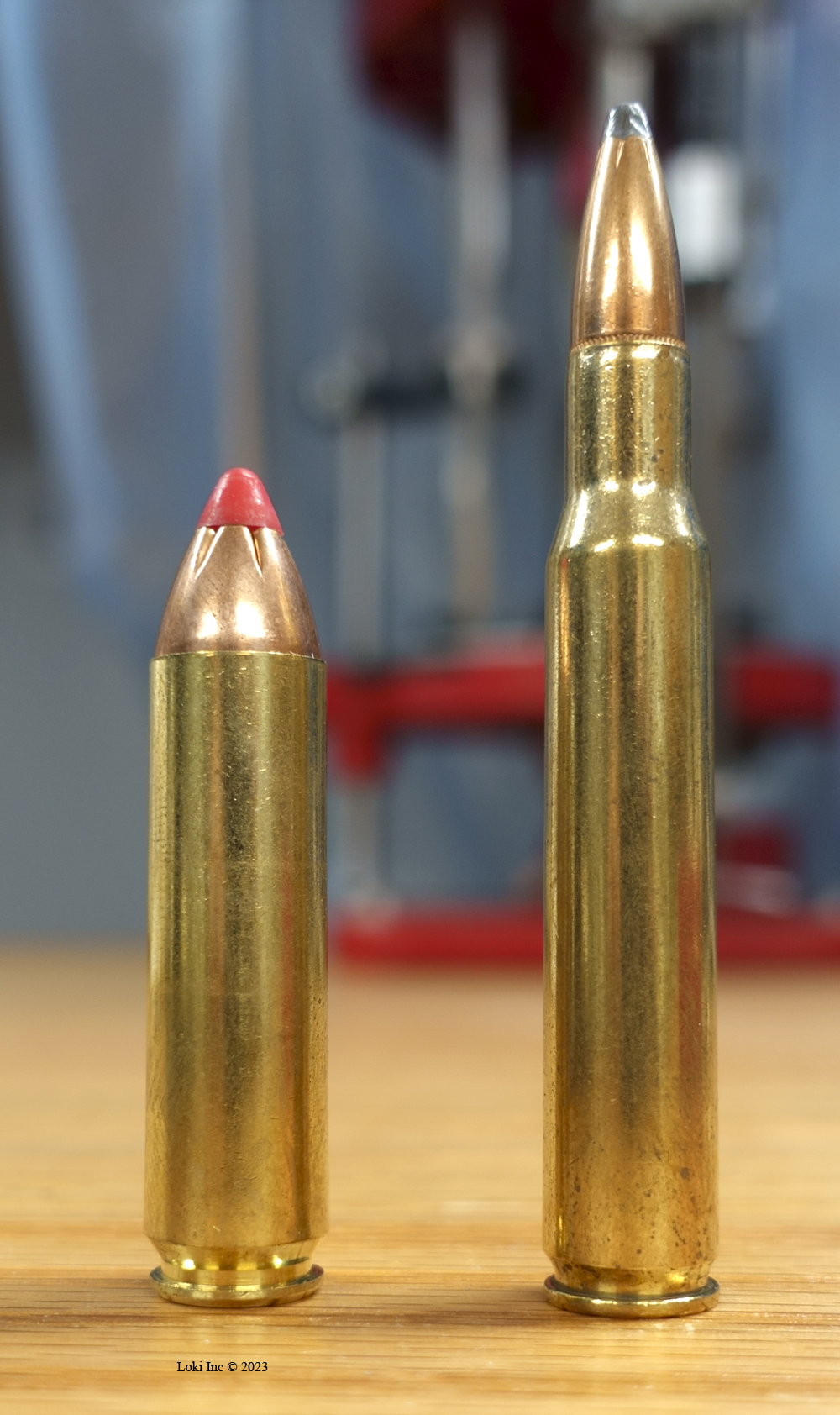
.450 Bushmaster on Left, .30-’06 on Right
The Ruger is longer and heavier than the Henry, and the .30 caliber cartridge is longer than the .450. Notice the latter bullet has a larger diameter, and it is heavier by 100 grains (250 vs 150). The .30 caliber bullet leaves the gun muzzle at over 700 feet per second faster than the .450 and has about 250 foot-pounds greater kinetic energy because of its higher velocity (recall that Ek = 1/2 mV2, so energy increases faster with increasing velocity than it does with increasing mass). Even so, the shape of the Henry’s stock, and its lighter weight combined with shorter length, causes the muzzle to rise more when I shoot it offhand than the rise of the .30-’06.
Now, the fun began! I got ready to take the rifle out to the range to test it, with the only commercial ammo I could find at the time, Hornady Custom with 250-grain FTX bullets. As part of my range preparation, I looked at the particulars of this round. On the cartridge’s web page under Specifications, you’ll be able to compare each of the .450 Bushmaster cartridges that Hornady loads, and also view the data for each cartridge in Hornady’s Ballistic Calculator. I reproduced the results for the 250-grain FTX load, below.
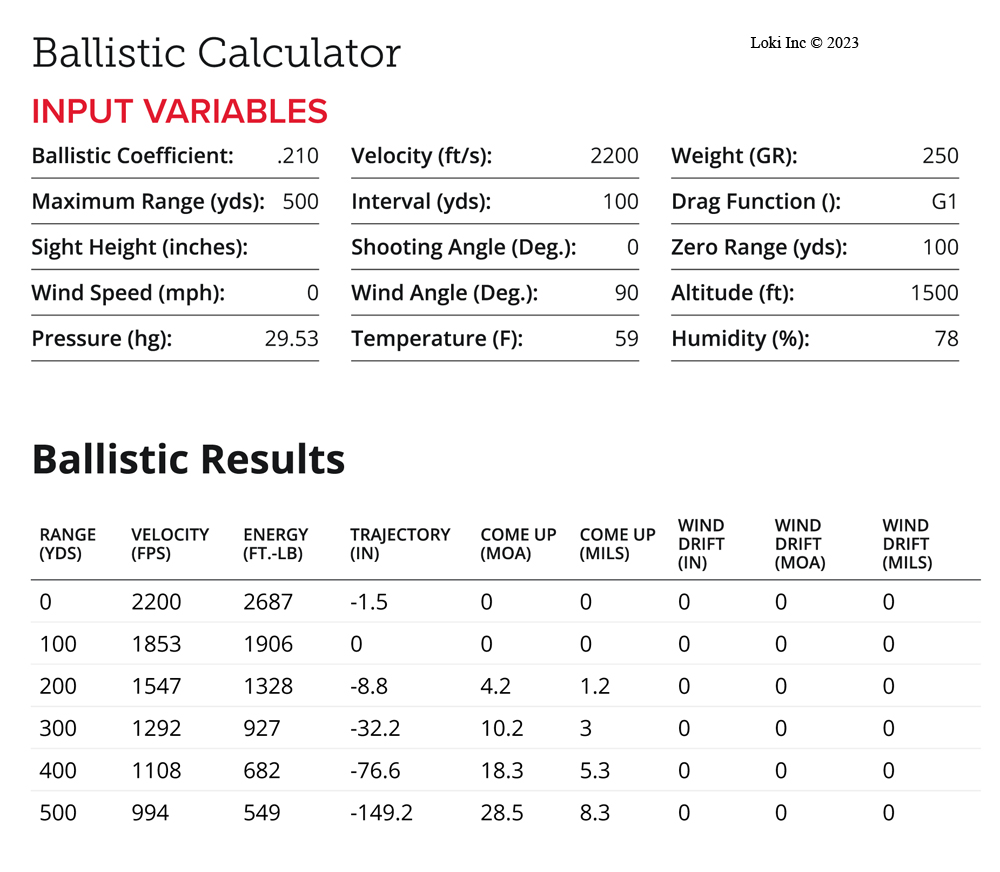
Ballistic Calculator for .450 Bushmaster
Looking at the results, I see the big slug slowing down rapidly, becoming subsonic somewhere between 300 and 400 yards downrange. Given a 100 yard zero, the bullet stays within a point-blank range (a dinner plate sized impact zone) from the gun’s muzzle out to nearly 200 yards, where it drops almost nine inches and loses nearly half of its kinetic energy. That tells me that if I do my part, I can make killing shots on deer-sized targets to nearly 200 yards by merely holding the red dot on my desired impact point when I fire the rifle. Given my intended use of the gun, that is more than enough range.
At the range, the rifle and cartridge combo truly is a thumper! The felt recoil is on a par with a 12-gauge turkey shotgun firing 3-inch magnum shells.
Reworking a Savage Axis 6.5 Creedmoor Rifle
My original rifle for this project was a new Savage Axis rifle in 6.5 Creedmoor caliber that I won at a benefit banquet. I anticipated enjoying hours of shooting this new rifle, but quickly learned that it needed to have its rifle barrel reworked.
As per my usual process with a new rifle, I mounted a good scope on it, cleaned it, bore-sighted it, and shot it. I wasn’t happy with the groups I was getting, using two different loads from Hornady (140 grain ELD Match, and 147 grain ELD Match) and one handload with four different powder weights (140 grain ELD bullets, H4350 powder @ 38.1, 39.0, 40.0, and 40.9 grains). There wasn’t much difference among the group sizes of any of the loads; the groups were twice as big as those fired from my S&W M&P 10 in 6.5 Creedmoor, and I knew a good bolt-action rifle should be able to shoot at least as well as an AR-type rifle.
I was not happy about the so-so group sizes, and after examining everything else I could think of as causative factors (action bedding, scope ring and mounting screw torques, etc.) I used my borescope to see if the problem was in the bore. The bore looked OK until I examined the last two inches or so of it at the muzzle of the barrel. There was severe corrosion pitting of the entire last two inches of the bore reminiscent of the entire original bore of a 1913 Spanish Mauser barrel I used to have that had been fired in its early days using ammo with corrosive primers.
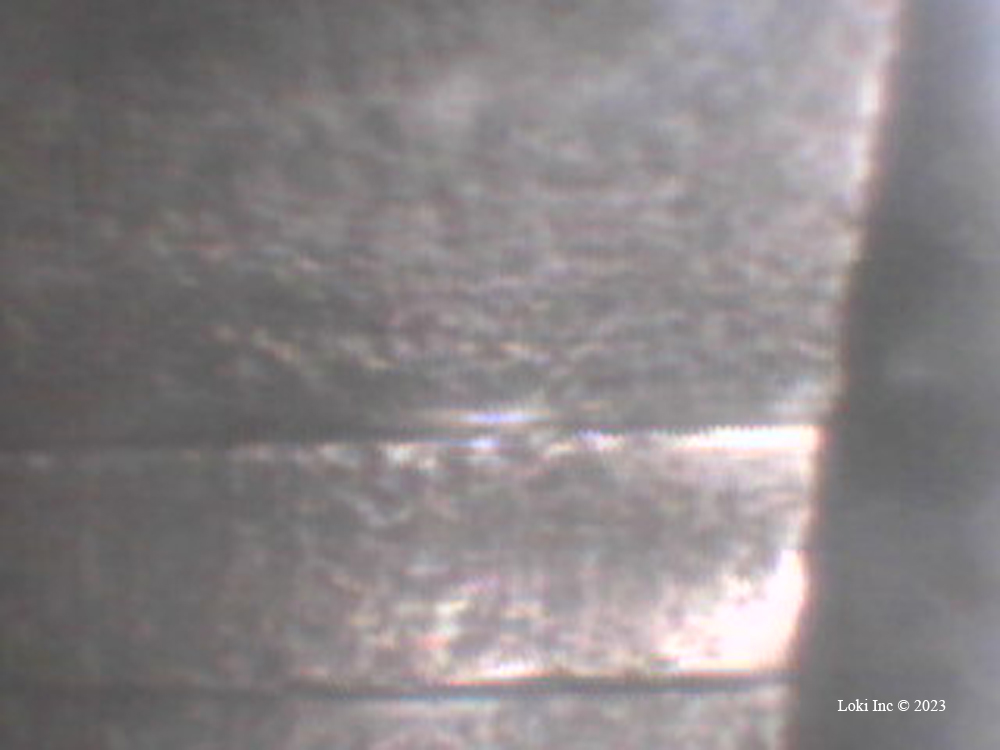
Corrosion damage to rifling 1
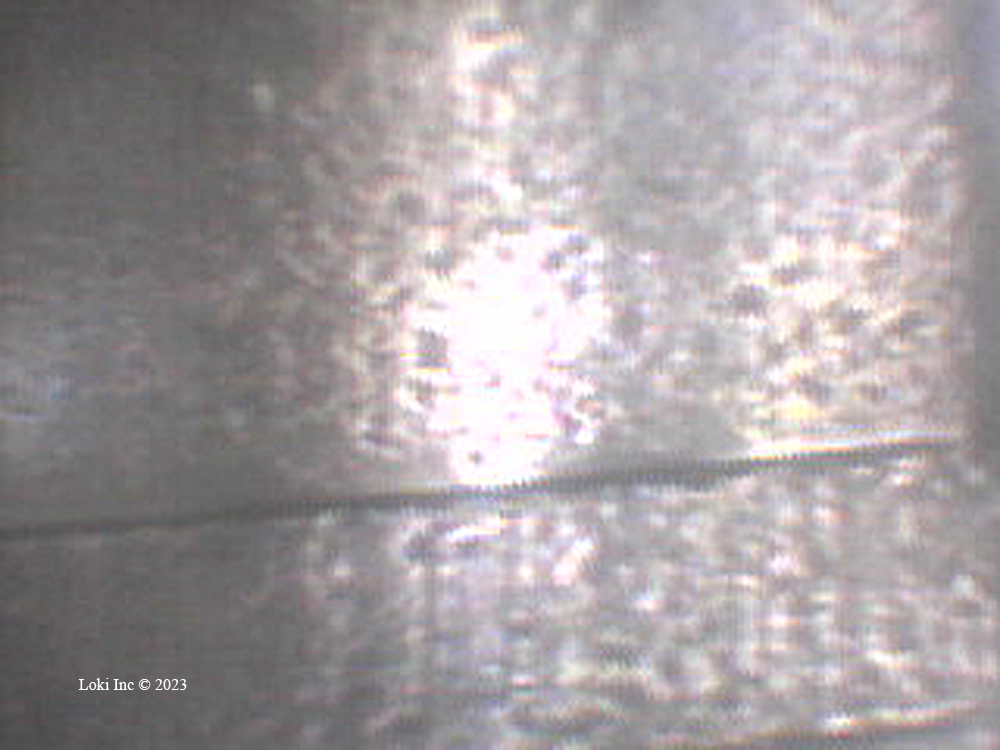
Corrosion damage to rifling 2
Reworking a Savage Axis 6.5 Creedmoor Rifle
Therefore, if I wanted to improve the group size, at the very least I would have to either cut-off the damaged part of the barrel and re-crown it, or re-barrel the gun. I decided to re-barrel the gun, rather than lose ammo velocity by shortening the barrel. At the same time, I decided to improve the trigger pull consistency and weight.
After searching around the Internet for replacement 6.5 Creedmoor barrels, I decided to buy a varmint (heavy) contour barrel from E. Arthur Brown Company. I already had a Savage barrel locknut wrench, but I needed headspace gauges to properly install the barrel, so I also ordered a Forster No-Go gauge from eabco.net, and as eabco.net didn’t have any Field Gages in stock, I ordered one of those from Amazon.
As the Forster directions say:
“The “No-Go” Gauge is used to set your headspace when installing a new barrel. Forster gauges allow for a very close .004” headspace setting with the Forster NO-GO gauge. SAAMI spec allows up to .010”. So if your action closes on this gauge it doesn’t mean you have excess heads space. … Only that its more than the gauge allows. We recommend NO-GO gauge for setting the headspace on a bolt action barrel installation. … We recommend the closer fitting NO-GO gauge for installing a new barrel on a bolt gun.”
A Field gauge is for checking that the headspace is not too long, after setting it with the No-Go gage.
Because the new varmint barrel had a different contour than the original Axis barrel, and the original Axis gunstock was made of webbed plastic, there was no easy way for me to re-cut the barrel channel in the gunstock.
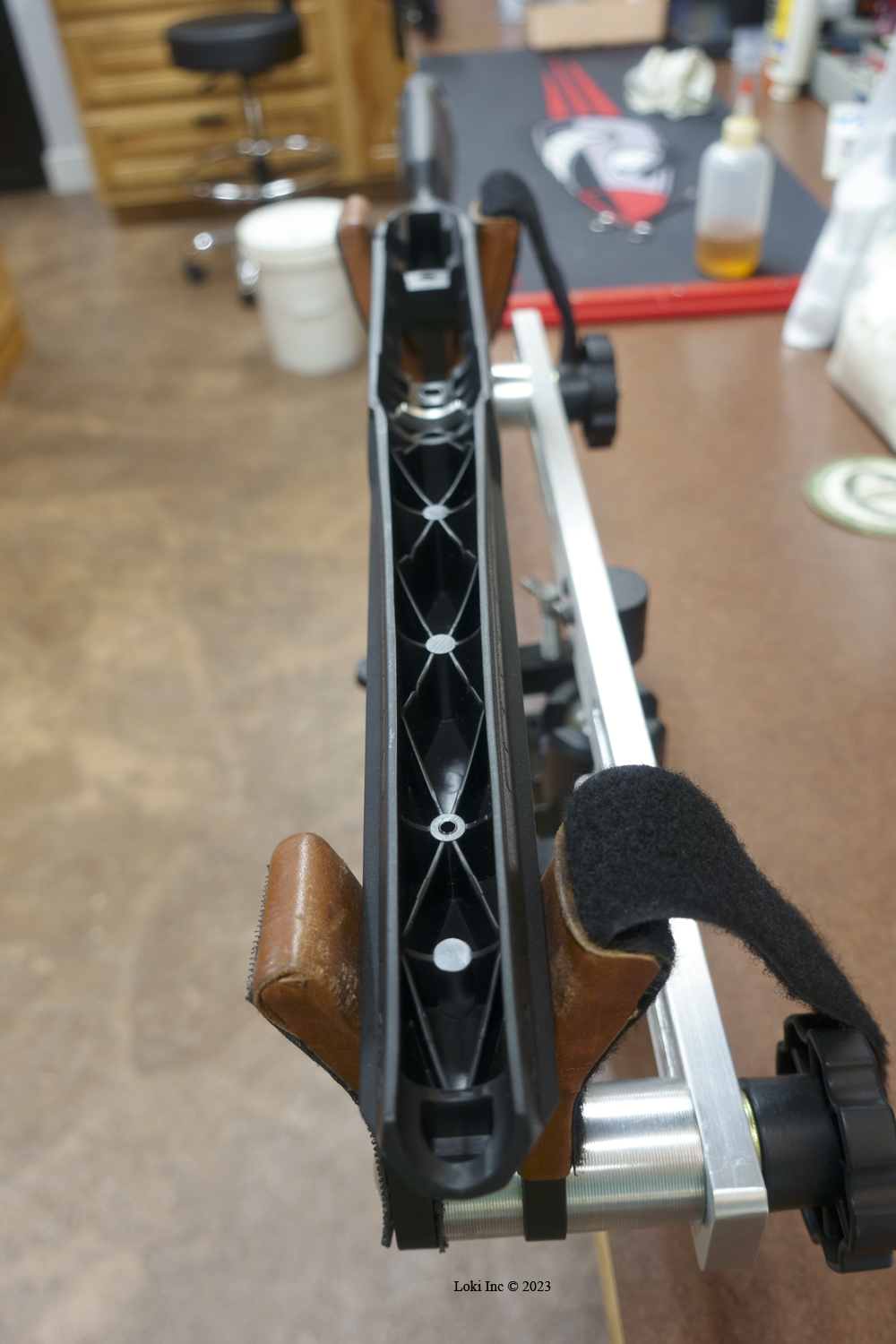
Barrel channel of original Savage rifle stock
Therefore, I needed a new gunstock. I spotted a Boyds Hardwood Pro Varmint gunstock on sale at Optics Planet that would fit my Axis with its new barrel, so I ordered it. I knew that it would take a bit of fitting to get the barrel channel relief I wanted, but I already had a set of barrel channel bedding tools that I could use for that task.
The receiver and chamber portion of the rifle fit well into the Boyds gunstock, but as I suspected I needed to cut some material out of the barrel channel to achieve a business card gap thickness between the barrel and the stock.
The stock came pillar bedded, and I may decide to glass bed the stock later after I shoot the reworked rifle, if I think it needs it.
I decided to improve the stock trigger on the Axis while I was doing all this other work on the rifle. What I did was similar to what the Hunting Gear Guy did, except that I already had a set of small gun springs and screws I could use. I recommend using springs specifically made for guns for the overtravel spring, and choosing the correct length instead of cutting coils off a longer spring. I also smoothed the mating surfaces (along the top) of the trigger sear – don’t try to do anything but slightly polish these surfaces, or you’ll make the trigger unsafe by taking off too much metal.
I wanted to mount a Leupold Mark 5HD scope on the rifle, and needed medium height rings to fit a 35 mm scope body diameter, so I purchased a set of Leupold Mark 4 rings for the project.
I assumed the scope base on the original Savage rifle was a Picatinny pattern rail, but when I checked the rings against it I was dismayed to find the rail slots were not in the Picatinny pattern; they were narrower and spaced differently than the slots on a Picatinny rail. I don’t know; they may have been Weaver pattern, but my rings wouldn’t fit in the slots.
So, I bought a Leupold Mark 4 one-piece base with a 20-MOA taper to fit a Savage 110 round receiver, after checking to make sure it would also fit the Axis receiver.
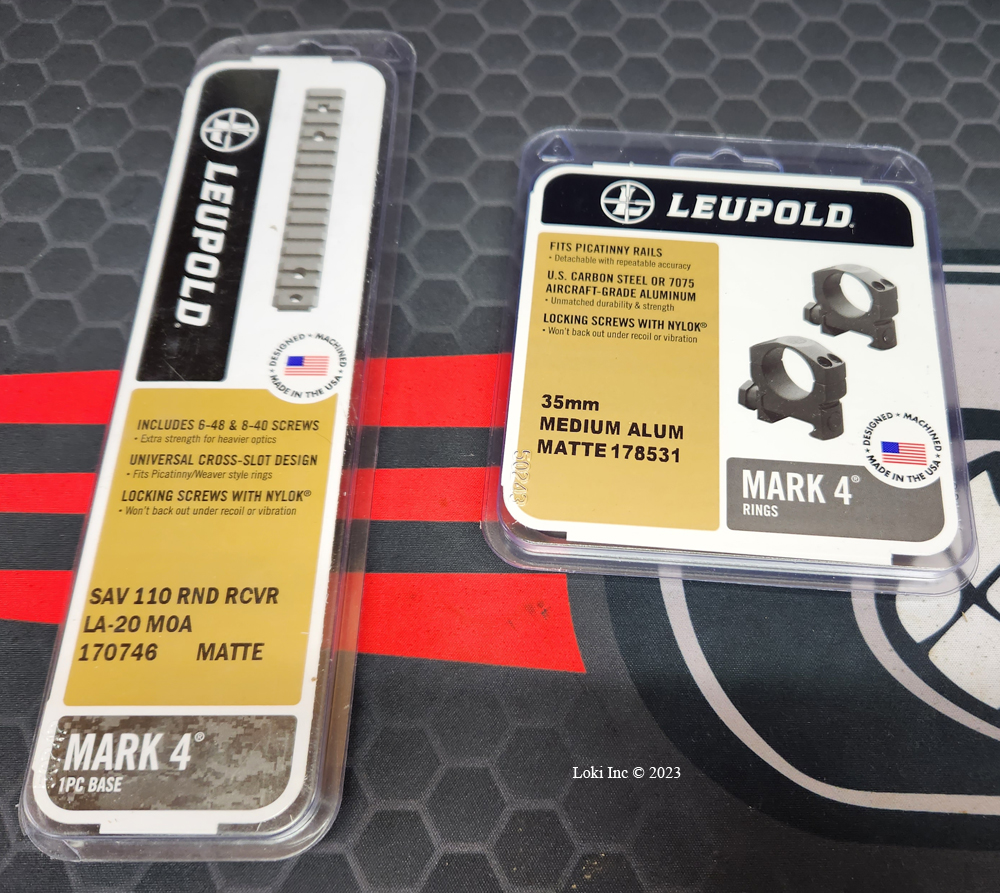
Scope base and ring set
Most of the aftermarket items made to fit the Savage 110 will also work on Axis receivers, but check before you invest in one. I removed the original Savage scope base rail, and cleaned the mounting holes with carburetor cleaner to degrease them. After letting the carb cleaner soak the mounting holes for a while, I used cotton swabs to absorb as much of the cleaner from the holes as possible, and then I blasted the holes with canned air to dry the remaining cleaner.
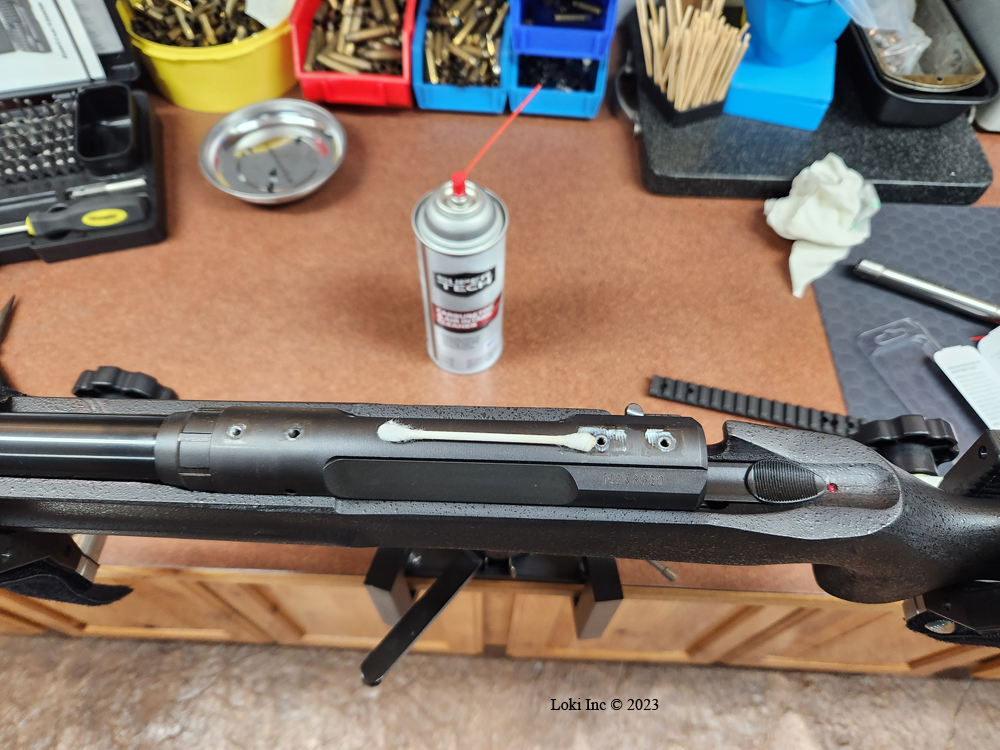
Degreasing receiver top and scope base mounting holes
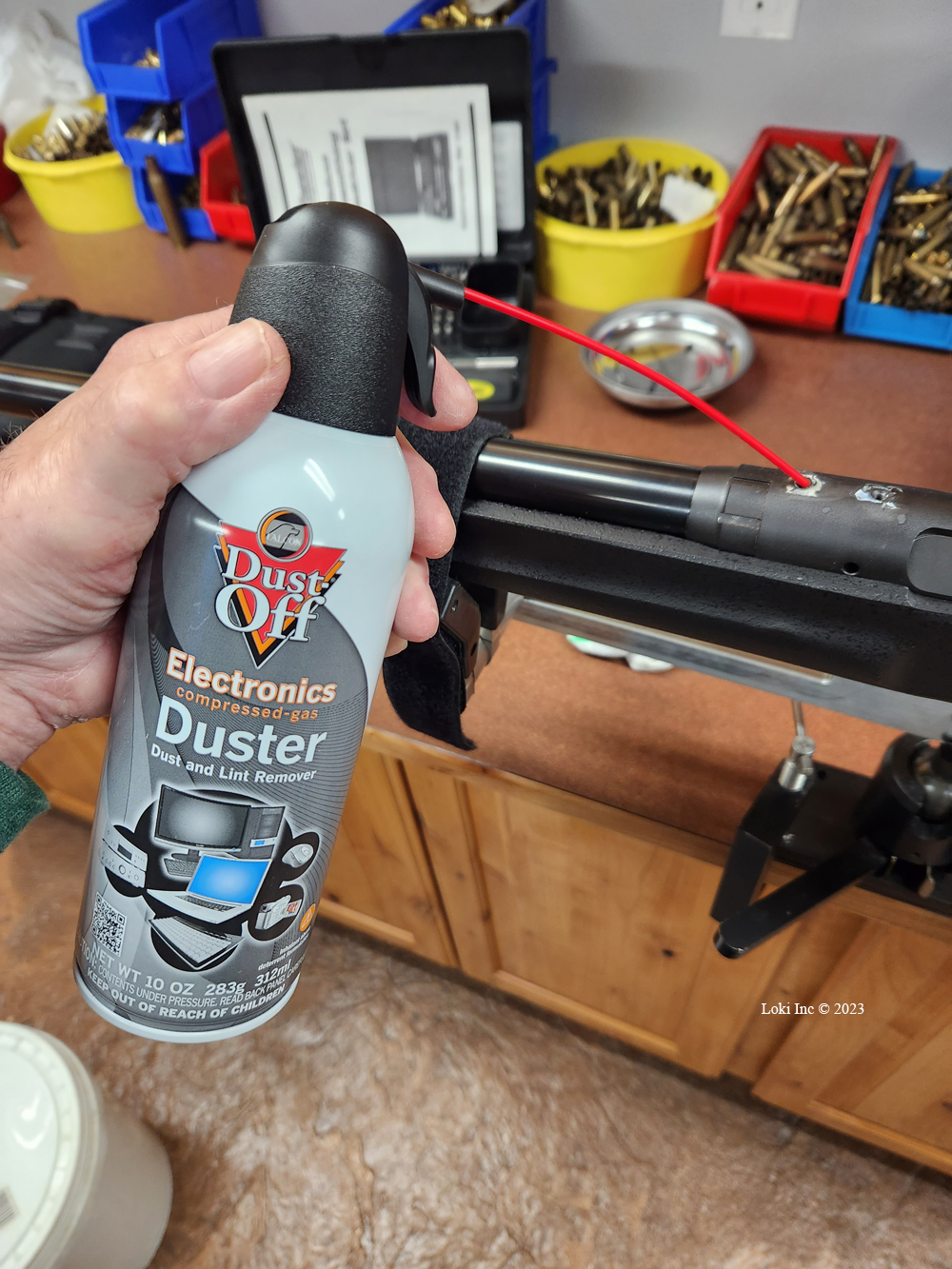
Drying degreaser out of mounting holes
The base came with both 6-48 and 8-40 screws. After pre-mounting the new Mark 4 base to make sure the screws would line-up with the receiver holes, and that the screws fit the holes, I used a torque wrench to secure the screws in the holes. The instructions that came with the base said to use 22 in-lbs for the 6-48 screws, and 28 in-lbs for the 8-40 screws.
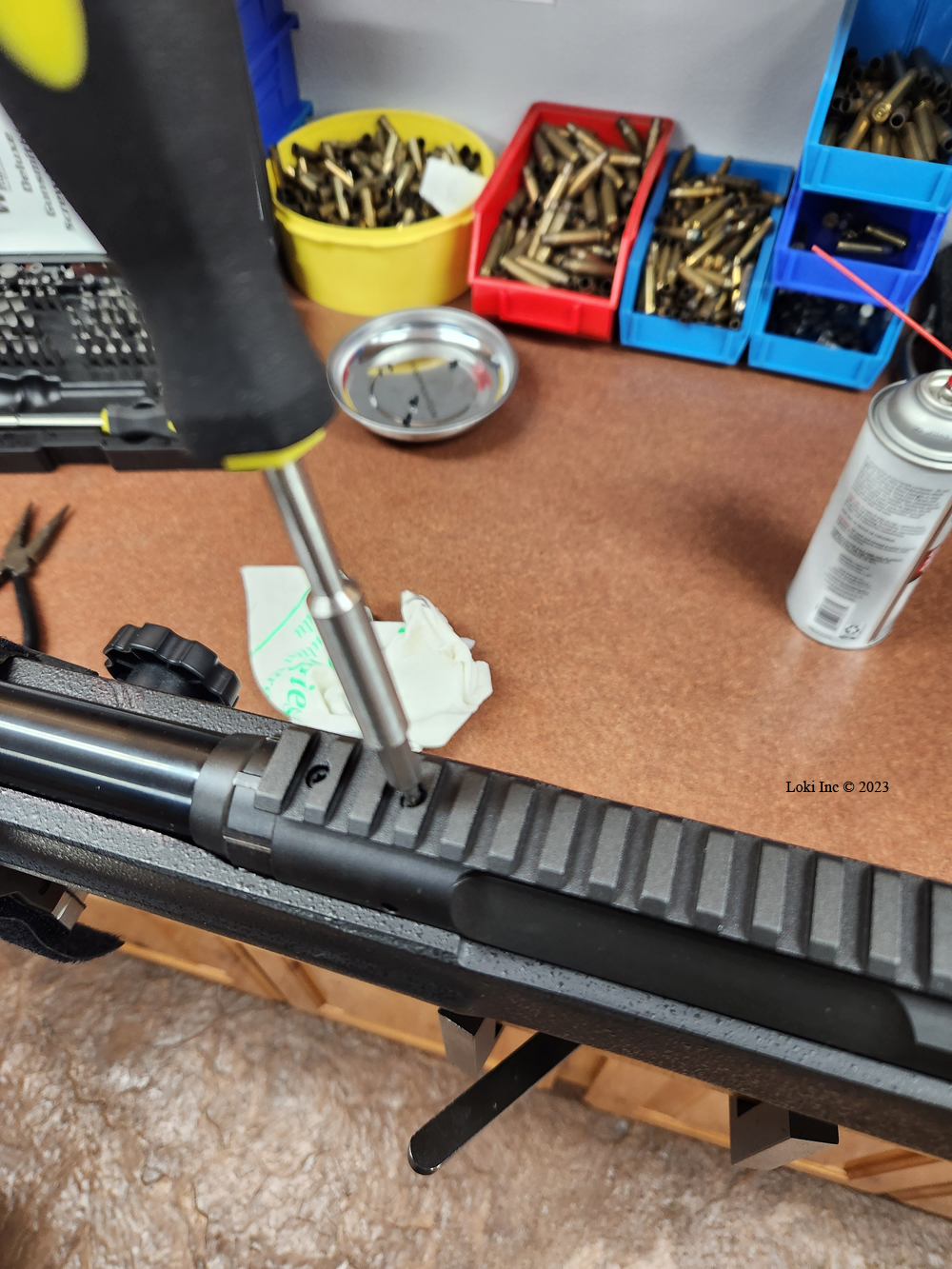
Installing scope base mount screws
Because the base had a 20-MOA taper, I had to be sure to mount the base in the correct orientation. To do this, I merely mounted the base with its arrow mark on the underside so the arrow tip pointed to the gun’s muzzle.
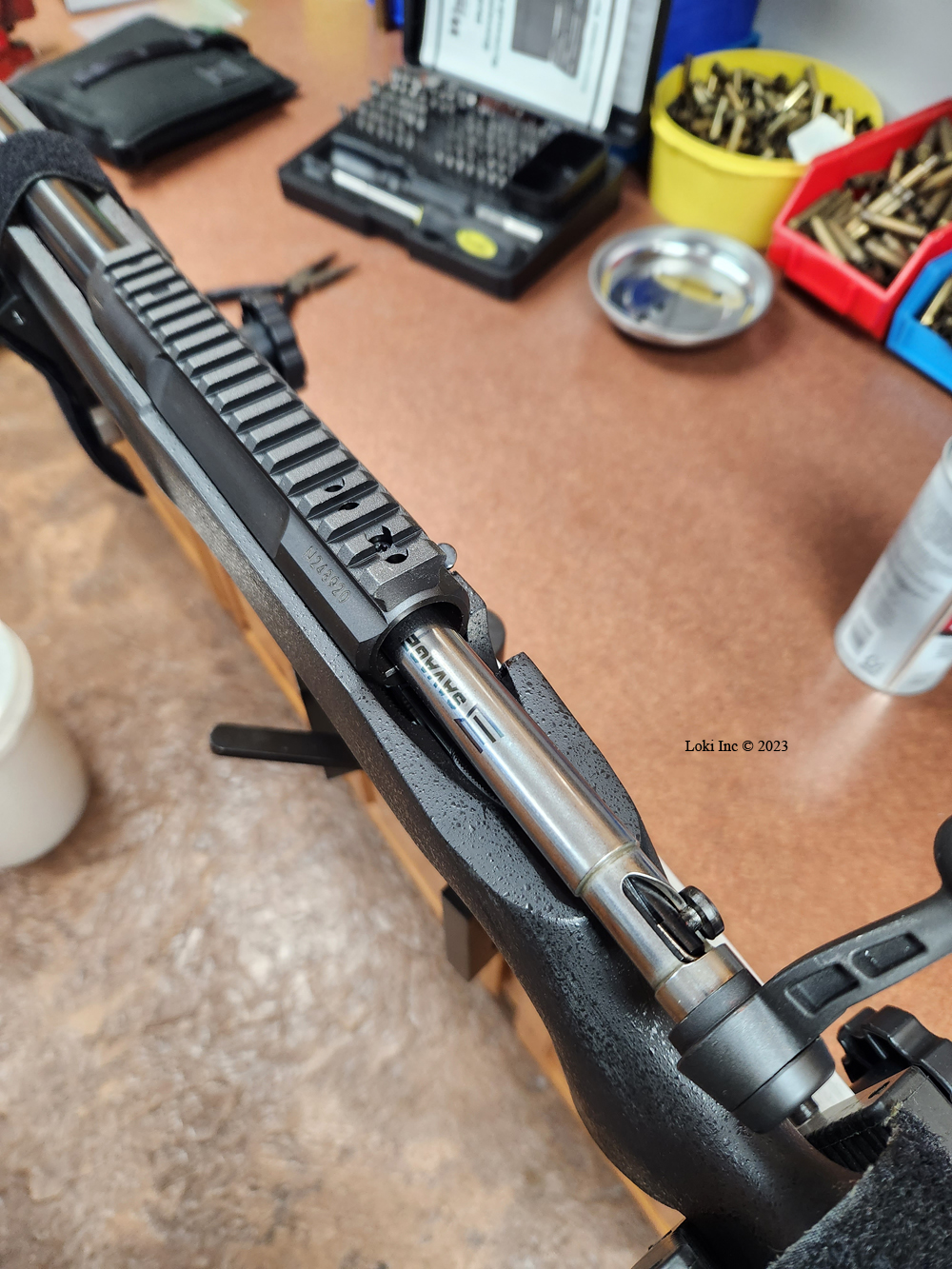
Scope base on receiver
Leupold used a Nylok® thread locking system on each of the screw threads for the base, so I didn’t have to use any liquid thread locker compound.
I removed the Torx screws holding the halves of the Mark 4 rings together, and positioned the lower halves on the base while ensuring the lug on each ring lower half engaged a slot on the rail. I set the variable-power scope to its highest magnification setting and carefully placed it onto the ring lower halves. I checked the front and rear ring positions to make sure they would hold the scope securely when fully mounted. I like to have the rings as far apart from each other as the scope will allow, giving the most stable scope mounting position.
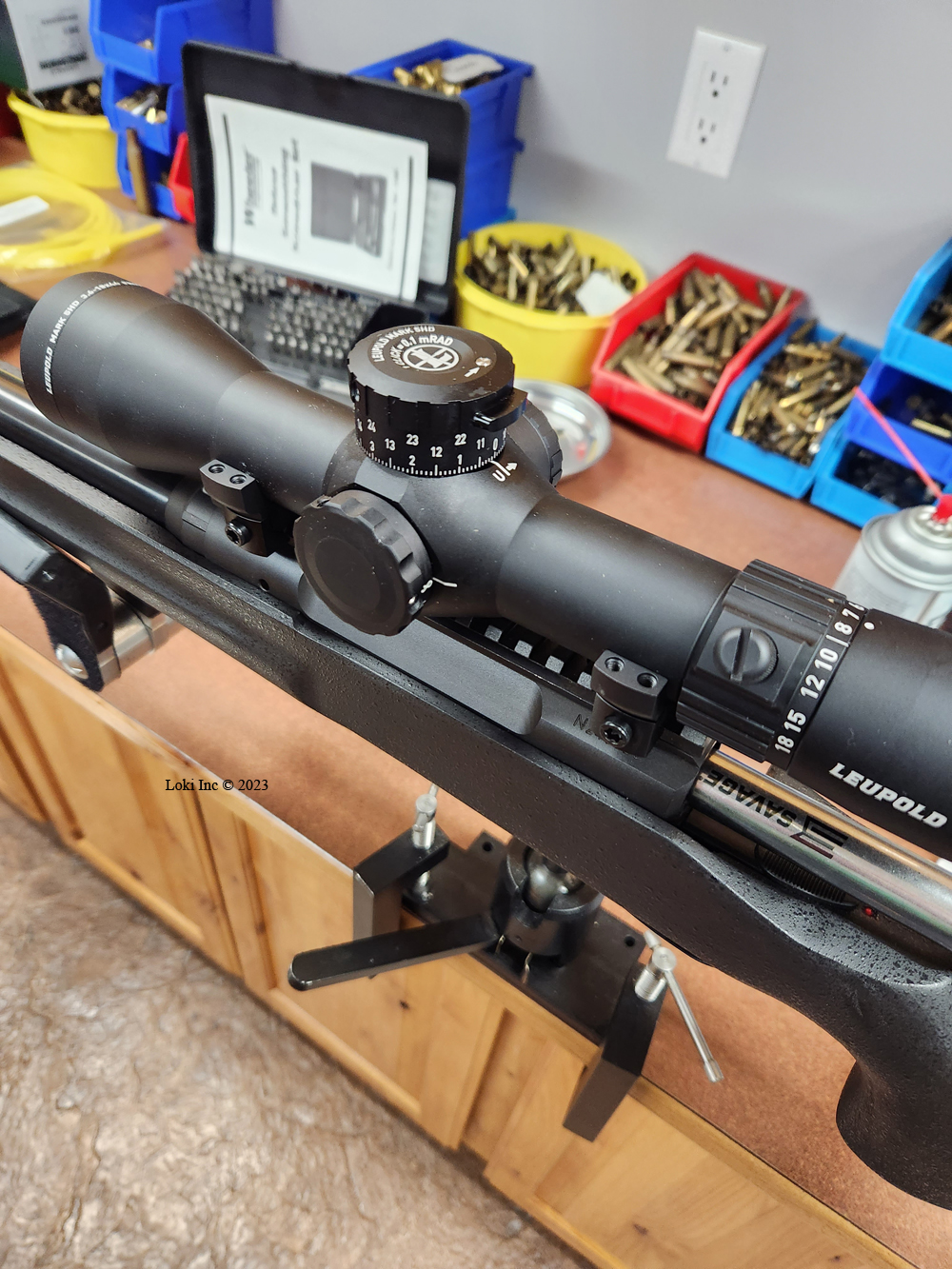
Placing scope on lower bases to check eye relief
Once I established the lower ring positions with respect to the scope, I loosely installed the upper ring halves onto their respective lower halves. I tightened the ring screws finger-tight, enough to keep the upper halves (and the scope) from falling off during the next step.
I carefully lifted the rifle to my shoulder to check the eye relief, or distance from the scope eyepiece to the shooter’s eye. One has the proper eye relief when vignetting is minimized while looking through the scope; to achieve this, I mounted the rifle to my right shoulder in the way I would instinctively when shooting, and then I looked through the scope while slightly moving the rifle forward and backward relative to my right eye. One achieves the correct eye relief when the circular area enclosing objects visible through the scope is maximized, while the dark border at the periphery of that area (the vignette) is minimized. Then, I moved the scope ring positions (with the scope in place) so that the vignetting was minimized.
Having decided where my scope would be fixed into position, I removed the ring upper halves and the scope, placed the rifle in my rifle vise, and used a small level on the scope base to level it.
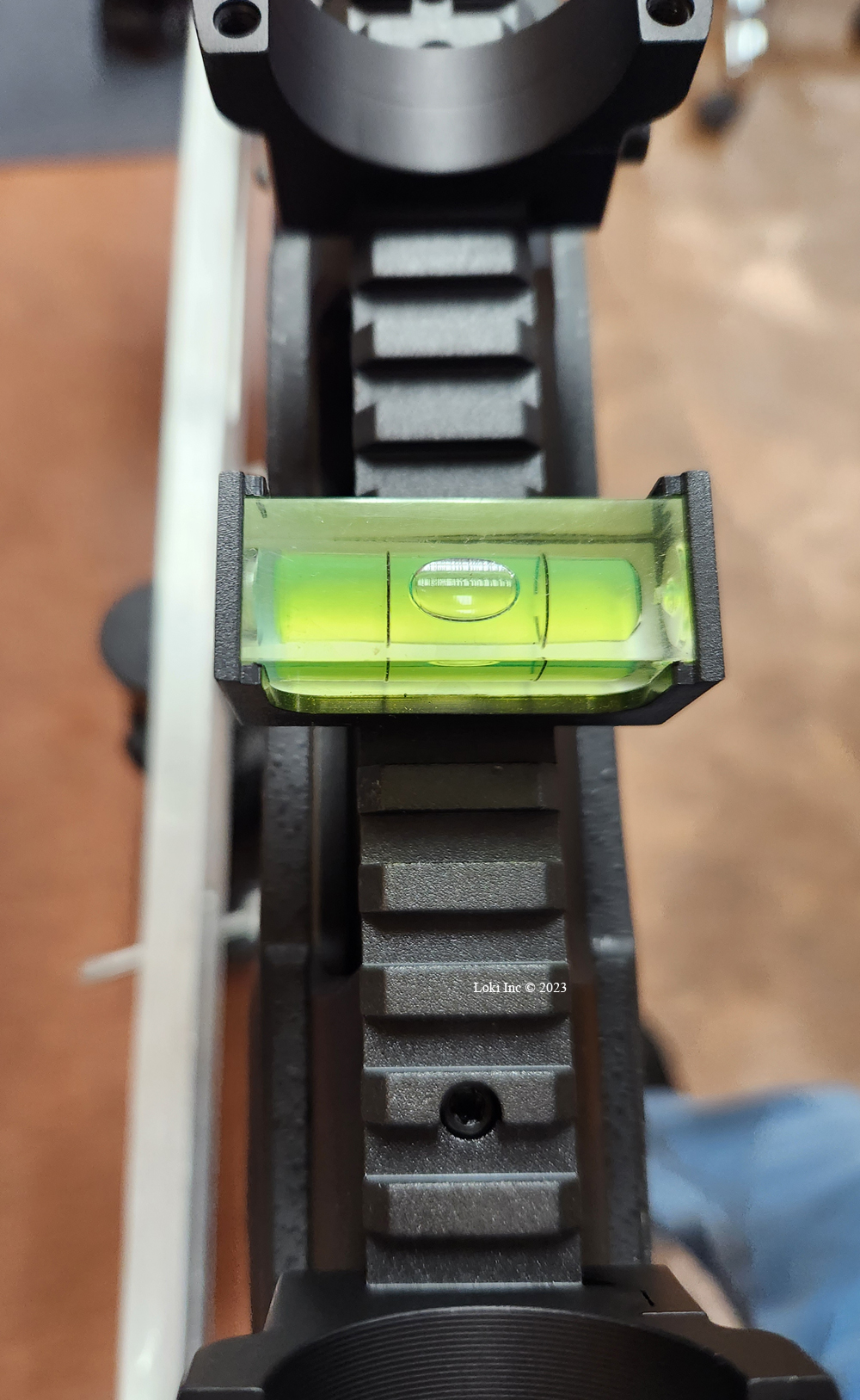
Checking level of base prior to leveling scope in rings
I also torqued each lower ring mounting bolt to the correct amount, 45 in-lbs, to secure the lower rings to the base in their correct positions while pushing each ring forward against its rail mounting slot.
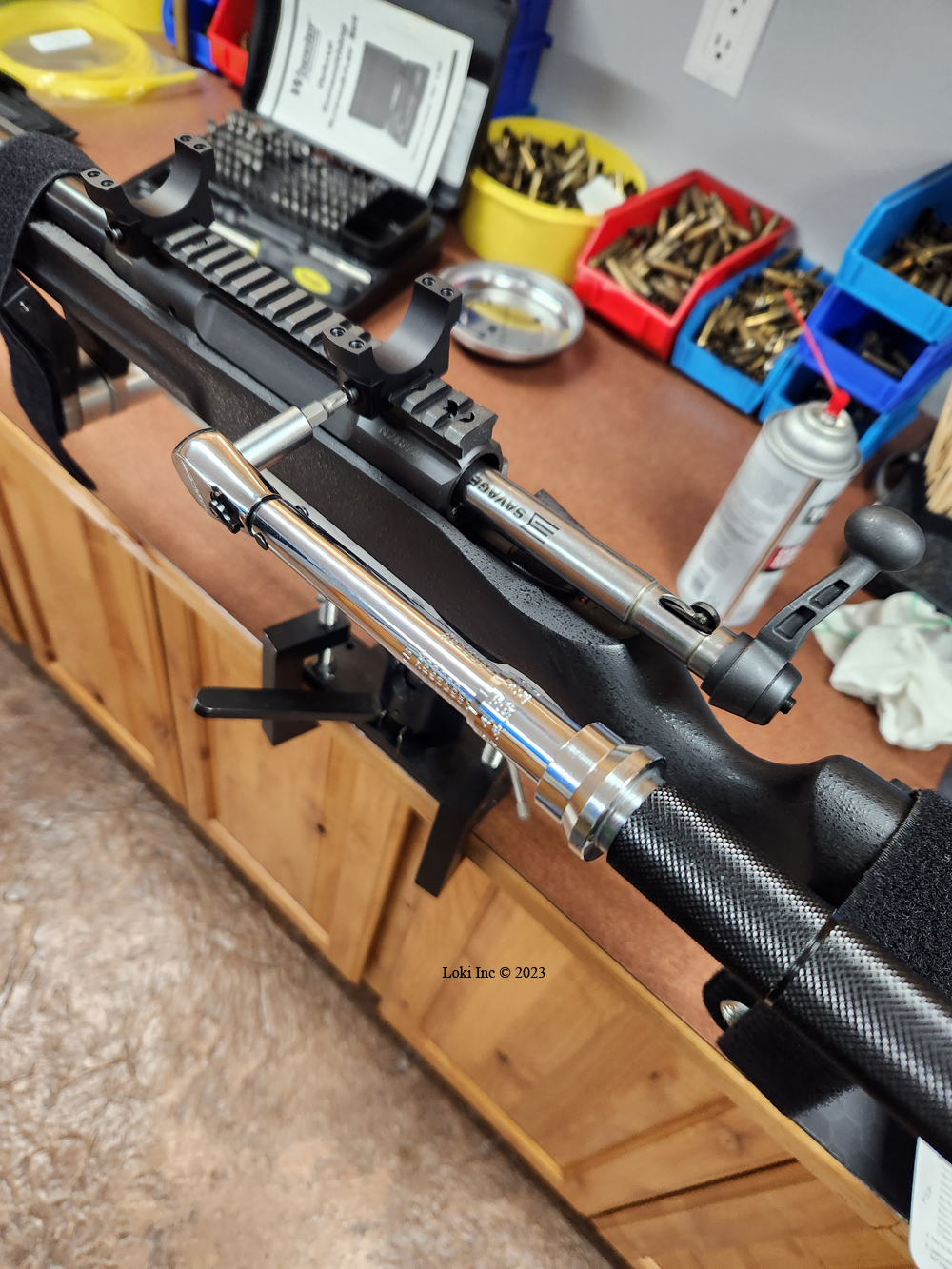
Using torque wrench to tighten lower halves of rings on scope base
Then, I put the scope back onto the lower rings and used my level atop the vertical crosshair adjustment turret to level the scope on the (already) leveled base.
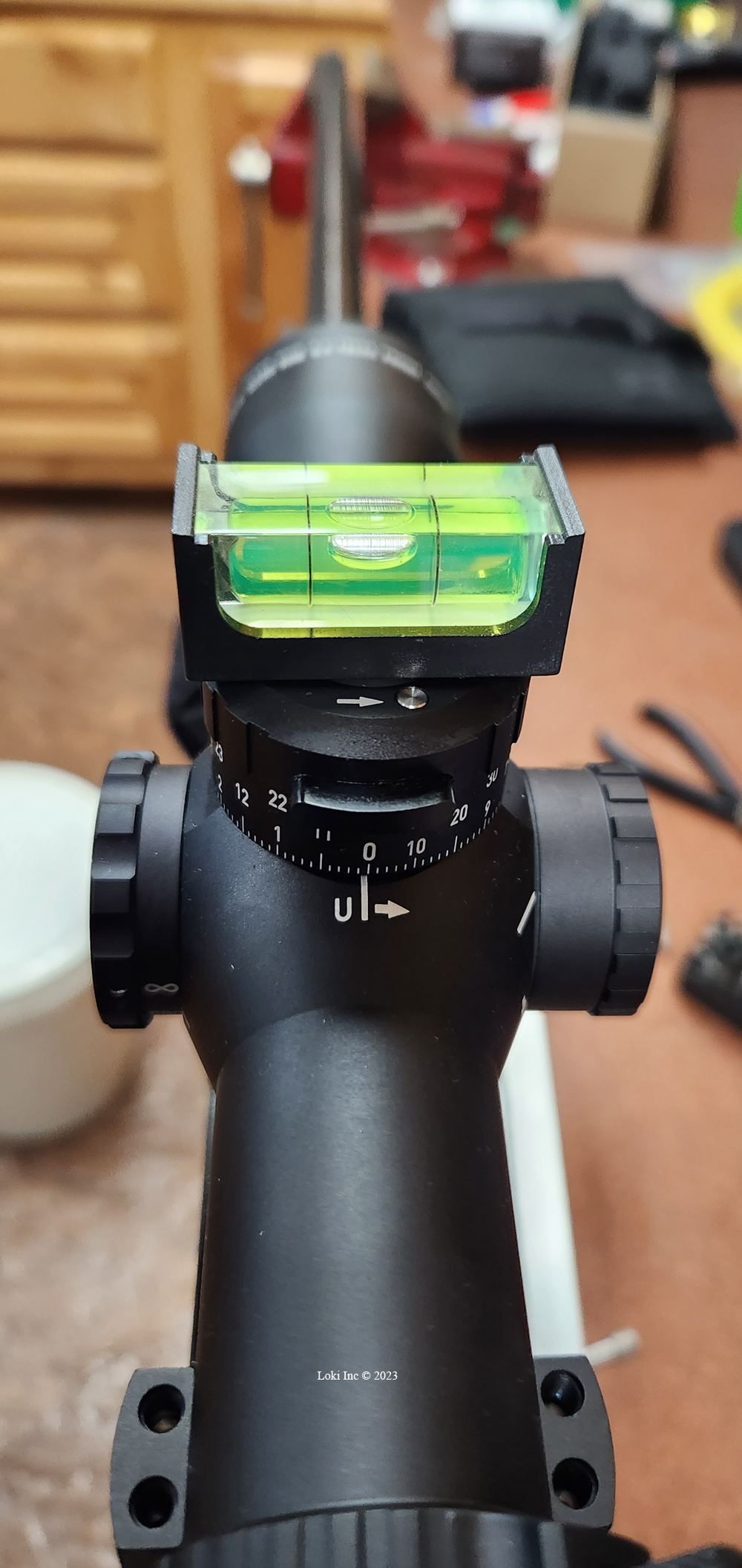
Checking level of scope prior to installing ring upper halves
Next, after installing the upper rings, I snugged the ring screws down enough to keep the scope from slipping or rotating. I shouldered the rifle to check that the eye relief hadn’t shifted, and that the crosshairs were vertical and horizontal. If not, or if there was a shift, I would have re-done those steps in the scope mounting process until the eye relief was correct and the crosshairs oriented correctly.
As with the base, Leupold used a Nylok® thread locking system on each of the threads on the ring screws, so no additional thread locking was required. I used my torque wrench and tightened the ring half screws to 28 in-lbs per the instructions that came with the rings.
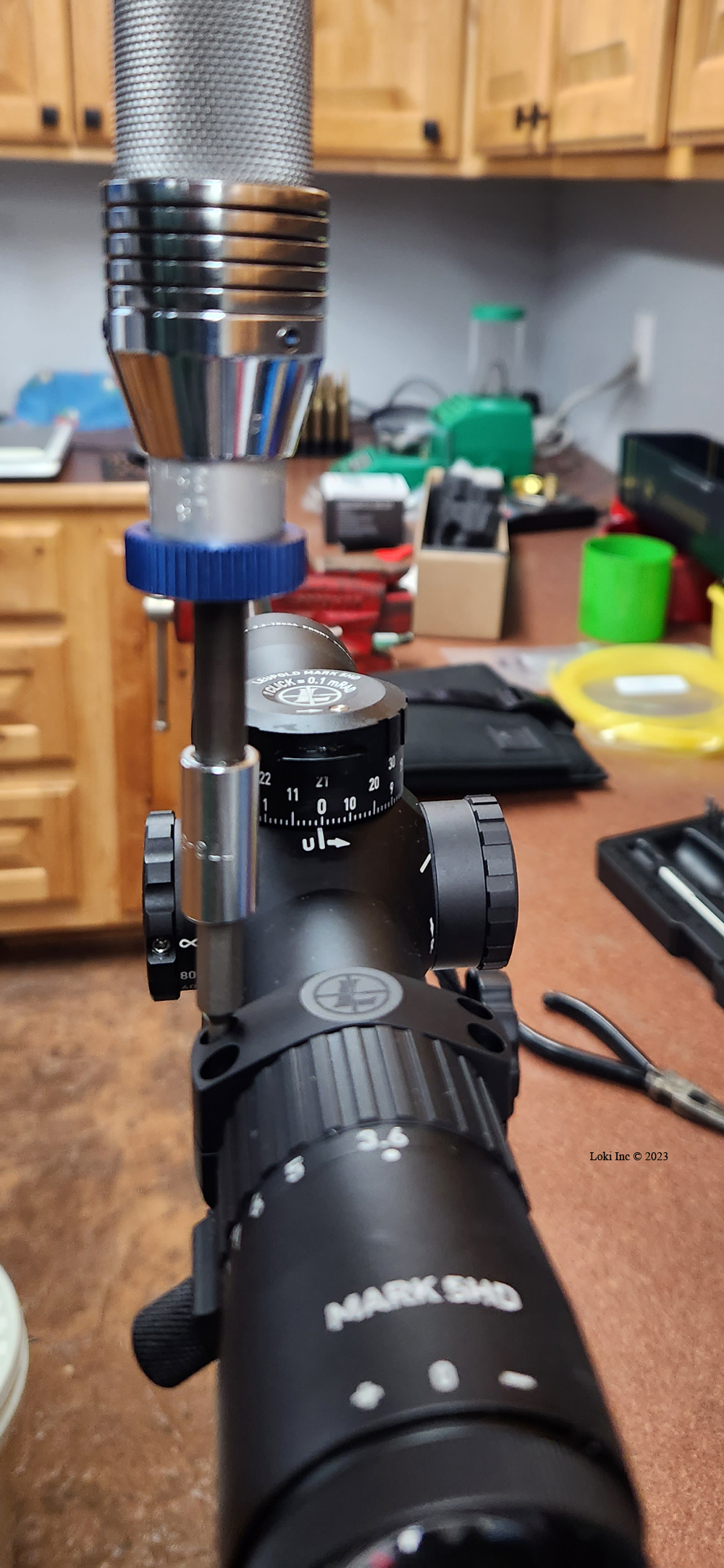
Using torque wrench to tighten scope ring screws
I made sure to use a crossing pattern when tightening the screws, gradually tightening them while checking the gaps between the top and bottom ring halves to ensure even spacing
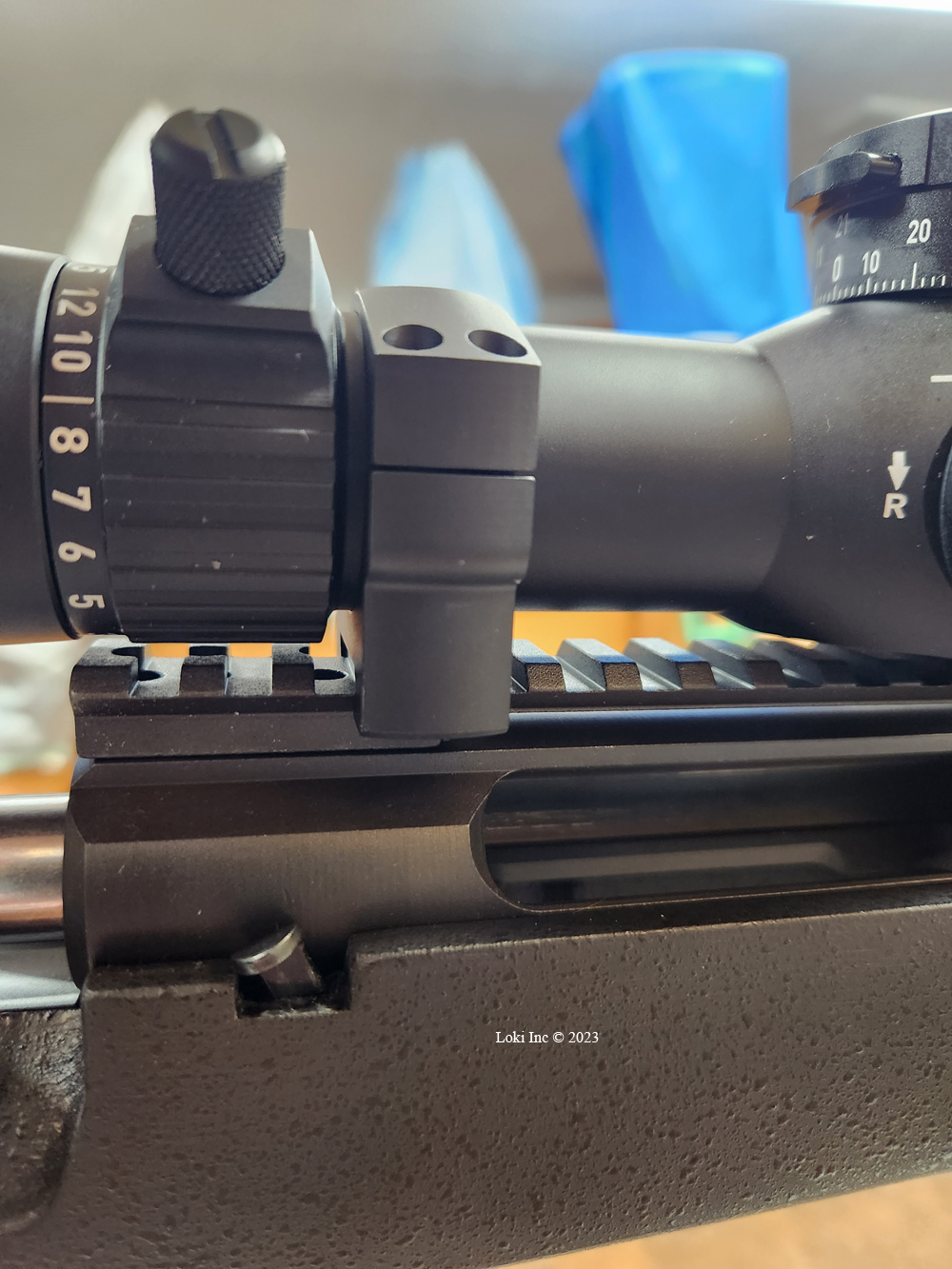
Ring gap right side
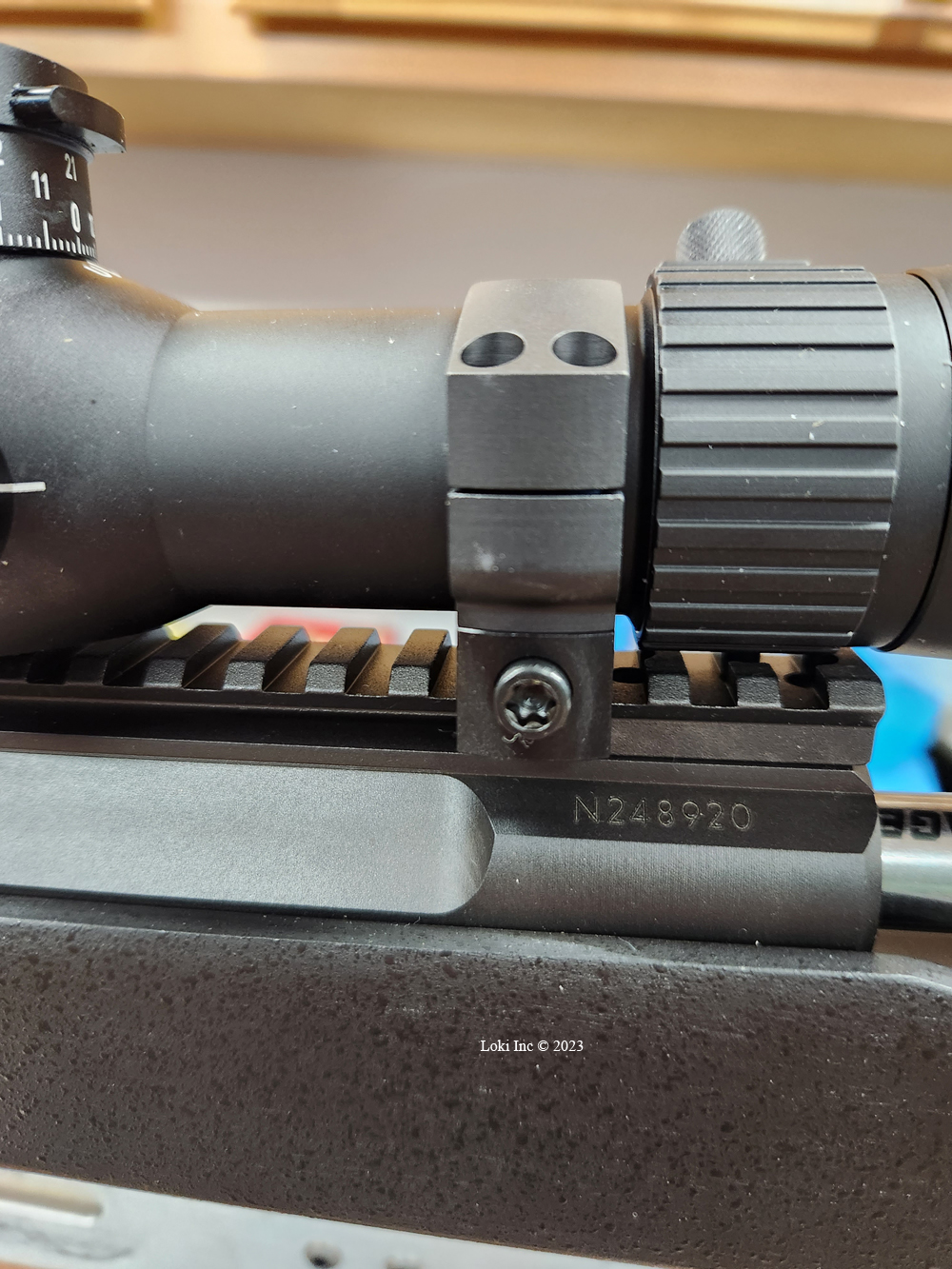
Ring gap left side
This is critical to ensure the scope rings exert an even squeeze on the scope.
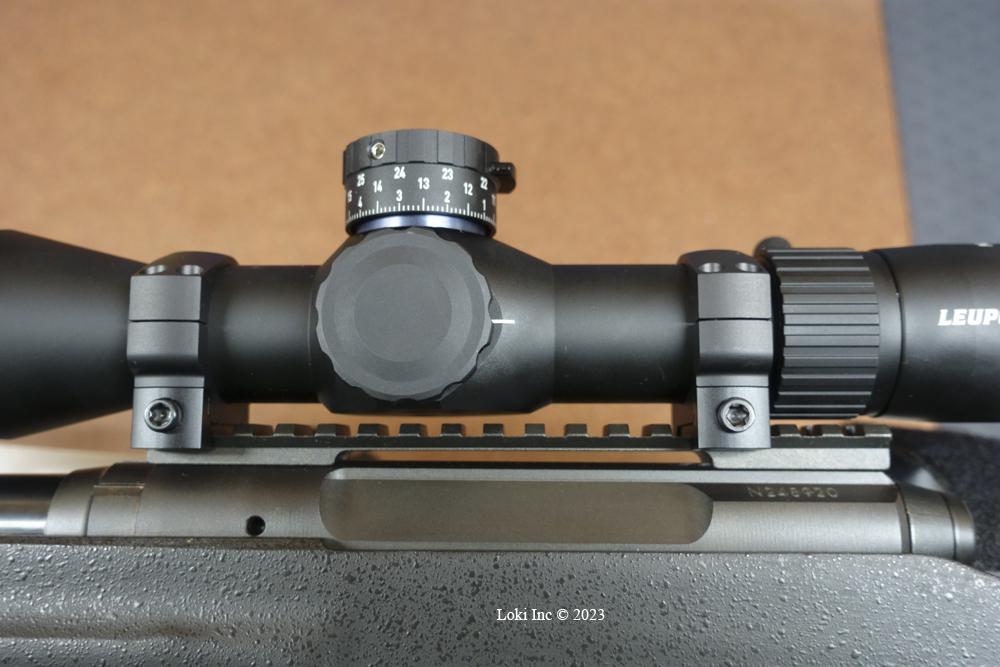
Scope mounted on 1 piece base
A sunshade came with the scope, and I purchased Leupold scope caps to complete the setup.
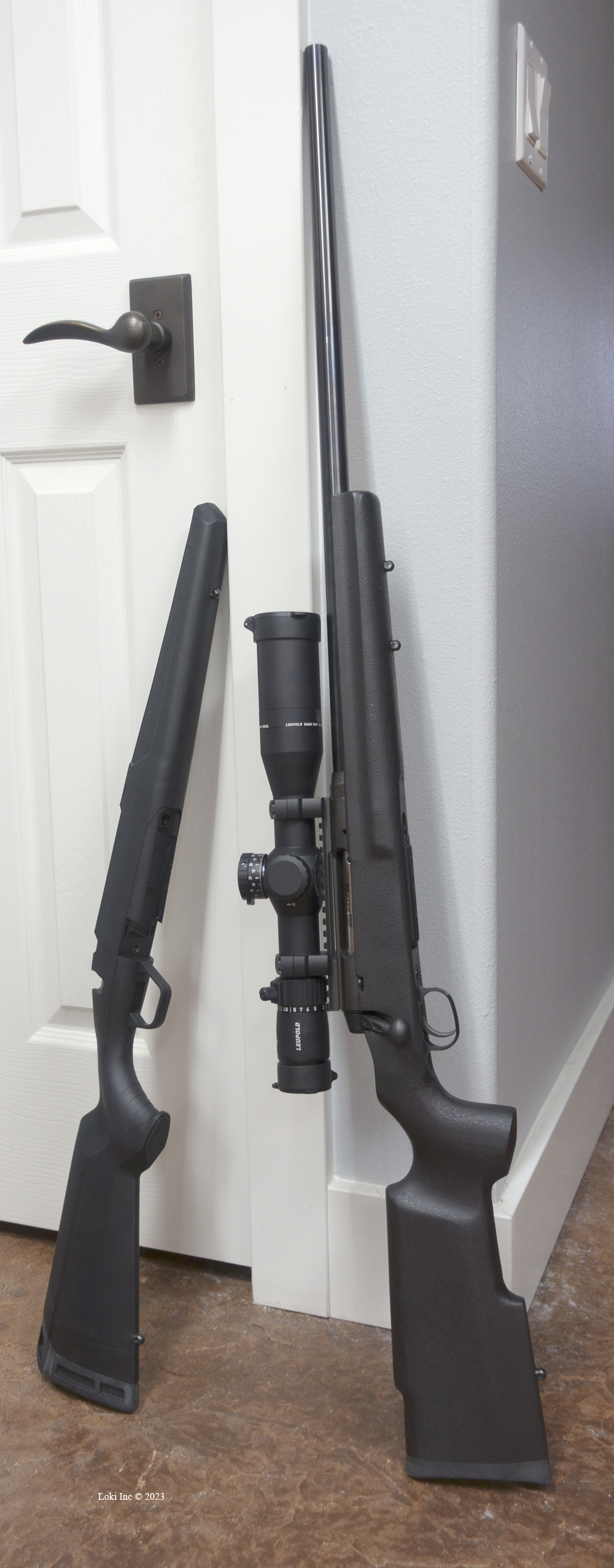
Reworked rifle next to original Savage rifle stock
I now had a well-mounted scope system that, when combined with my new rifle system and tuned handloaded ammunition, proved very accurate at long ranges.
Review: Hornady 190-Grain Sub-X Ammunition and Bullets for 300 AAC Blackout
This is a review that focuses on the overall performance and comparison of factory versus handloaded ammo. Specifically, I used the Hornady 190-grain, Sub-X ammunition and bullets for my .300 AAC Blackout rifles.
I own several guns in .300 AAC Blackout caliber, and only one is not based on an AR semi-automatic action. It’s a Ruger American Ranch rifle, a bolt-action with a short, threaded barrel. I bought it purposely for varmint hunting, and chose the gun and the caliber so I could make the system as quiet as possible when pairing it with a suppressor.
For a while, I had to contend with having only non-expanding bullets available for my .300 hunting ammo, whether in factory ammo or for my handloads, because I wanted subsonic ammunition. This would eliminate the supersonic “crack” noises from the bullets as they traveled downrange, trailing their sonic shock waves along behind them. Achieving subsonic speed, along with good terminal performance, typically means using a big, heavy, but streamlined bullet.
Unfortunately, those streamlined projectiles do not expand at subsonic striking velocities, as they were designed for centerfire rifle ammo. They have good terminal performance at high striking velocities, but poor expansion in animals at the slow projectile speeds I want in my system. I did a lot of .300 cartridge reloading with different projectiles in the 190 to 220 grain range, trying to get a good combination of powder load, projectile weight and shape that would be subsonic at the gun’s muzzle, accurate and have good terminal performance. Alas, all I was able to achieve was a bunch of .30 caliber holes through and through the targets. Ditto with factory ammo.
Hornady 190-Grain Sub-X Ammunition and Bullets for 300 AAC Blackout
In a happy coincidence, at about the time I was ready to give up and accept poor terminal effects, Hornady Ammunition released its 30 cal .308 190 grain Sub-X® bullets to the handloading community.
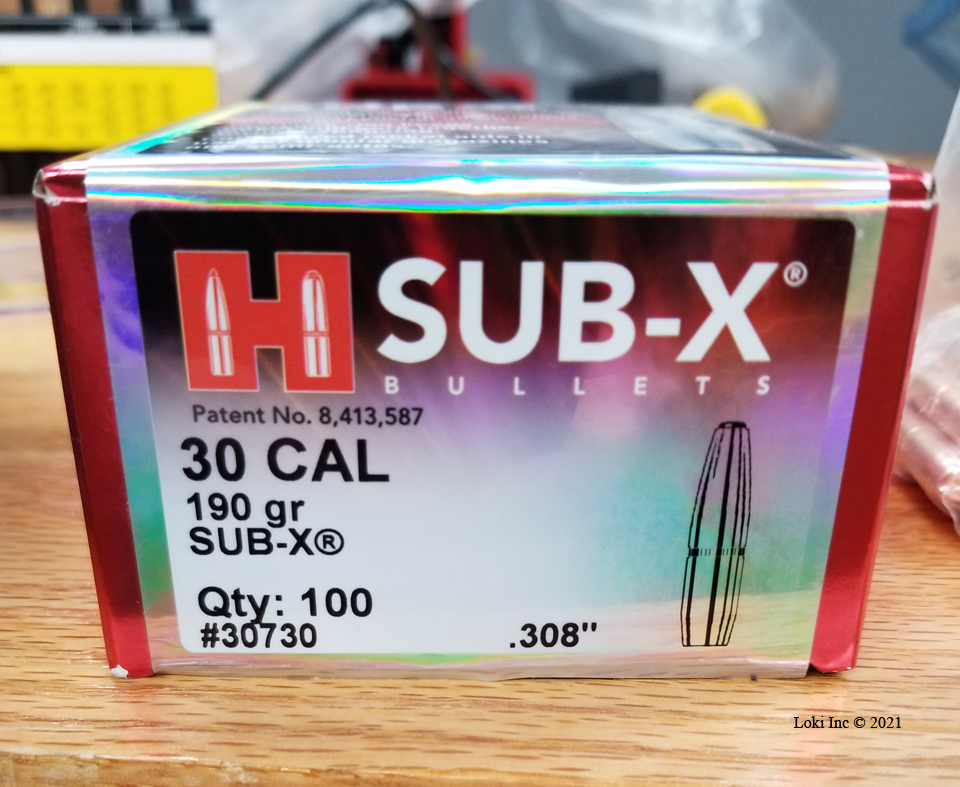
Hornady Sub-X® bullets details
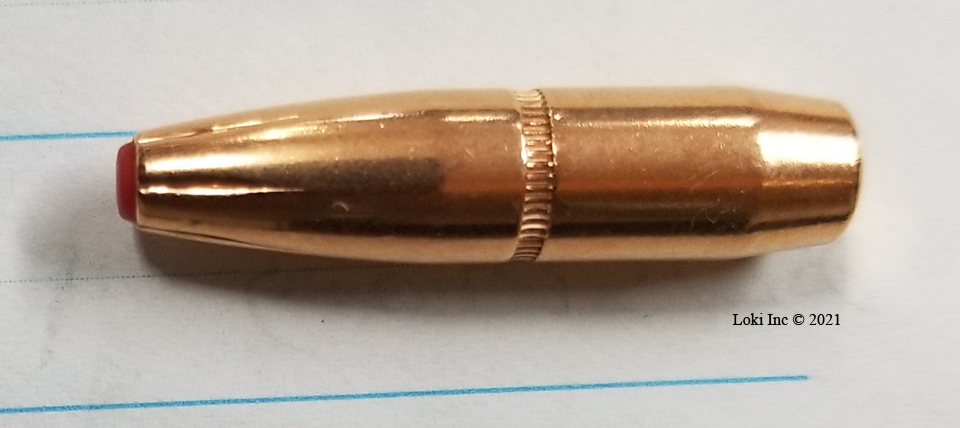
Hornady Sub-X®bullet
Hornady advertised that the bullet design was optimized for ballistic performance at subsonic velocities, as well as reliable expansion in an animal target. Soon afterwards, Hornady introduced rifle ammo using the same bullet, the 300 Blackout 190 grain Sub-X® Subsonic.
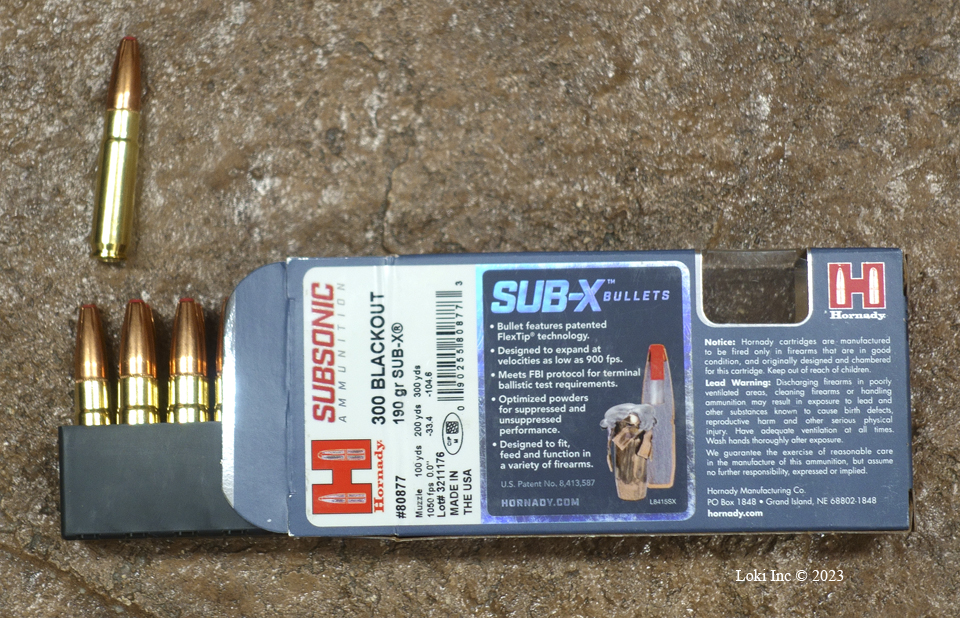
Hornady Sub-X® 300 Blackout factory ammo
First, I acquired enough Sub-X® bullets to run handloads for load development, and then for testing on varmints. I had finished my load development and was busy busting armadillos and raccoons with the ammo when Hornady released the factory loads. So, I acquired a couple of boxes of the loaded Sub-X® rounds for comparison to my handloads.
The Reloading Process
For my handloads, I had difficulty finding new cases so I used 100 demilitarized, once-fired, FC 15 5.56 x 45 mm NATO caliber cases, cut-down and re-formed into .300 AAC/Blackout cases (7.62 x 35 mm). Because they were “remanufactured” cases, I checked a small sample for their maximum trim length to be no more 1.368 inches and they were okay. I then checked the neck dimensions (outside diameter no more than 0.3340 inches, and thickness no more than 0.013 inches) and as I suspected, about half were not OK.
Why did I check the necks?
Experience with remanufactured .300 cases made me alert to over-thick case necks. Because the cases are made from 5.56 cases, and are shorter than the parent cases, the resulting neck metal comes from the parent case body instead of its neck. Case bodies, particularly military case bodies, tend to be thicker than the necks. Over-thick necks on .300 cases can cause them to jam during feeding or extraction, and can lead to higher chamber pressures than intended.
Not having a neck trimming tool that would work on the .300 cases, I used my mini lathe to thin the necks of the offending cases. Next, I lubed the cases then decapped and sized them with the full-length sizing die from my Lee die set – three times through the sizing die, rotating the case 90 degrees after the first time through.
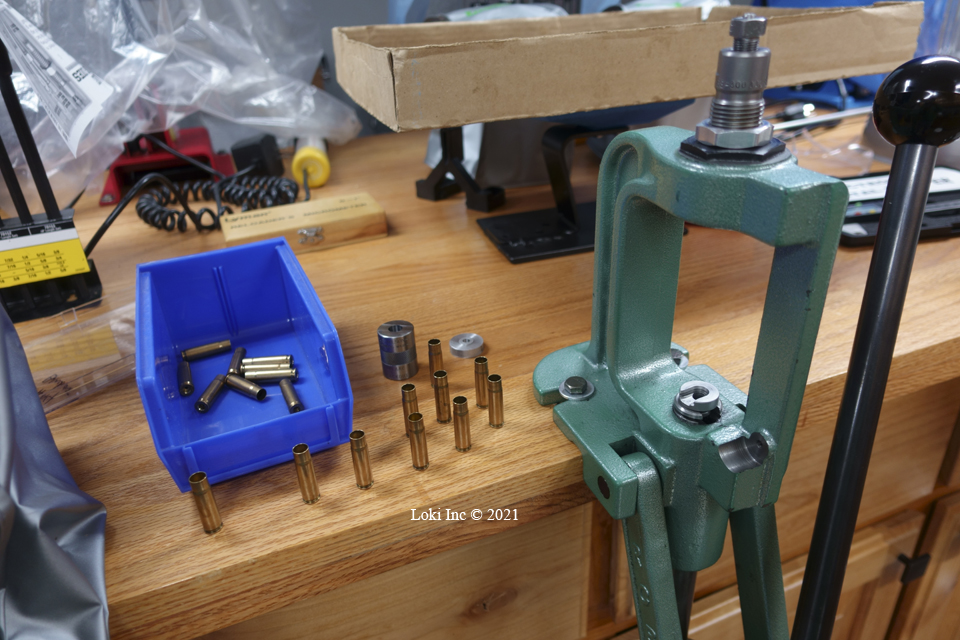
Resizing .300 AAC Blackout cases
I reamed the case primer pockets and cut the primer crimps (they were former military cases, so the primers were crimped) with a Hornady Small Head Primer Pocket Reamer chucked in a hand-held drill. I then deburred the case mouth of each case, inside and outside, with an RCBS Deburring tool.
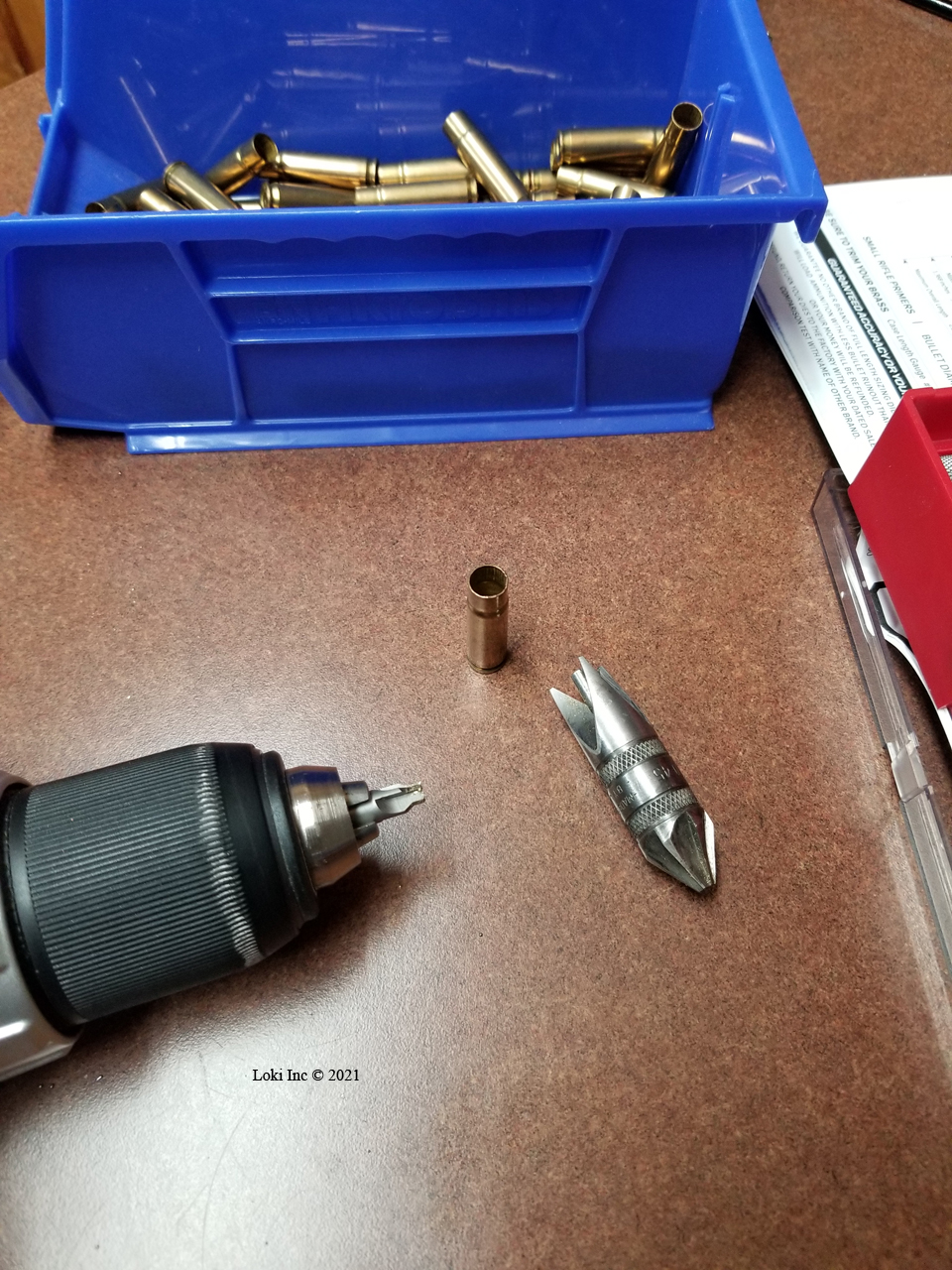
Trimming sized cases
I also used a Lyman Flash Hole Uniformer to remove the small burrs from the primer flash holes created when the holes were punched during case manufacture. The uniformer also cuts those holes to a consistent size and shape, as long as they are close to the center of the primer pocket. If they aren’t, the tool will let you know by its feel that it is trying to center the holes. Check those cases, and throw them out if the holes are off-center.
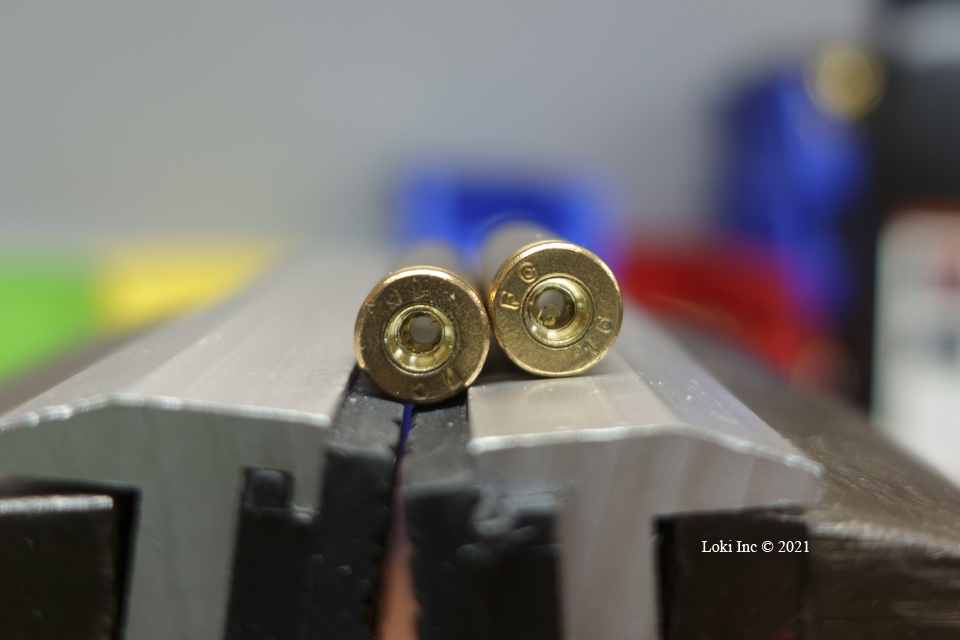
Cases with problem primer flash holes
I primed the cases with Remington #6 ½ Small Rifle Primers, then dropped powder into them Since Remington primers are no longer for sale, any good quality standard small rifle primer will work as a substitute. I loaded five cases, each, with 9.6 grains of H110, and five cases, each, with 11.0 grains of AA1680.
Lastly, I seated each bullet to center of its cannelure (corresponding to an overall length of 2.050 inches), and used the Lee factory crimp die to put a medium crimp on each case mouth.
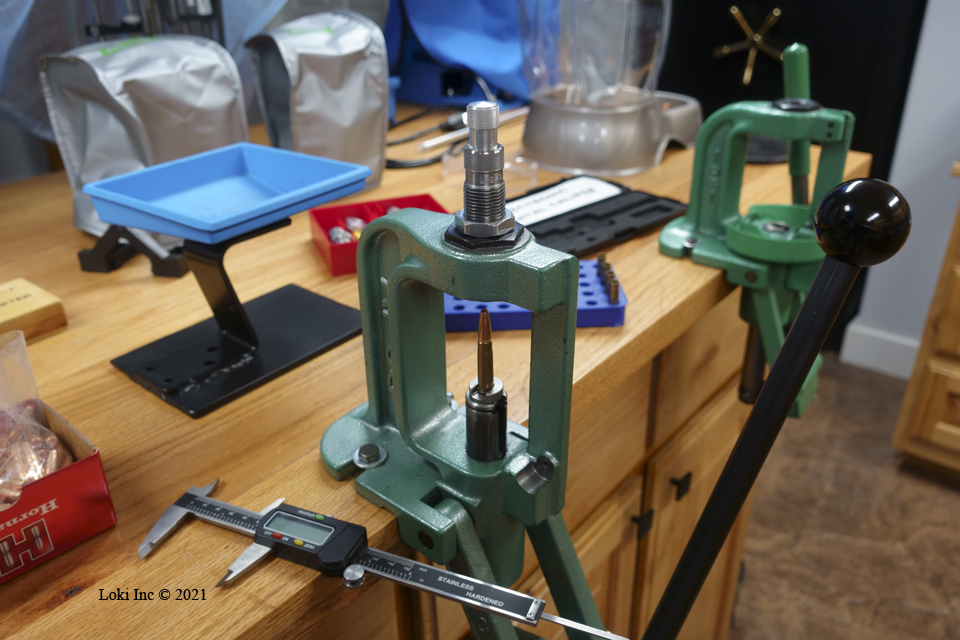
Seating 190 grain Sub-X®bullet in .300 AAC Blackout case
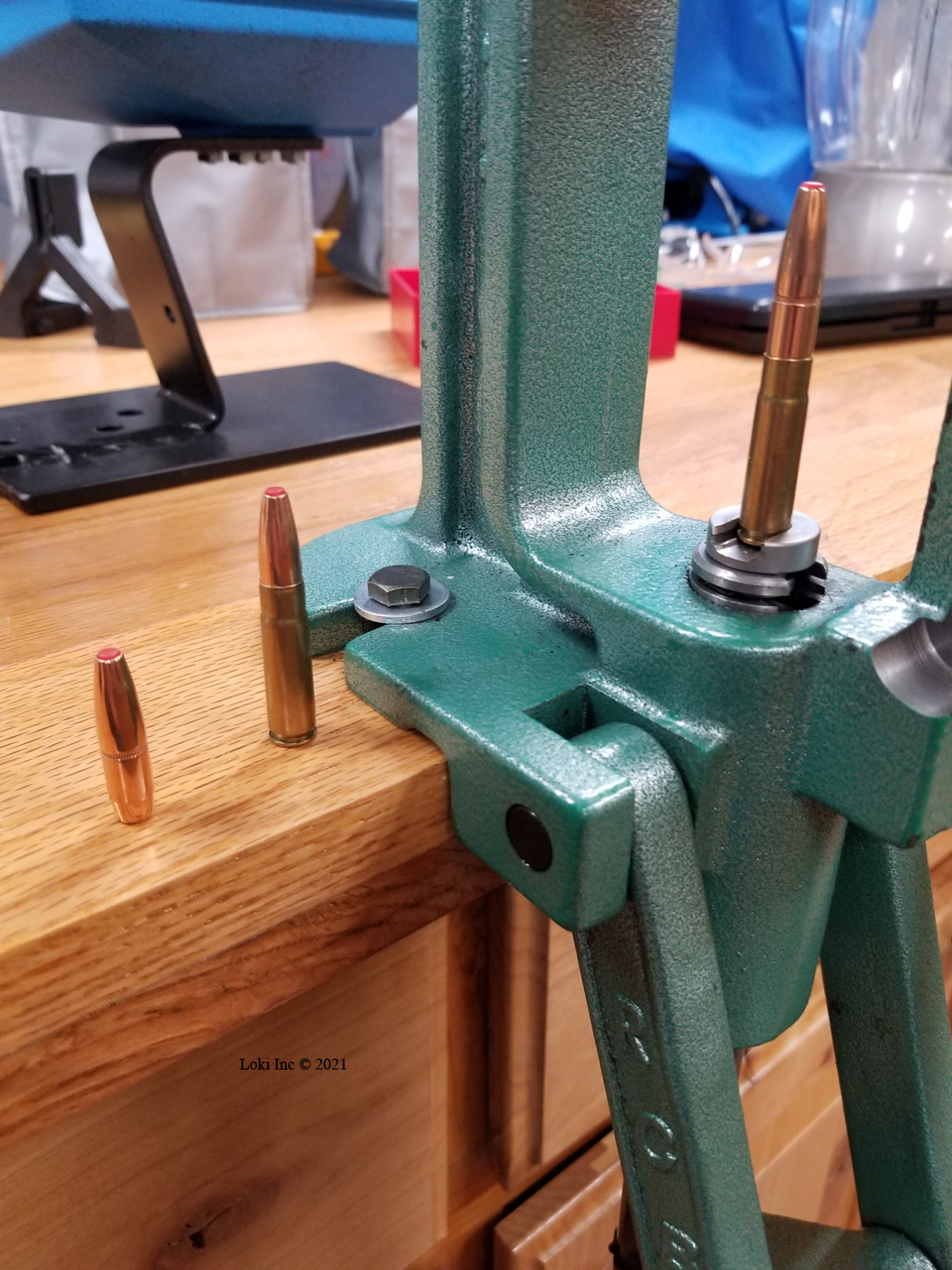
Loading press with bullet to be seated, bullet, and completed round
At this point, I double-checked the case necks to make sure each was less than 0.3340 inches in diameter so they would feed and perform correctly in my rifle. They were all okay [photo – Finished .300 AAC Blackout round with 190 grain Sub-X® bullet].
Range Testing
I test-fired the loaded rounds at a 50-yard target across a Magnetospeed chronograph; the average temperature was 63.5F [photos – Magnetospeed chrono mounted on Ruger American rifle, Ruger American rifle with Magnetospeed chrono ready to test .300 AAC Blackout handloads]. My projectile velocity goal was slightly less than the speed of sound, which, for my location and the temperature was about 1120 feet per second (fps).
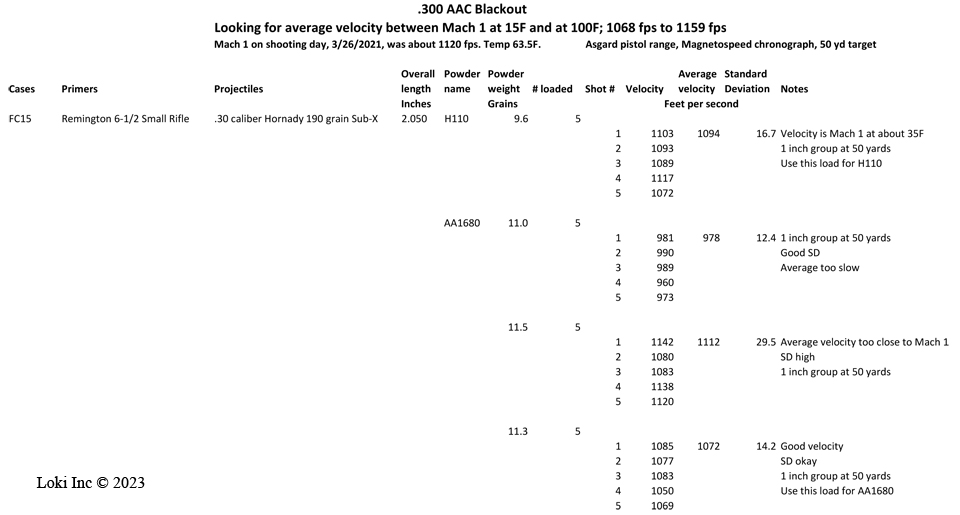
Shooting data Hornady 190 grain Sub-X
The H110 shots averaged 1094 fps, with a Standard Deviation (SD) of 16.7 fps, so I stayed with this load. The AA1680 shots averaged 978 fps, with an SD of 12.4 fps; this average velocity was too slow, so I decided to adjust the load. Even though I wasn’t particularly focused at this stage on group size, each load I shot produced groups of less than an inch at 50 yards. This is sufficient for shooting medium-sized varmints such as armadillos or raccoons under the conditions where I hunt them (dense woods and overgrown fields).
Because of the shooting tests, I loaded five more cases the same way as before, except for using 11.5 grains of AA1680.
Shooting Tests
I fired them under the same conditions (one advantage of having a range right outside your loading area door is that you can quickly go back and forth between the loading bench and the range), and their average velocity was 1112 fps, with an SD of 29.5 fps; the average was too fast, and the SD was higher than I like.
Therefore, I loaded five more cases the same way as before, except for using 11.3 grains of AA1680.
Once again, I fired them under the same conditions, and their average velocity was 1072 fps with a SD of 14.2 fps, so I stayed with this load. The group size of this load was also under an inch at 50 yards.
Based on this shooting data, and the fact that 11.3 grains of AA1680 more completely fills the case volume than 9.6 grains of H110, I loaded 50 rounds using 11.3 grains of AA1680 in the same manner as before to use for varmint hunting. Now, it was time for comparison testing of my handloads and the factory ammo.
Field Testing
I live in a target-rich environment when it comes to varmints, and was able to try each type of .300 AAC Blackout ammunition, factory and handloaded, against several 10s of these creatures.
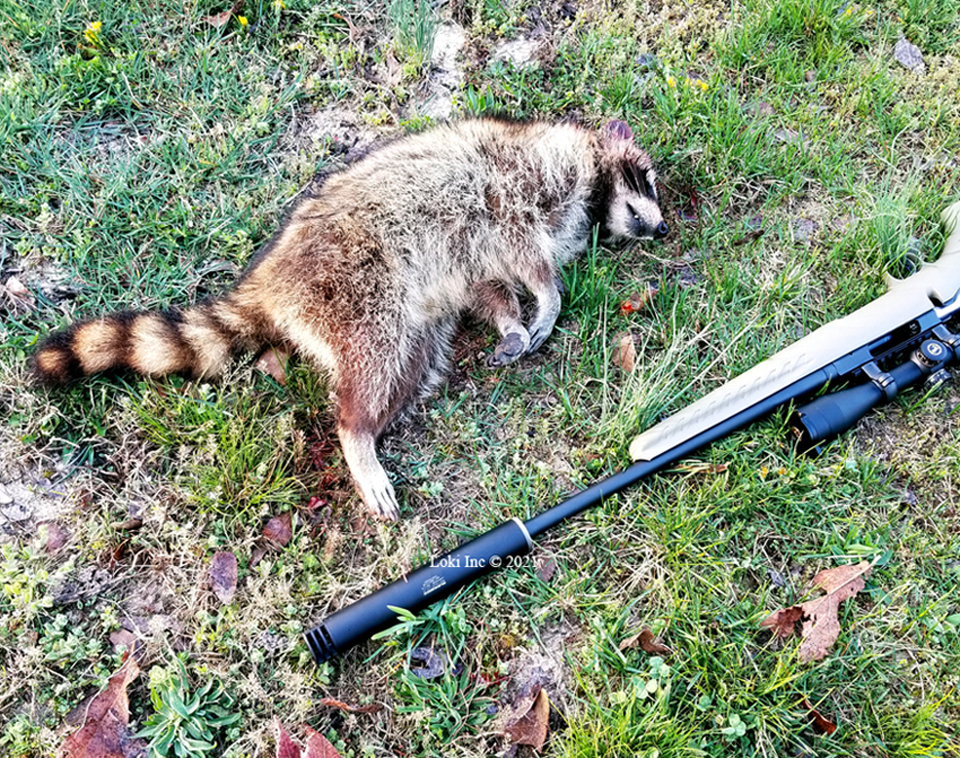
190 grain Sub-X®handload vs coon
After shooting armadillos, coons, possums, and skunks, I could tell no differences between the performances of factory ammunition versus my handloaded ammo. I was able to achieve one-shot kills in most cases, with no failures on the part of the projectiles.
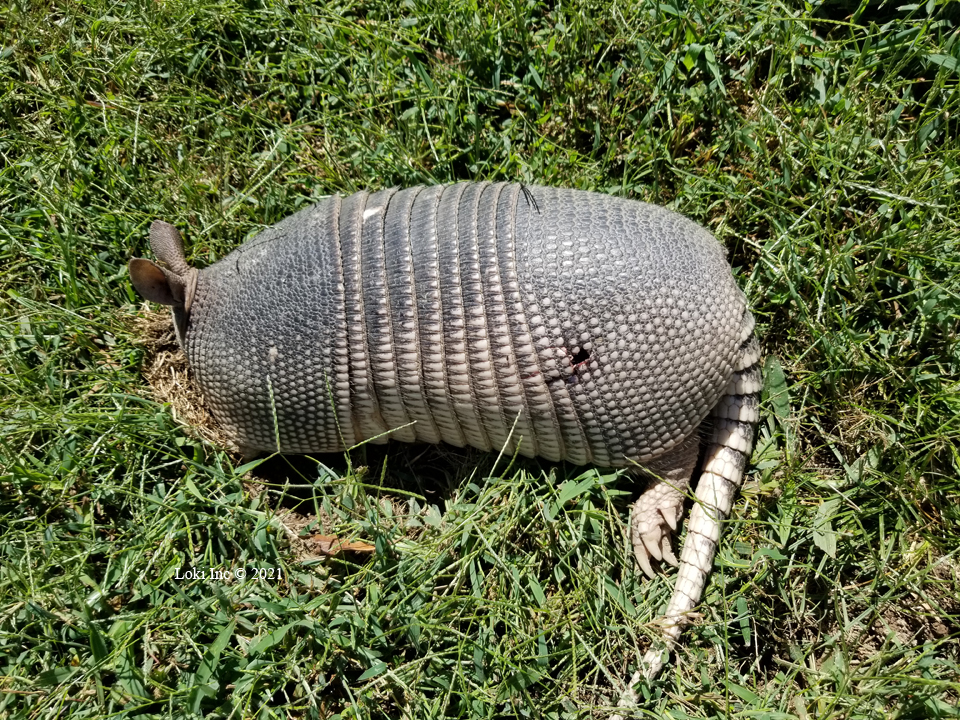
Entrance wound 190 grain Sub-X® factory ammo
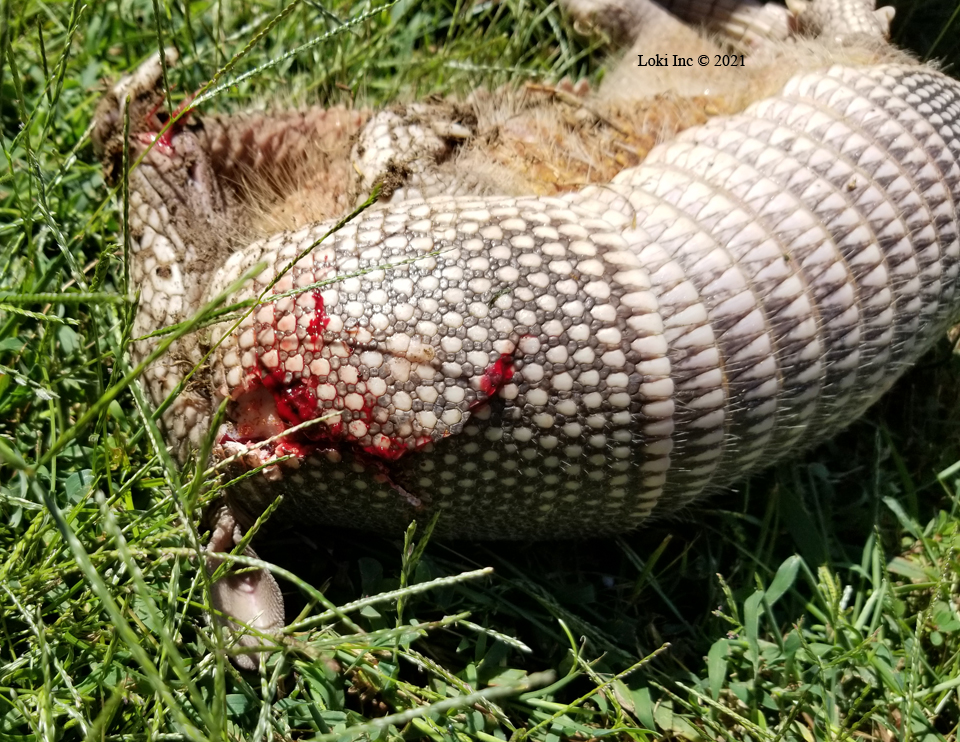
Exit wound 190 grain Sub-X® factory ammo
The “nut behind the butt” was responsible for any kills that required more than one shot. In several instances, the projectiles didn’t exit the varmint; where bullets did exit and I was able to recover them, they showed good expansion and mass retention.
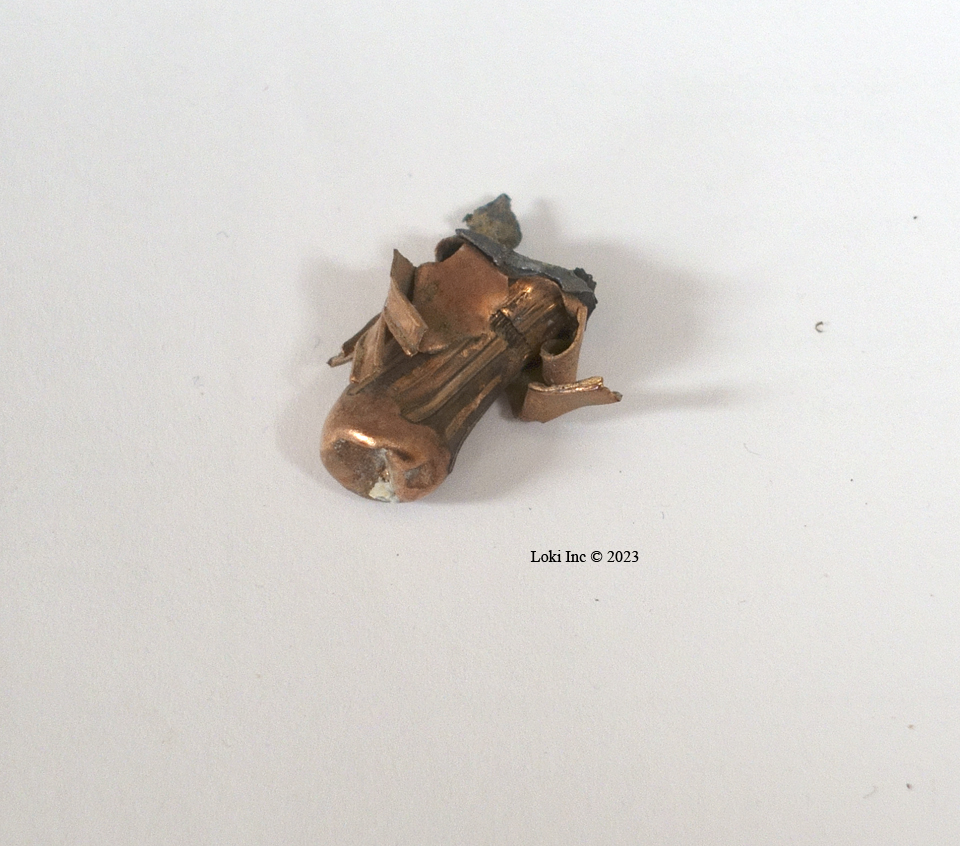
Recovered Sub-X® 300 AAC Blackout bullet
Conclusion
Hornady’s new Sub-X® ammunition and bullets for handloading fit perfectly into my .300 AAC Blackout concept – arming my quiet, suppressed bolt-action rifle with cartridges capable of accurately launching subsonic projectiles that expanded reliably on impact.
Visit Hornady online to see more about this ammunition and bullets.
Review: Mantis BlackbeardX Training System
You may have heard of one of the Mantis products, such as the Mantis X or the X10 Elite training systems, but Mantis recently released an upgrade to their Blackbeard AR-15 training system that combines the functionality of the Mantis X with the Blackbeard – hence, the BlackbeardX.
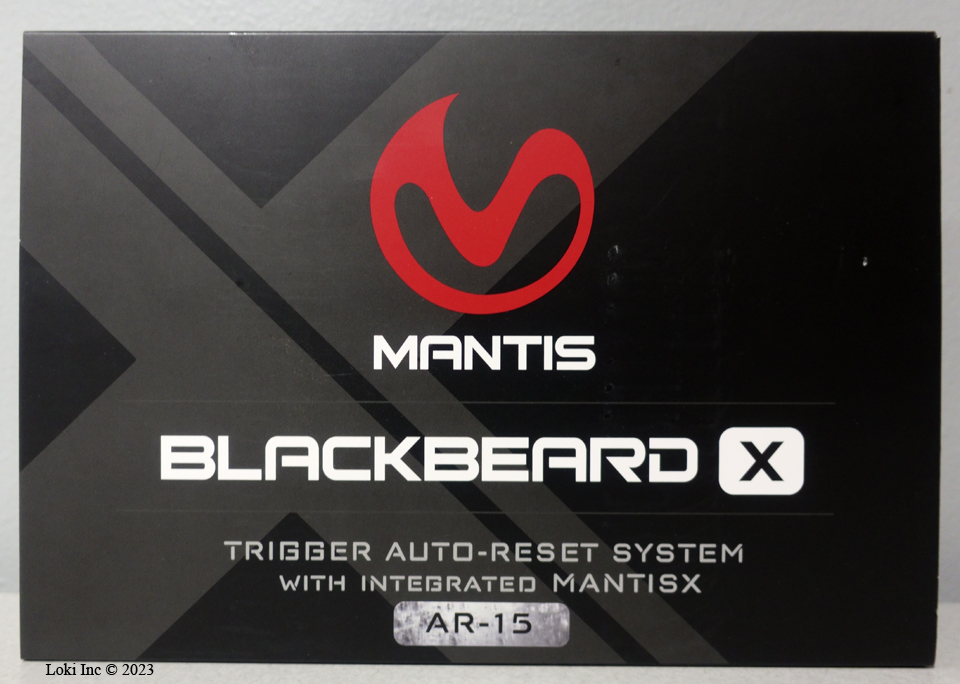
Front of Blackbeard X package
In a nutshell, the Mantis BlackbeardX allows you, as an AR-15 gun owner, to practice shooting indoors with instant feedback on how well you are doing. The original Blackbeard replaced your AR (rifle or pistol) system’s bolt carrier group (BCG) and charging handle with a single part that allowed dry fire without charging (pulling back the charging handle, sliding it forward to engage, then releasing the bolt) or changing the trigger weight or feel. The system’s rechargeable battery pack resembled a 30-round magazine, and installed in the magazine well the same as a real magazine. The new BlackbeardX retains the functionality and appearance of the Blackbeard, but adds a laser-aiming spot and the Mantis X training system for immediate shot feedback. That feedback is from the laser spot on your target with each of your trigger pulls, and through the Mantis X system app on your portable device (cell phone, etc.). A fantastic feature of the original Blackbeard that is retained in the X version is that you don’t have to charge the gun after every trigger pull – the system automatically re-cocks the hammer after each shot!
Of course, if you had the Mantis X, you could have attached it to the forend of your AR to take advantage of that mobile device application-driven training system for live fire training, as well as dry fire training. You would have had to recharge the gun between shots during dry fire, however, and you wouldn’t have the laser spot for shot feedback (or to use with the Mantis Laser Academy).
Mantis Blackbeard X Training System
What Mantis has done with the BlackbeardX is bring similar convenience and capability to your long gun as they created for your guns through the Mantis X10 Elite system. See my review of the X10 Elite for the details of how it opens a new world of shooting training to a user, without the expense of ammunition and trips to the range. The major difference between the BlackbeardX and X10 Elite systems is the Blackbeard system, as detailed above, replaces the bolt carrier group and charging handle of the AR-type firearm, whereas the X10 Elite mounts externally to the gun. Therefore, you can use the X10 Elite for dry fire as well as live fire, but the Blackbeard is for dry fire only. Of course, when you get ready for live-fire drills, replace the BlackbeardX with your BCG and charging handle, mount an X10 to your AR and head to the range.
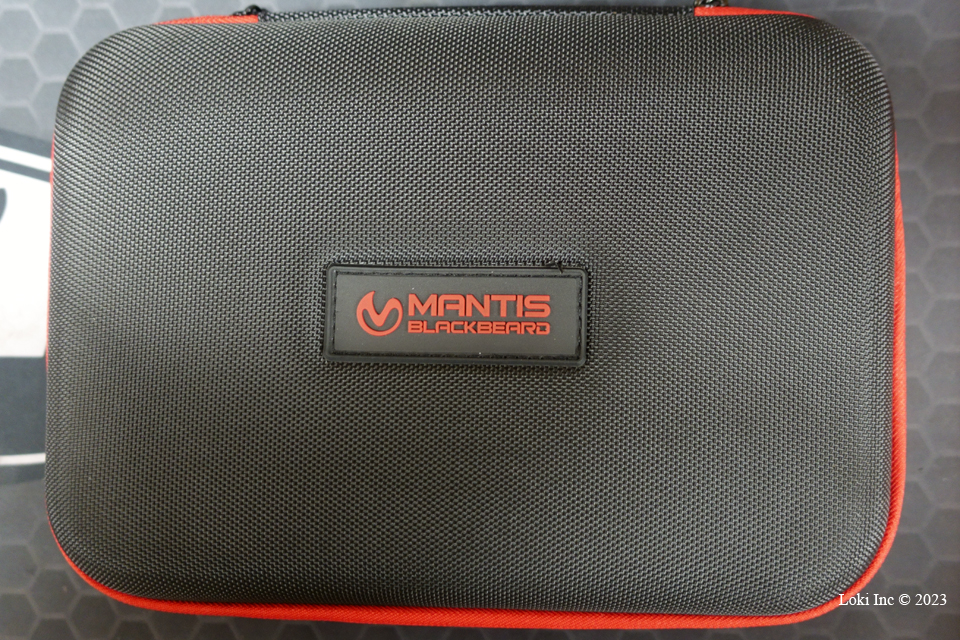
Blackbeard X system travel case
The BlackbeardX is packaged in what I call a travel case, as it is robust, zippered and compartmented. Inside the case, the “magazine” and charging handle/BCG device have their own separate cutouts in the foam lining, with the quick start sheet and laser academy information residing in an enclosure in the case “lid” along with the USB cable for charging the battery.
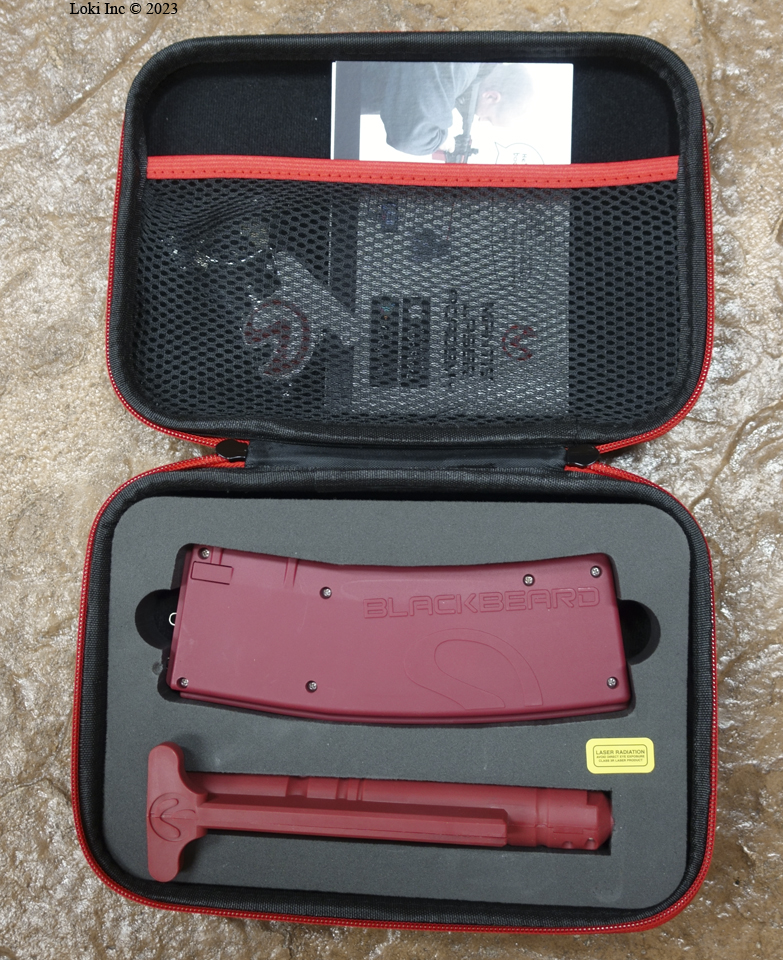
Blackbeard X system in travel case
The system battery and Bluetooth components are in the magazine; it is a good idea to charge the batteries before using the system the first time.
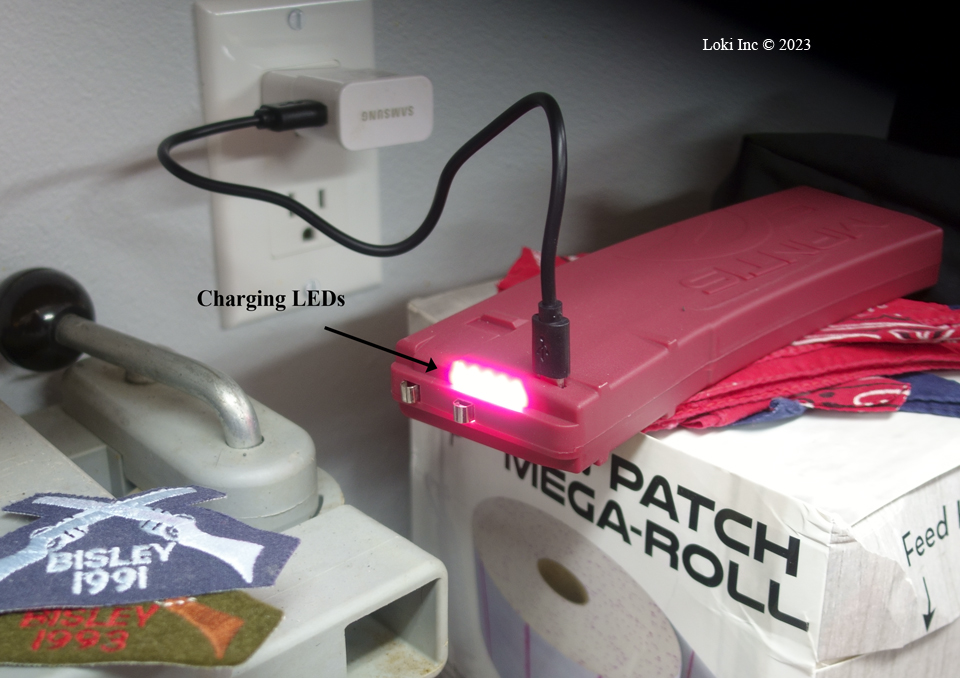
Blackbeard X battery pack charging
The batteries in the BlackbeardX I received were nearly dead, and required a bit of time to recharge as indicated by a series of lights across the top of the magazine. The more lights that are illuminated, the closer the pack is to a full charge. While you are waiting for the battery pack to charge, you can get your AR ready and install the charging handle/BCG device into it.
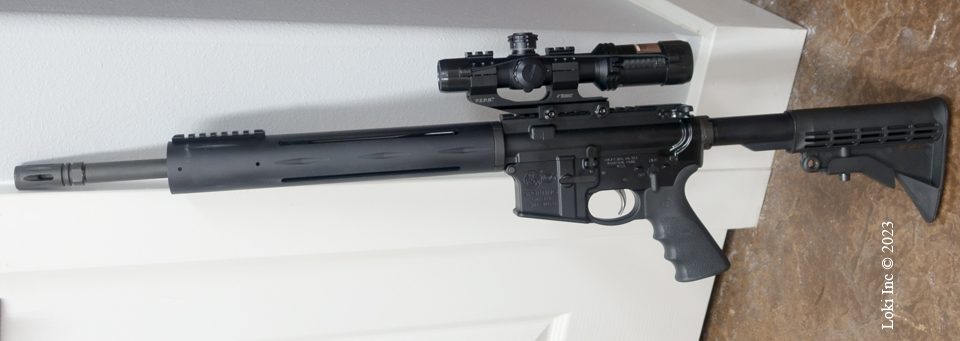
Colt AR ready for Blackbeard X
I chose to use a Colt Sporter AR-15 as my rifle for this review, but the system should fit into any AR-15 pattern firearm, rifle or pistol.
Installing the Mantis BlackbeardX
Double-check that the gun is clear, with no ammunition in your work area. You won’t need a magazine, of course. After clearing the weapon, use the correct procedure to remove the charging handle and BCG – pull back on the charging handle, cocking the gun, and then lock the charging handle in the forward position. Release the bolt to go forward into battery, but do not pull the trigger because the hammer needs to be in the rear, cocked, position prior to removing the takedown pin or pins.
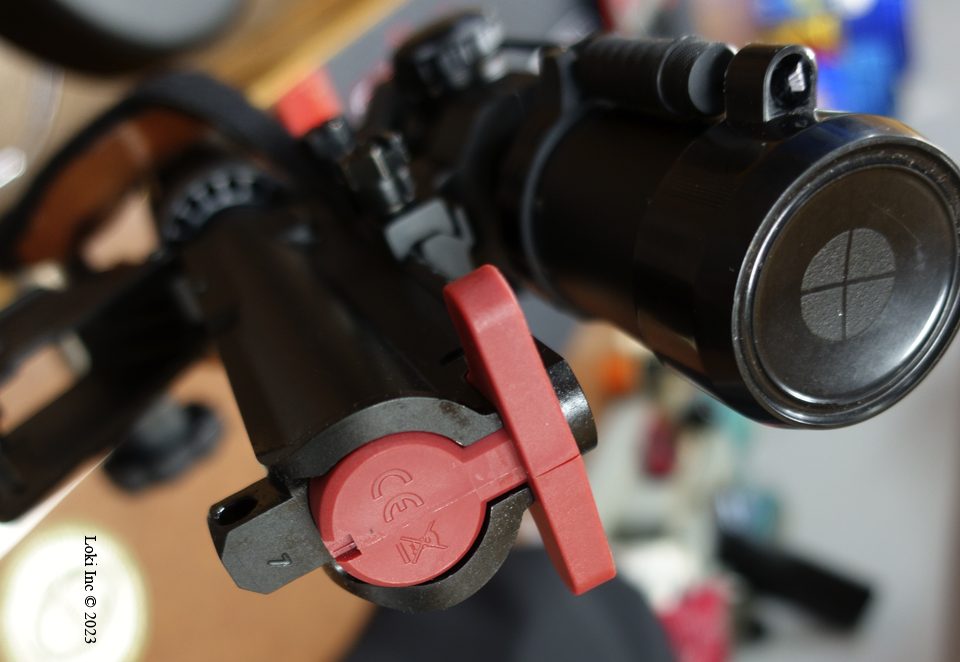
Rifle with Blackbeard X upper unit installed
Open the upper receiver, remove the charging handle and BCG, insert the BlackbeardX replacement, close the upper receiver back to its position on the lower receiver and pin it.
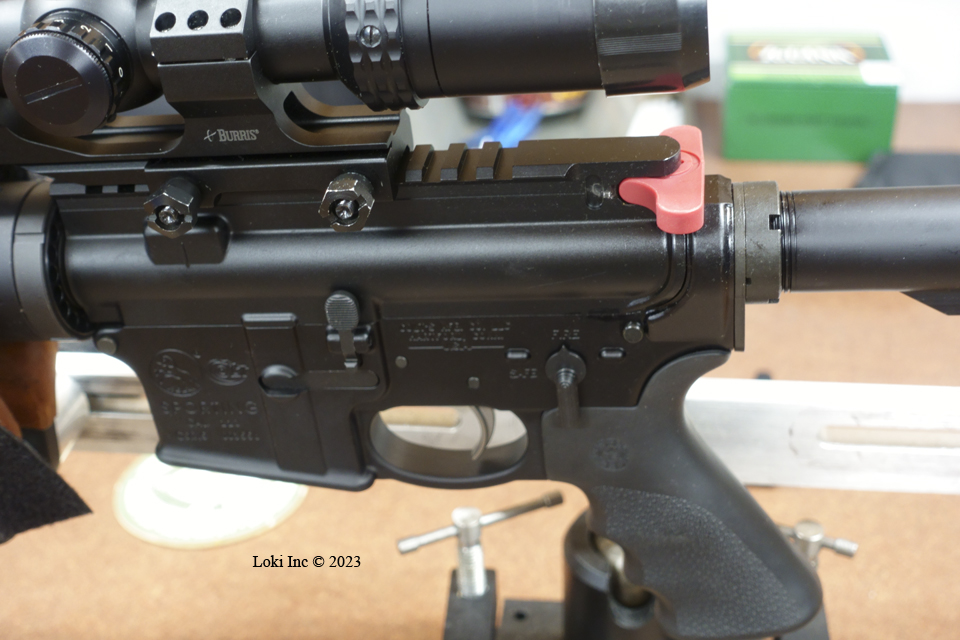
Left side view of rifle with Blackbeard X upper unit installed
When the battery pack is charged, simply insert the BlackbeardX magazine into the magazine well of the gun; make sure it is firmly seated. Before using the system, install the free Mantis smartphone application on your mobile device and get ready to pair your device with the BlackbeardX.
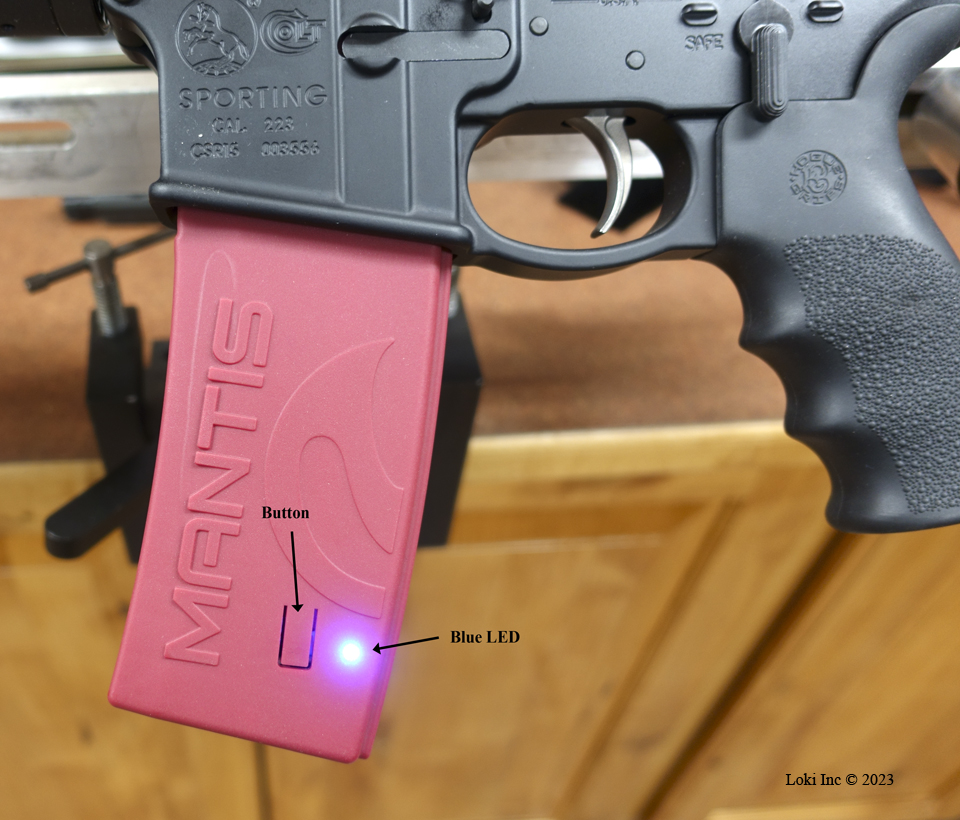
Side view of Blackbeard X magazine installed, showing power button and blue LED for Bluetooth
Fire!
When you are ready to use the system, press the power button on the lower left side of the magazine to turn-on the BlackbeardX. Be sure the LED on the side of the magazine near the power button turns-on. At that point, you can Bluetooth pair the Blackbeard X with your mobile device. Once your device and the BlackbeardX are paired, you are ready to use the system.
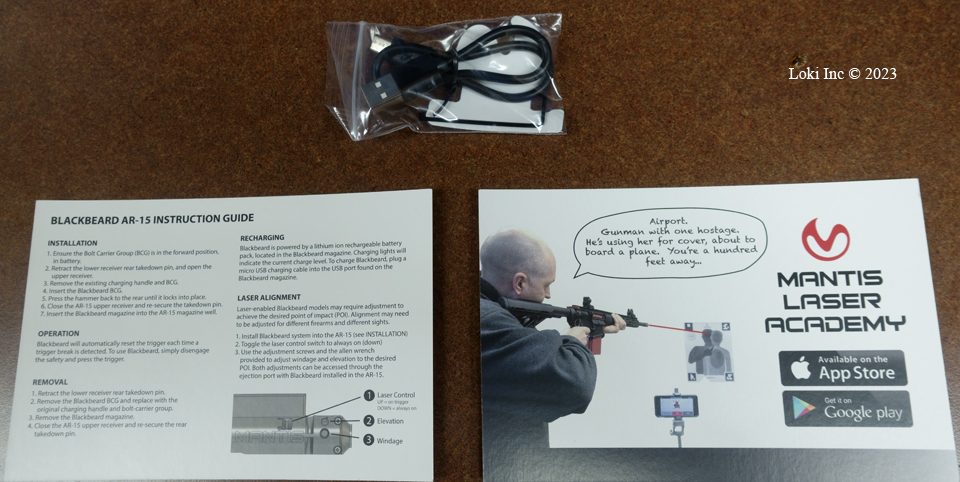
Blackbeard X instructions, cable, laser academy information
To recap a bit of my earlier review, once you upload the Mantis X application and create the Bluetooth connection to the Mantis system (BlackbeardX or X10 Elite) installed in/on your firearm, you can access many different scoring and training programs on the app. The Mantis sensors precisely detect movements of the gun and track those motions for a very brief time, as you pull the trigger until it breaks. As the tracking takes place, the gun unit transmits that information to the app. This allows the app to integrate gun pointing and gun movement into information in its sub-applications.
In my review of the X10 Elite, I addressed the advantages of including dry-fire in your training regime. Saving ammo costs is really a minor part of it, believe it or not. The real advantages are the ways the MantisX system makes dry fire training much more useful and effective.
If you are serious about improving your AR marksmanship skills, be sure to add effective dry fire to your training workouts, and be sure to add the BlackbeardX to your AR system!
Learn more about the Mantis BlackbeardX. MSRP: $319
Review: Mantis X10 Elite
The Mantis X10 Elite combines the utility of each Mantis X model into a single system, and the X10 Elite works with pistols, shotguns, rifles, and bows. It uses the same Mantis X application (updated from the original as per most apps) as the original system. The X10 Elite incorporates a simplified method of attachment to the firearm versus the original Mantis X that I have, and it is smaller and lighter than the Mantis X. It appears to have increased sensitivity, as it didn’t drop any of my dry fire shots as the original device did every once in a while. I found it an excellent aid for dry firing in particular.
Wow! It figures – for whatever reason, rising crime, Sleepy Joe, etc., a lot of us in the US have been buying guns recently. Moreover, for whatever reason, the ammunition to go along with those guns is scarce and expensive. What is a shooter to do? The conventional wisdom is to dry-fire your guns, even every day — particularly the guns that you may depend on to defend yourself or your family. Dry firing requires no ammunition (in fact, one must dry fire with no ammo in the gun or anywhere nearby), and it can be done in a safe area in your home, garage, shop, etc.
Unfortunately, unless you had some basic gun handling and marksmanship training, dry firing practice with a handgun is nearly useless. In fact, it may be harmful to your shooting skills.
Why? Unless you are very self-aware and are trained to use the correct sight alignment, grip, and trigger control, and can make a mental sight picture of where your gun is pointed and how the sights are aligned at the instant the trigger “breaks,” you do not have the skill necessary to self-criticize and correct problems with the aforementioned shooting skills. Without some way of telling, you are forming muscle memory habits that may become bad habits, making your dry-fire drills a waste of time or worse. The Mantis X10 Elite system is an aid to learning proper grip and trigger management.
How do I know? More than 40 years ago, I was a member of the US Air Force Academy Intercollegiate Pistol Team. As a teen living in a rural area, I learned gun safety from my dad, and he taught me basic marksmanship with a rifle and a shotgun. He admitted to having no pistol skills, so until I joined the team as a cadet, I had no training with handguns. Fortunately, our team coach was a pistol competitor in the Olympics and in the National Matches, and was an excellent teacher. I learned the above-mentioned skills from him, and they have since held me in good stead as the Officer-in-Charge of an RAF station shooting team, and as an NRA Certified Pistol Instructor.
Even though I already had these skills, I found the new Mantis system an effective aid to reinforce them, and a boon to dry fire practice.
In the long-ago and faraway times (so it seems) prior to the Covid uproar, I attended Shot Show. During my perusal of the multitude of booths and displays, I stopped at the Mantis booth and listened to their explanation of the shooting trainer device they called the Mantis X. I listened to the booth person’s explanation of the system, tried it on one of the neutered pistols they had at the booth, and decided to get one to use at home and on my range. The Mantis X system came with the rail-mounted sensor, a USB charging cable, Bluetooth connectivity, and a hard shell (Pelican-type) carry case. The sensor attached to a pistol rail with a screw clamp, and to holster the weapon I had either to remove the device or use a holster designed for a handgun with a light in the same mounted position as the Mantis X.
After that, I used a Mantis X off and on for several years, for personal training and for firearms testing, but I’ve found the Mantis X10 Elite is a definite upgrade to the older system. The X had problems tracking dry fire practice on some of my pistols, but so far, the X10 Elite system has not. The new system made my dry fire practice more useful and enjoyable, because I now had external feedback on my grip and trigger manipulation during the firing sequence. That’s one of the difficulties of dry firing without a coach or something like the Mantis system; with no feedback, if we aren’t already trained to recognize problems we will just keep clicking the trigger merrily away, possibly forming bad muscle memory habits. If we are trained already, we can lie to ourselves and accept poor gun handling as good follow-on training. The Mantis system helps prevent both situations.
So, what does the Mantis X10 Elite do? It precisely senses movements of the gun on which it is mounted, and captures those movements for a brief time as you move the trigger until it breaks. The gun-mounted sensor sends that information to the Mantis X application on your mobile device via Bluetooth, where the app massages the data to display gun pointing, gun movement and recoil information in the sub-applications. Pictures are worth many words, so I took some screenshots of a couple of my practice sessions, dry fire and live fire.
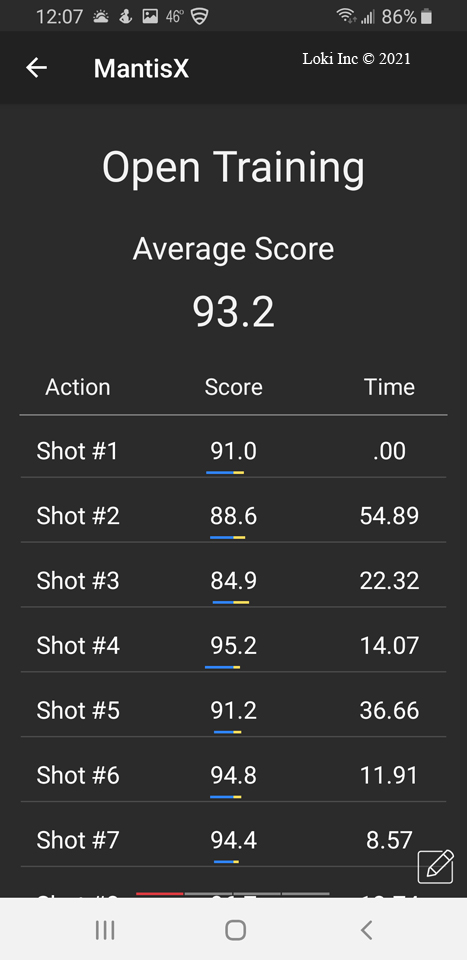
Mantis X application Open Training shot averages
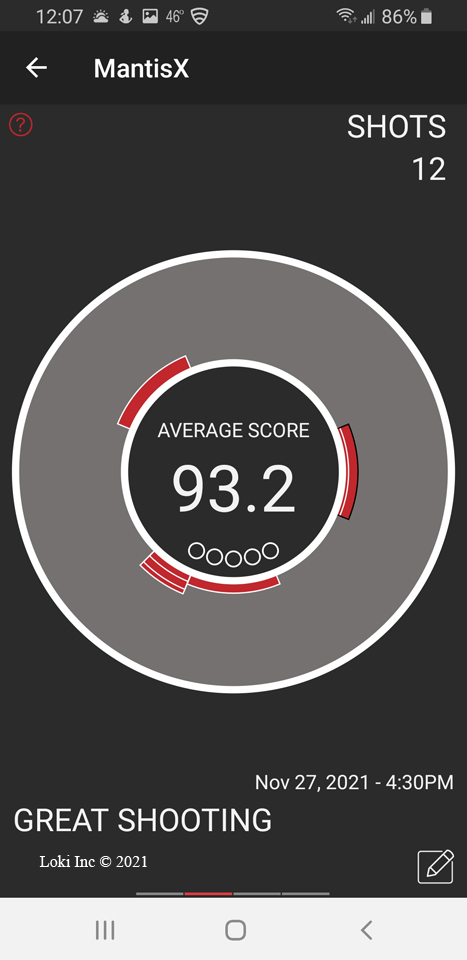
Mantis X application Open Training movement display
The application also presents several drills and courses that you can use as guides to your practice, including an introduction to the Mantis system that helps you learn to use the application.
Of course, the first time you use the application on your mobile device, you have to set it up. The setup, however, is simple and only takes a minute or two.
The instructions are located entirely within the application’s setup pages, and there are many videos on YouTube that might prove helpful if you have difficulties using the system.
I took a couple of photos showing a side-by-side comparison of the old Mantis X device versus the new Mantis X10 Elite system.
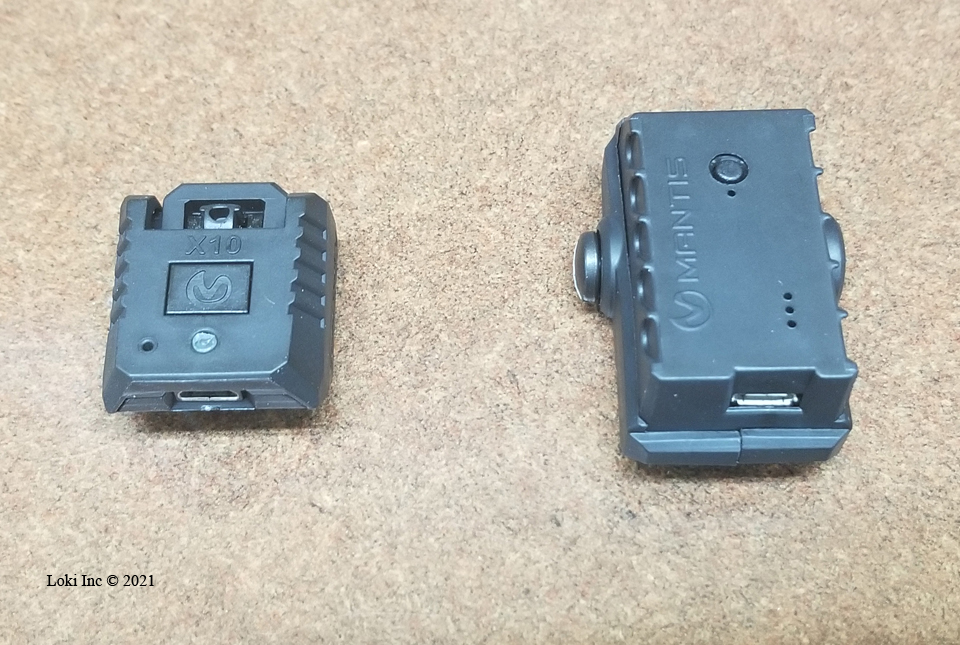
Mantis X10 (l) and Mantis (r) side-by-side comparison
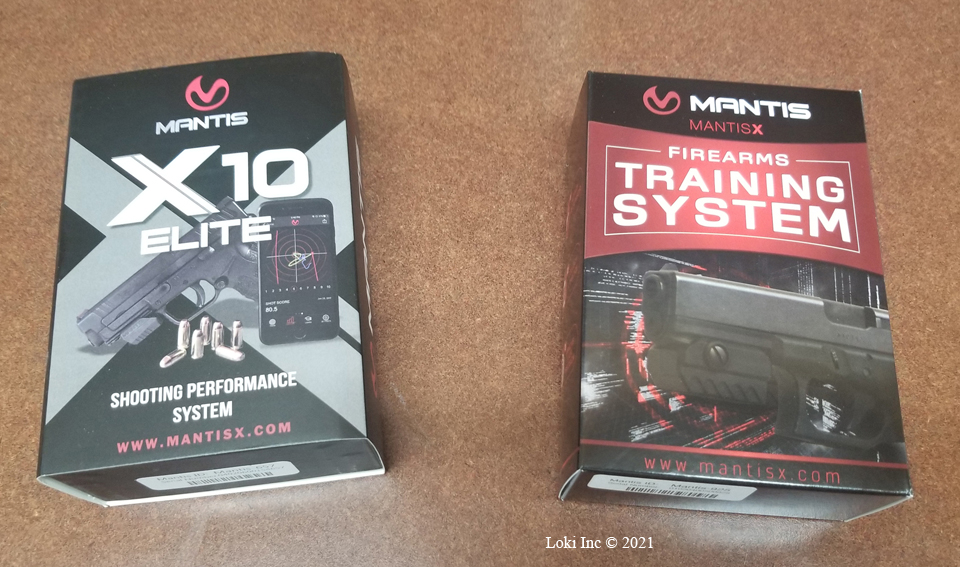
Mantis X10 and Mantis packages
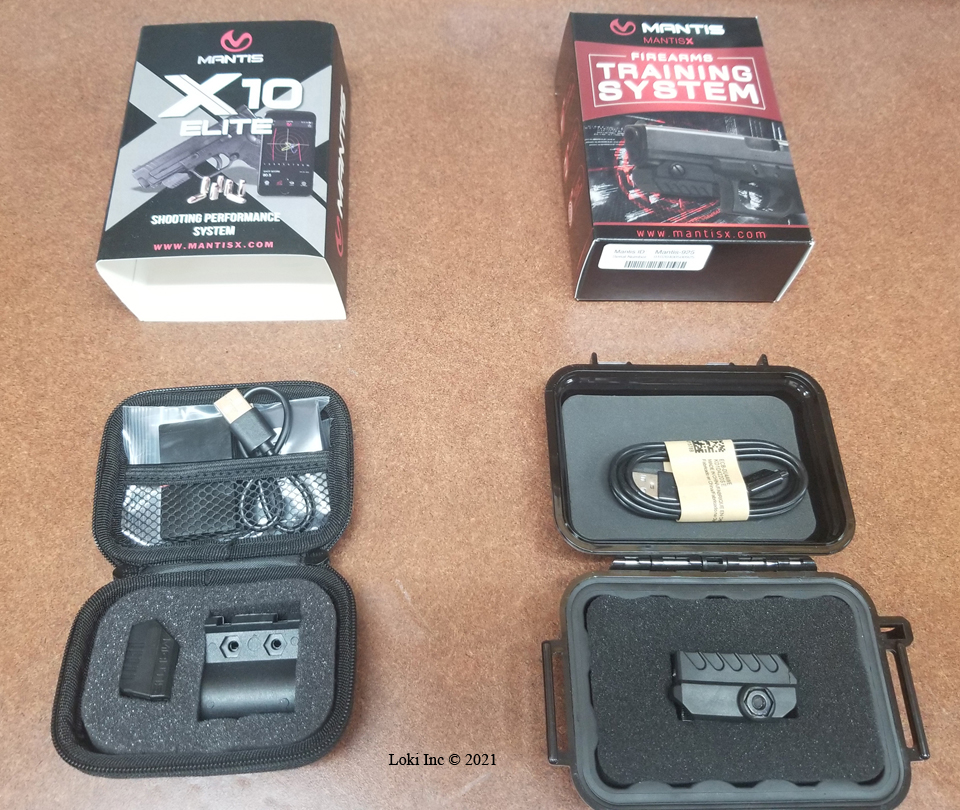
Mantis X10 and Mantis in their packages
Good things definitely come in small packages! I also took a couple of photos showing the original Mantis and the X10 device attached to the dust cover rail on one of my pistols, a SIG P220.
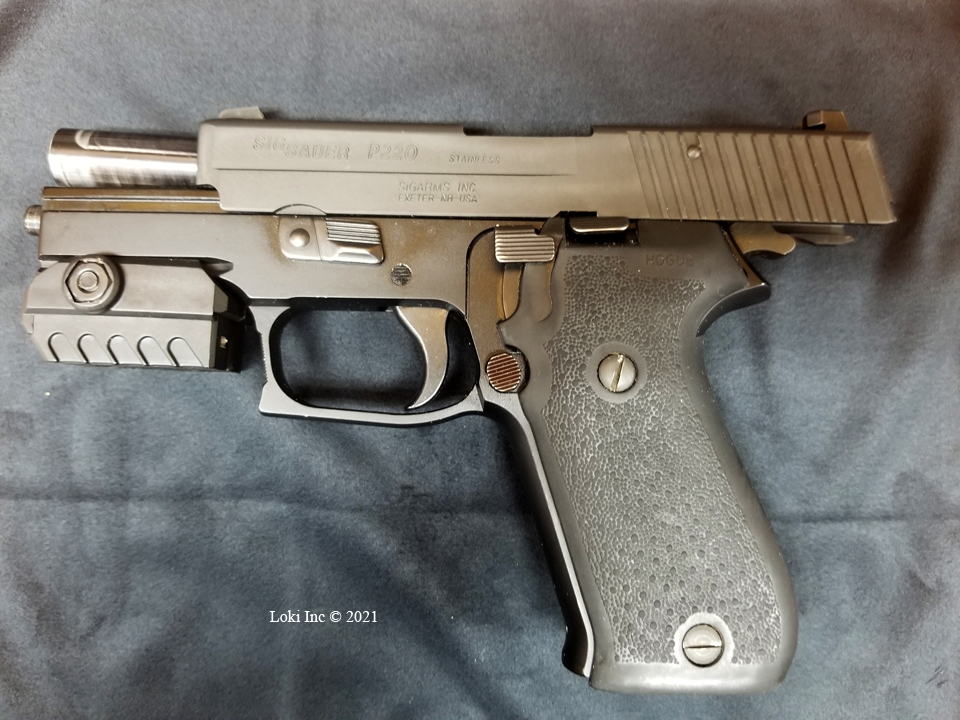
Left side of SIG P220 with Mantis
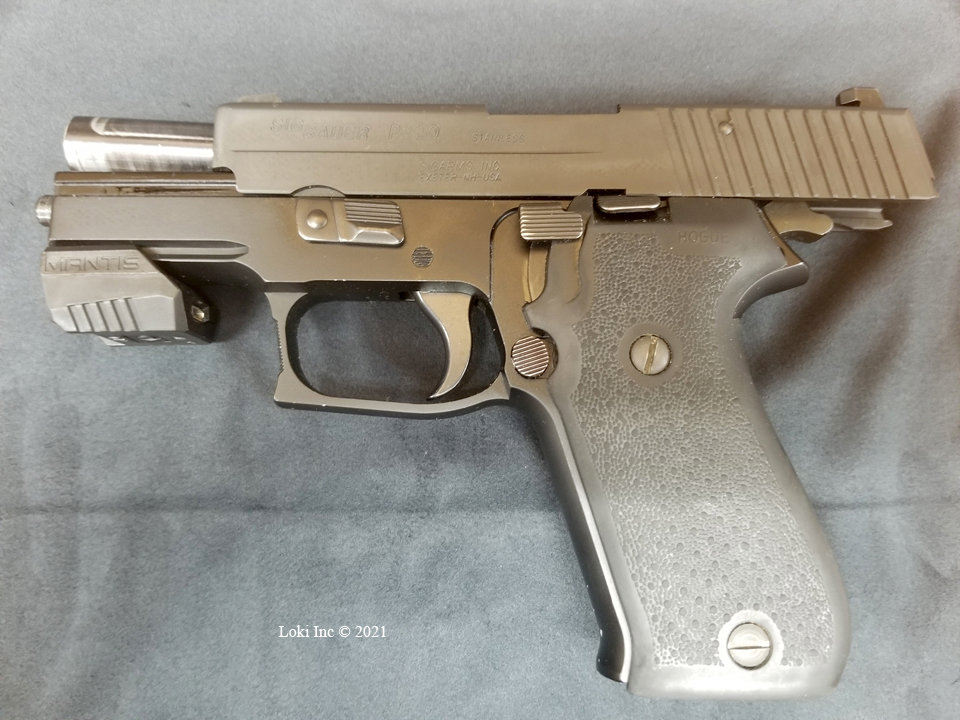
SIG P220 left side with Mantis X10
The Mantis X10 Elite system came with the sensor, a clamp and hardware useful for creating a mounting surface on a round part of a firearm, a USB cable, and a short section of Picatinny rail with attachment hardware.
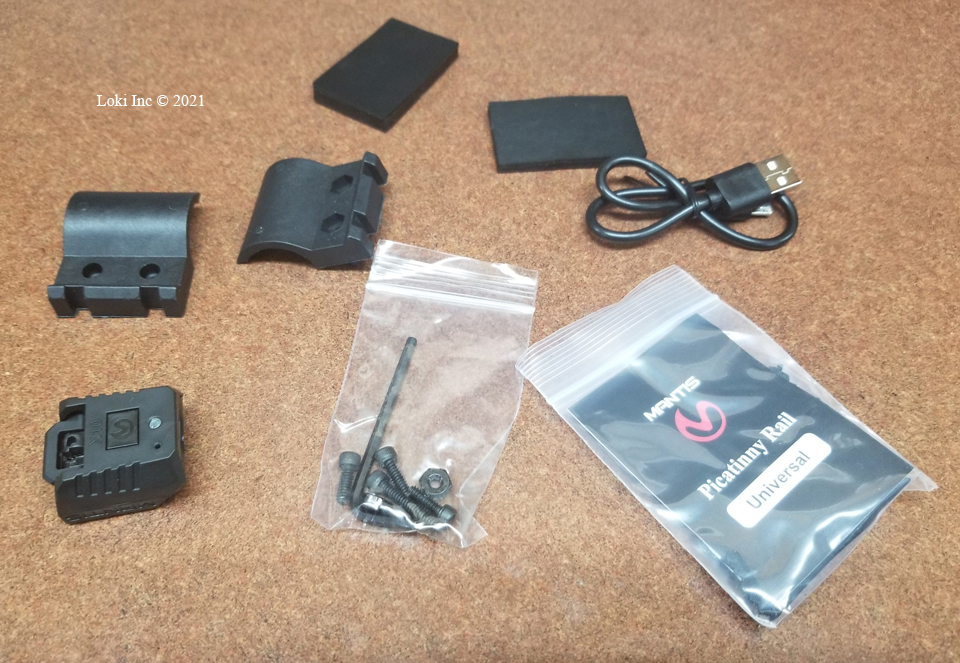
Included in the Mantis X10 package: Mantis X10, Picatinny Rail adapter and associated parts, USB cable
If your firearm already has a short rail section available in a good spot on the gun, you can attach the sensor directly to that rail section by merely pulling a spring-loaded lock out of the way while you slide the sensor onto the rail. Then, release the lock to secure the sensor in place.
So, if you want a great way to improve your dry fire practice during this dry spell of ammo availability, or if you have access to training ammunition, and you want a “coach” to give you grip and trigger manipulation feedback during live fire training, get a Mantis X10 Elite. Watch your shooting skills improve, even though Sleepy Joe would prefer you let them slide!